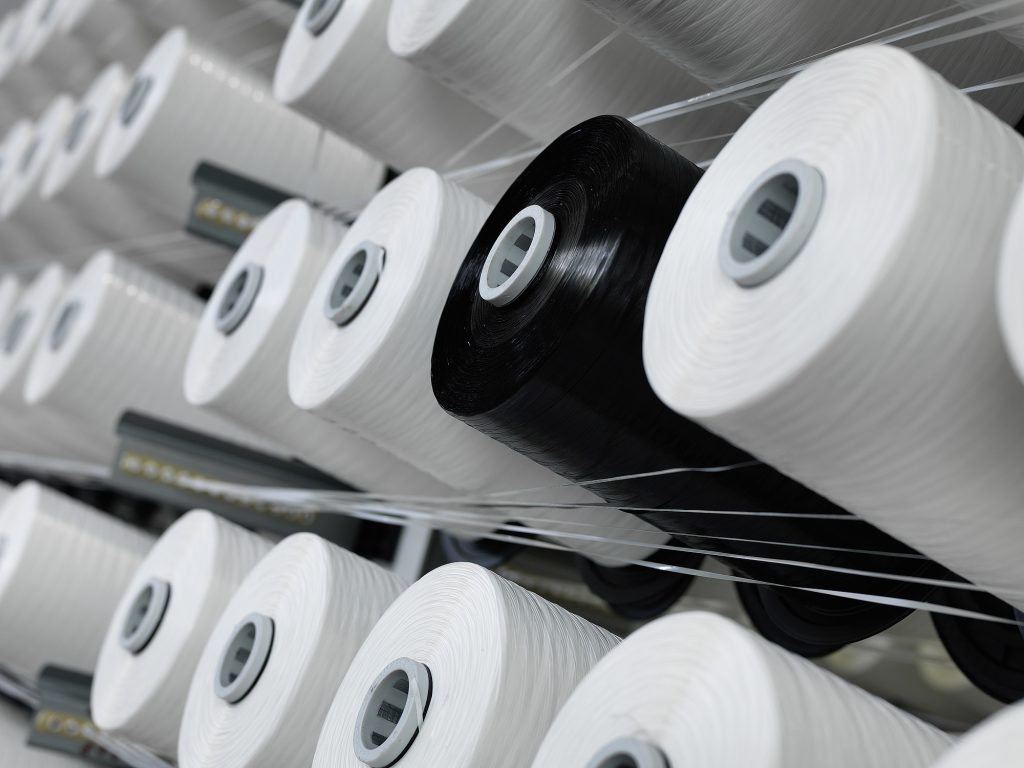
Block Bottom PP (Polypropylene) bags have redefined packaging with their combination of strength, efficiency, and sustainability. Their unique square-bottom design offers superior stacking, reducing space requirements and streamlining logistics. This report explores their applications, advantages, and how VidePak integrates sustainability into their production processes.
Block Bottom PP Bags: A Packaging Revolution
Block Bottom PP bags combine the best features of cartons and sacks. Their flat-bottom structure provides stability for stacking and storage, while their polypropylene material ensures strength and durability. These attributes make them indispensable in industries such as agriculture, construction, and chemicals, where reliable packaging is critical.
Advantages Backed by Design and Material
- Exceptional Strength:
Made with high-grade woven polypropylene, these bags resist tearing and punctures. The material’s tensile strength ensures safe handling, even for heavy or abrasive contents like cement or grains. - Optimized Storage:
The square-bottom design allows vertical stacking, maximizing space utilization in warehouses and transportation. This feature not only increases efficiency but also reduces costs. - Customizable Features:
Options like UV resistance, lamination for water resistance, and custom printing for branding make these bags versatile across various industries.
Innovations for Efficient Loading and Unloading
Efficient logistics rely on smart packaging solutions. Block Bottom PP bags are engineered to simplify handling, loading, and storage while maintaining product integrity.
Key Design Features:
- Anti-Slip Coatings: Prevent stacked bags from slipping, ensuring safe transport and storage.
- Reinforced Handles: Optional handles simplify manual handling during loading and unloading.
- Customizable Sizes: Tailored dimensions optimize pallet use, minimizing wasted space.
- Inner Liners: Protect moisture-sensitive products like fertilizers and chemicals, ensuring quality during storage and transport.
Feature | Benefit |
---|---|
Square-bottom design | Enhances stacking stability and reduces space usage |
UV resistance | Protects contents from sunlight degradation |
Lamination | Provides waterproofing for outdoor storage |
Customizable printing | Boosts brand visibility and product identification |
Industry Applications:
- Agriculture: Sturdy and moisture-resistant, ideal for grains, seeds, and fertilizers.
- Construction: Handles heavy-duty loads like cement and sand, ensuring safe delivery.
- Chemicals: Inner liners protect sensitive materials, maintaining product integrity under varying conditions.
Sustainability at VidePak: ESG in Action
VidePak’s production processes align with ESG (Environmental, Social, and Governance) standards, emphasizing sustainability, worker welfare, and efficient management. These principles are embedded in every stage of their operations.
Environmental Initiatives:
- Solar Power Integration: A 2MW rooftop solar system powers factory operations, reducing carbon emissions and reliance on non-renewable energy.
- Recyclable Materials: Products are made using recyclable polypropylene, promoting a circular economy and minimizing environmental impact.
Social Responsibility:
- VidePak supports education and better living conditions for children in underprivileged labor families, fostering community development and equality.
Effective Management:
- The adoption of the 5S management system ensures workplace safety, operational efficiency, and consistent quality control. This approach underscores VidePak’s commitment to precision and excellence.
Discover more about VidePak’s alignment with ESG standards.
Towards a Sustainable Future: Advancing Packaging Technology
VidePak is actively investing in technologies and processes to further reduce environmental impact. From developing biodegradable polypropylene alternatives to setting up systematic recycling hubs, VidePak is paving the way for greener packaging solutions.
Future Plans:
- Biodegradable Materials: Researching innovative materials to meet rising sustainability demands.
- Recycling Systems: Establishing centralized hubs for recovering and reusing polypropylene products.
- Expanded Solar Capacity: Enhancing renewable energy reliance for all operations.
Learn more about VidePak’s commitment to eco-friendly solutions.
FAQs About Block Bottom PP Bags
Q: What makes Block Bottom PP bags suitable for heavy loads?
These bags are made with high-tensile-strength polypropylene, reinforced seams, and advanced lamination techniques, ensuring they can handle even the heaviest materials without damage.
Q: Can these bags be reused or recycled?
Yes, Block Bottom PP bags are designed for reuse and are 100% recyclable, supporting sustainability initiatives.
Q: Are there options for moisture-sensitive products?
Absolutely. Bags can be laminated or fitted with inner liners to protect against moisture and other environmental factors.
Q: How does VidePak ensure the quality of these bags?
VidePak employs stringent quality control at every production stage, from material selection to final inspection, adhering to international standards and ESG guidelines.
Conclusion
Block Bottom PP bags are an innovative solution for modern packaging challenges. Their superior design, exceptional durability, and customization options make them invaluable across industries. VidePak’s commitment to sustainability and quality further enhances the value of these bags, ensuring they meet the highest standards for performance and environmental responsibility.
As the packaging industry evolves, Block Bottom PP bags will remain a cornerstone of efficient, sustainable, and versatile packaging solutions.