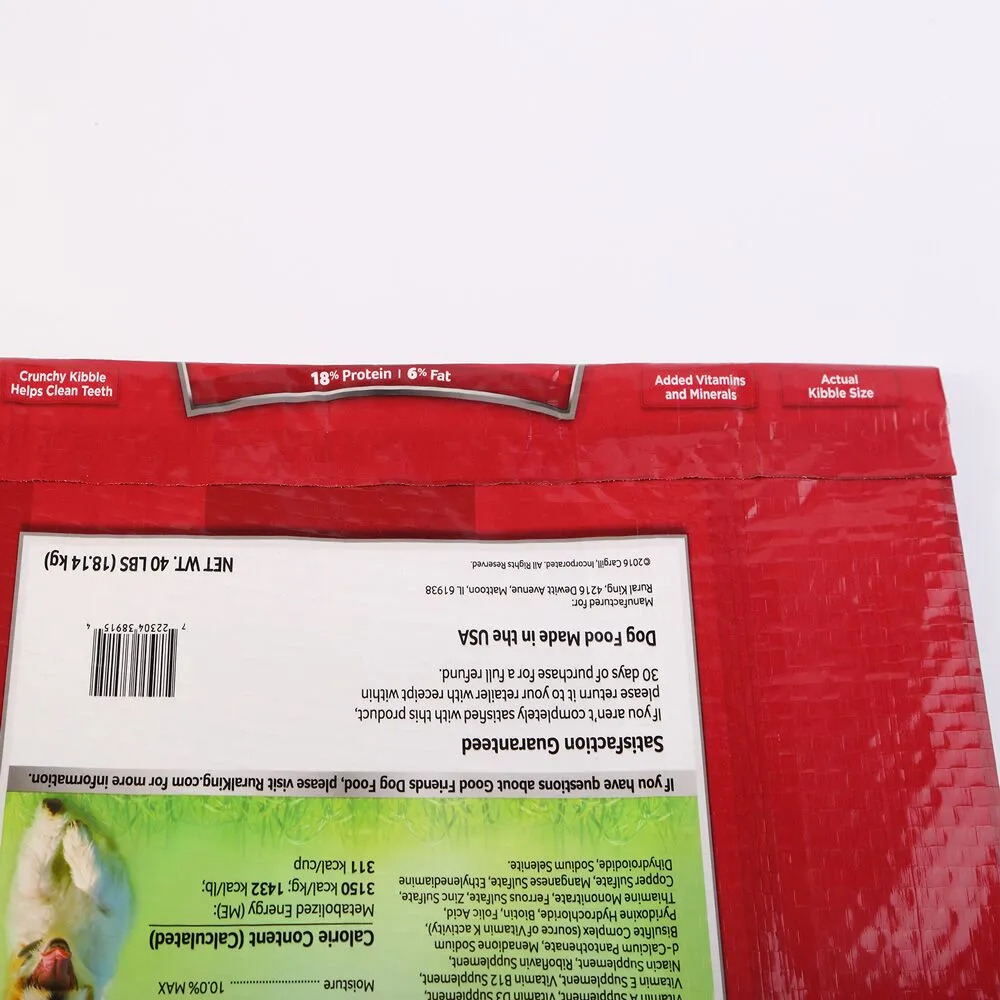
Block BOPP bags are rapidly becoming the go-to solution for various industries requiring durable, flexible, and cost-effective packaging. These bags, also known as Block Bottom Woven Bags or Block BOPP sacks, are particularly recognized for their high strength and versatility. In today’s competitive global market, achieving consistent product quality and efficiency in production processes is crucial. VidePak has addressed these needs by implementing state-of-the-art technology, sourced from globally renowned equipment suppliers like Starlinger and W&H, throughout its manufacturing stages.
What Are Block BOPP Bags?
Block BOPP Bags, often referred to as Block BOPP sacks or Block Bottom Woven Bags, are woven polypropylene (PP) bags with a unique block-bottom construction that ensures greater stability and allows them to stand upright on their own. This design is ideal for bulk packaging of products like chemicals, powders, food, and construction materials. Their structure provides ease in storage, stacking, and transportation, offering an effective packaging solution for both industrial and retail use.
The Block Bottom design also ensures that these bags are able to hold heavier loads without compromising on structural integrity. This makes them ideal for heavy-duty applications, providing a more secure alternative to traditional open-mouth or valve bags.
The following table outlines the typical parameters of Block BOPP Bags and their benefits:
Property | Block BOPP Bags | Block Bottom Bags | Block Woven Bags |
---|---|---|---|
Material | BOPP (Biaxially Oriented Polypropylene) | Polypropylene (PP) | Polypropylene (PP) |
Construction | Woven + BOPP Film | Woven polypropylene | Woven polypropylene |
Design | Block Bottom, Stand-up | Block Bottom | Block Bottom |
Strength | High tensile strength | Strong, durable | Strong, durable |
Load Capacity | Heavy-duty | Heavy-duty | Heavy-duty |
Customization | Multi-color printing, custom sizes | Custom sizes, coatings | Multi-color printing, custom sizes |
Applications | Chemical powders, grains, animal feed, construction materials | Agriculture, chemicals, food | Chemicals, food, grains |
Environmental Impact | Recyclable | Recyclable | Recyclable |
Seal Type | Heat-sealed | Heat-sealed | Heat-sealed |
Shelf Stability | High (stands upright) | High (stands upright) | High (stands upright) |
Why Choose Block BOPP Bags?
- Durability and Strength
Block BOPP Bags are known for their superior tensile strength. Unlike traditional bags that may easily tear under stress, Block BOPP sacks can handle heavier loads and are resistant to damage during handling and transportation. This makes them an ideal choice for packaging heavy or bulk products, such as fertilizers, seeds, and various powders. - Enhanced Stability
One of the standout features of Block Bottom Woven Bags is their ability to stand upright, even when filled. This feature not only makes it easier to pack and store products but also provides better stacking capability in warehouses, saving valuable space. - Excellent Barrier Properties
Block Woven Bags often come with added layers of protection. These bags can be laminated with BOPP film, which enhances their ability to resist moisture, dust, and other environmental elements. This makes them particularly suitable for products that need to be kept safe from external contaminants, such as chemicals or food items. - Customization Options
VidePak offers extensive customization options for Block Bottom Bags. From custom sizes and designs to multi-color printing, businesses can tailor these bags to meet their branding needs or specific functional requirements. The bags can also be reinforced with coatings or additional layers to improve their barrier properties, further enhancing their suitability for specialized applications. - Cost-Effectiveness
Given their durability and strength, Block BOPP Bags offer a long-term solution that minimizes the need for frequent replacements. Additionally, the cost of production is highly efficient due to the automation and high-quality equipment used in manufacturing, which ensures consistency and reduces waste.
Advanced Equipment for Superior Production
The production of Block BOPP Bags at VidePak is driven by cutting-edge technology from two of the most respected equipment manufacturers in the industry: Starlinger and W&H. Each stage of production, from yarn extrusion to weaving, printing, coating, and lamination, utilizes the latest machinery to ensure that every bag meets the highest standards of quality and performance.
- Extrusion
The production of polypropylene yarn begins with the extrusion process. Using Starlinger’s top-of-the-line extruders, the polypropylene resin is heated and formed into fine threads that are then used to create the woven fabric. This ensures that the fabric used in the bags is both strong and flexible. - Circular Looms
The next step in the process is weaving the fabric. VidePak uses over 150 circular looms, provided by Starlinger, to weave the polypropylene yarn into a high-density, durable fabric. This fabric is the foundation of the Block BOPP Bags, providing the strength needed to carry heavy loads without breaking. - Printing
Block BOPP Bags can be customized with multi-color prints, logos, and branding messages. To achieve this, VidePak uses W&H’s advanced printing machines, which allow for high-quality, sharp prints on the woven surface. The printing process uses water-based inks that are safe for the environment and ensure long-lasting, vibrant designs. - Coating and Lamination
To further enhance the strength and durability of the bags, VidePak applies a coating of BOPP film to the woven polypropylene. This is done using advanced lamination machines, also sourced from Starlinger. The BOPP film gives the bags a smooth surface and provides an additional layer of protection against moisture and dirt. - Sealing and Packaging
Once the Block BOPP Bags are finished, they are heat-sealed at the top to prevent any spillage. The use of high-efficiency sealing machines ensures a secure seal that maintains the integrity of the bag throughout its lifecycle. These bags are then carefully packed and shipped to customers worldwide.
Applications of Block BOPP Bags
Block BOPP Bags are incredibly versatile and can be used across a wide range of industries. Some common applications include:
- Agriculture: For packaging grains, seeds, and fertilizers. The strong, durable structure of the bags ensures that products remain safe during transportation and storage.
- Chemicals: For packing chemical powders and other substances that require protection from the environment.
- Food: Packaging grains, sugar, flour, and other bulk food items. The BOPP film lamination helps preserve the freshness and quality of food products.
- Construction: For carrying construction materials such as sand, gravel, and cement. The added strength of Block BOPP Bags makes them the ideal choice for these heavy-duty applications.
By choosing Block BOPP Bags, businesses benefit from an advanced packaging solution that combines strength, flexibility, and customization. The use of state-of-the-art equipment ensures that each bag is produced to the highest quality standards, meeting the demands of the global marketplace.
Conclusion
The Block BOPP Bag is an essential packaging solution that offers exceptional strength, versatility, and performance. By leveraging advanced equipment and manufacturing techniques, VidePak has positioned itself as a leader in the production of these bags. Whether you are in agriculture, chemicals, food, or construction, Block BOPP Bags provide a reliable, cost-effective solution to meet your packaging needs. For more information on how these bags can benefit your business, visit the links below: