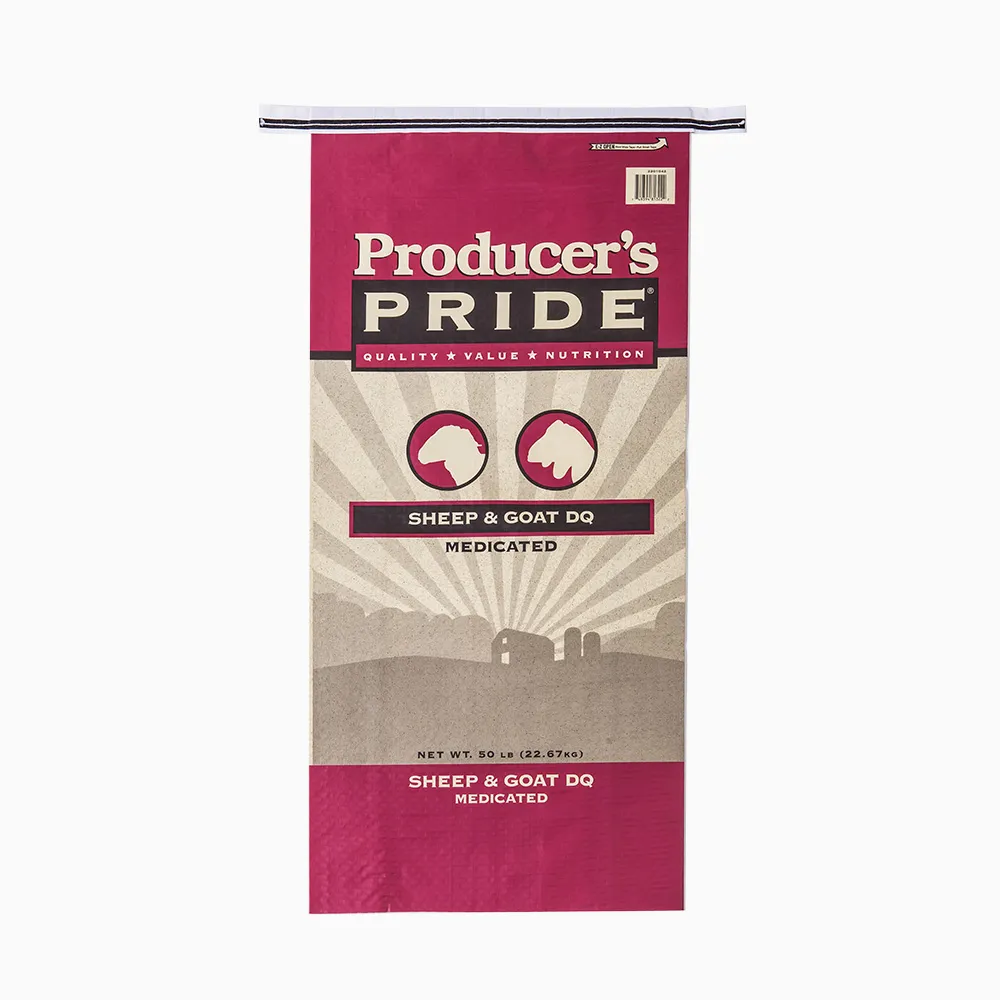
In today’s world, businesses are constantly looking for packaging solutions that combine strength, sustainability, and versatility. Poly-paper bags are one such solution that has gained significant attention due to their ability to offer the best of both worlds: the durability of polypropylene (PP) and the eco-friendly qualities of paper. This combination allows for a packaging solution that not only meets the demands of various industries but also addresses environmental concerns.
In this article, we will explore why Poly-paper sacks are becoming the go-to packaging choice for various sectors. We will also take a deep dive into the manufacturing process of these bags, emphasizing how cutting-edge technology from renowned equipment suppliers like Starlinger and W&H enhances quality and efficiency.
Why Choose Poly-paper Bags?
Poly-paper bags, also known as Kraft Paper Woven Bags or Kraft Paper PP Bags, are gaining popularity because they combine the benefits of two powerful materials: paper and polypropylene. Here are the key reasons why they are preferred for packaging:
- Strength and Durability
Poly-paper bags offer an exceptional combination of strength, durability, and resistance to wear and tear. The outer layer of kraft paper provides rigidity, while the inner polypropylene layer enhances its tear resistance and strength, ensuring the bag can withstand heavy loads and rough handling during transportation and storage. - Eco-friendliness
The combination of paper and PP helps meet the demand for sustainable packaging solutions. Paper is biodegradable and recyclable, while polypropylene is durable and reusable. This mix of materials results in a packaging solution that has minimal environmental impact compared to traditional plastic bags. - Moisture Resistance
One of the main benefits of Kraft Paper Woven Sacks is their inherent ability to resist moisture, making them ideal for packaging products like food, chemicals, and construction materials. The paper’s fiber structure offers a natural barrier to water, while the PP interior layer provides additional moisture resistance. - Customizability
These bags can be easily customized with different designs, sizes, and features to meet the specific needs of businesses. Whether it’s printing a brand logo, adding valves, or changing the bag size, Kraft Paper Woven Bags are highly adaptable for various industries. - Versatility in Application
Poly-paper sacks can be used in a wide range of industries, including agriculture, food, chemicals, and construction. Their ability to hold a variety of products, from grains to fertilizers, and even chemicals, makes them a versatile packaging option.
For more on how these Poly-paper bags can transform packaging solutions, check out this detailed guide on Poly-paper Bags.
The Manufacturing Process of Poly-paper Bags
The production of Kraft Paper Woven Bags involves several critical stages, each contributing to the final product’s quality and durability. Below is a breakdown of the key steps in the manufacturing process.
1. Extrusion and Drawing
The process begins with the extrusion of polypropylene resin. This is the foundation for the Kraft Paper PP Bag. The resin is heated and forced through a die to form a sheet or film. This stage is crucial because the quality of the PP film dictates the strength and durability of the bag.
After extrusion, the PP material undergoes a drawing process, where it is stretched to align the polymer chains, further enhancing the strength of the material. The extrusion process ensures that the final product has a smooth surface for printing and coating, making it ideal for customization.
2. Weaving
Once the polypropylene film has been extruded and drawn, it is woven into fabric using high-tech circular looms. These looms, often supplied by renowned manufacturers like Starlinger, ensure precision and efficiency in weaving. This stage creates the woven fabric that forms the core structure of the Laminated Woven Bags.
The fabric’s density and pattern can be tailored to meet specific needs, depending on the load the bags will carry and the environment in which they will be used. For example, bags designed for agricultural products may require tighter weaves to prevent leakage, while those for chemicals may need a more robust structure to resist punctures.
3. Lamination
After the polypropylene fabric has been woven, it is laminated with kraft paper using advanced lamination techniques. This is a critical step in the production of Kraft Paper Woven Sack. The lamination process bonds the kraft paper to the woven PP fabric, creating a robust, yet lightweight packaging solution.
The lamination process helps to provide additional benefits such as:
- Increased moisture resistance
- Improved strength
- Better print quality for branding
This two-layer construction is highly effective in protecting the contents from external elements, particularly in outdoor or industrial environments.
4. Printing
Printing is an essential step for businesses looking to customize their packaging. The lamination process ensures that the Kraft Paper PP Bags retain a smooth surface for printing. High-quality flexographic printing presses, like those from W&H, are used to add logos, designs, and other brand elements.
This step not only enhances the bag’s visual appeal but also ensures that the bags are easy to identify in a warehouse or store setting, aiding in inventory management.
5. Bag Conversion and Finishing
Once the laminated fabric is ready, it is cut and converted into bags. The bag conversion process includes the addition of features such as valves, gussets, or reinforced stitching, depending on the bag’s intended use. The final step involves quality checks to ensure that the bags are defect-free and meet industry standards. These checks focus on ensuring that each bag has the correct dimensions, strength, and appearance.
At this stage, the Kraft Paper Woven Bags are ready for distribution and use in various industries. Their durability and customizability make them highly sought after for packaging needs across the globe.
Advantages of Starlinger and W&H Technology in the Manufacturing Process
The equipment used in the production of Poly-paper bags plays a significant role in ensuring the quality and efficiency of the final product. At VidePak, we rely on cutting-edge technology from global leaders like Starlinger and W&H to enhance every step of the process.
- Starlinger Circular Looms
Starlinger’s circular looms are renowned for their precision and efficiency in weaving polypropylene fabric. These looms are capable of producing high-quality woven fabric at high speeds, ensuring that our Kraft Paper Woven Bags maintain consistent strength and reliability. - W&H Lamination and Printing Machines
W&H’s advanced lamination and printing machines enable us to produce Laminated Woven Bags with excellent print quality and durability. Their technology ensures that the kraft paper and polypropylene are bonded seamlessly, providing a smooth surface for high-quality branding and enhancing the overall strength of the bags. - High-Efficiency Production
With the combination of Starlinger and W&H equipment, we achieve higher production efficiency and consistency in the quality of each bag. This allows us to offer our customers a superior product with minimal environmental impact, as the machines are designed to reduce material waste and energy consumption.
Product Parameter Table
Product Type | Material | Weight Capacity | Size Options | Printing Options | Applications |
---|---|---|---|---|---|
Poly-paper Bags | PP + Kraft Paper | Up to 50kg | Custom sizes | Flexographic | Agriculture, Food, Chemicals |
Kraft Paper Woven Bag | Kraft Paper + PP | Up to 60kg | Custom sizes | Flexographic | Food, Fertilizers, Feed |
Kraft Paper PP Bag | Kraft Paper + PP | Up to 40kg | Custom sizes | Flexographic | Construction, Chemicals |
Laminated Woven Bags | PP + Kraft Paper | Up to 50kg | Custom sizes | Flexographic | Food, Chemicals, Retail |
For a more detailed discussion on the versatility and production process of Kraft Paper Woven Bags, read further on Kraft Paper Woven Bags.
Conclusion
The demand for Poly-paper sacks continues to rise as more industries recognize the benefits of combining the strength of polypropylene with the eco-friendliness of paper. The manufacturing process, which involves extrusion, weaving, lamination, printing, and bag conversion, is greatly enhanced by state-of-the-art technology from Starlinger and W&H. These technological advancements ensure that our Kraft Paper Woven Bags are of the highest quality, offering both durability and sustainability. Whether for food, chemicals, or agricultural products, Kraft Paper Woven Sacks offer a reliable and eco-friendly packaging solution for businesses worldwide.