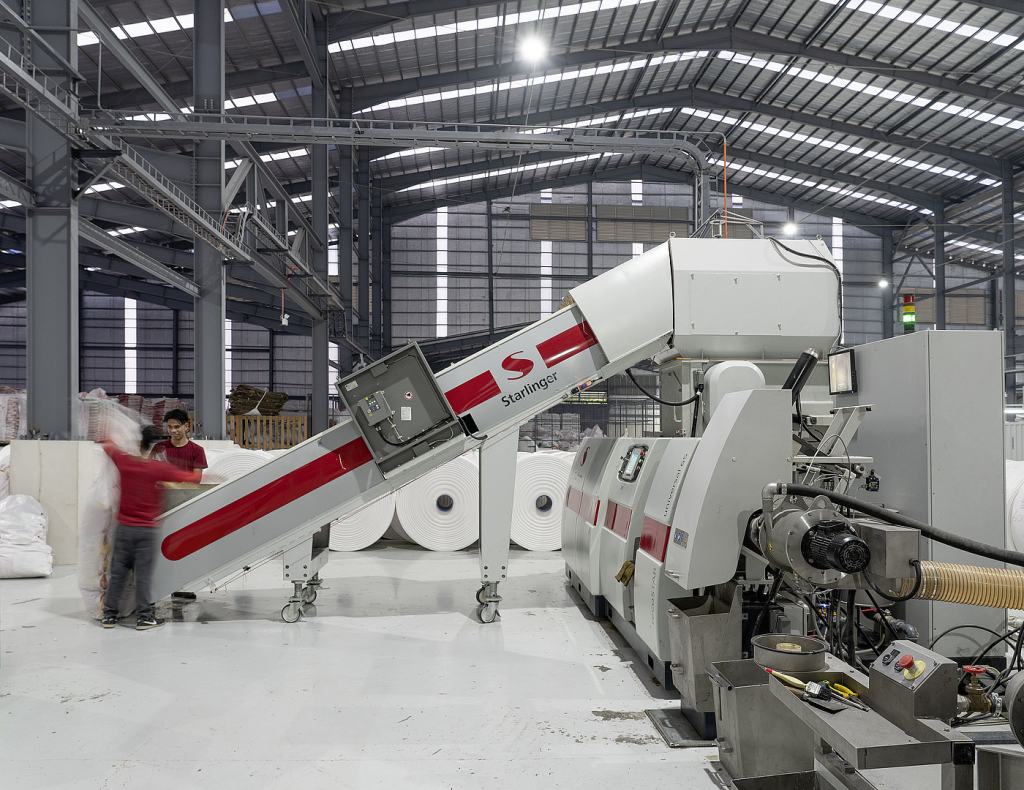
- 1. Technical Specifications: Defining Performance Boundaries
- 2. Anti-Static Technology: Safeguarding Sensitive Materials
- 3. Load-Bearing Capacity: Engineering for Safety
- 4. Innovation in Chinese Manufacturing: Beyond Cost Efficiency
- FAQs: Addressing Critical Concerns
- 5. The Future: Smart Packaging and Global Expansion
- Conclusion: Redefining Industrial Packaging
“What makes block bottom valve bags indispensable in today’s industrial supply chains?”
Ray, CEO of VidePak, answers without hesitation: “Precision engineering, anti-static safeguards, and relentless innovation. At VidePak, every bag is a testament to China’s manufacturing evolution.”
This philosophy has driven VidePak—a global leader with $80M annual revenue and 526 employees—to redefine block bottom valve bags as a cornerstone of modern logistics. Founded in 2008, the company leverages 30+ years of expertise, Austrian Starlinger machinery, and a commitment to ESG principles to deliver solutions that meet the rigorous demands of industries ranging from chemicals to food. This report explores the technical specifications, anti-static mechanisms, and load-bearing capacities of these bags, while highlighting how VidePak’s innovations align with China’s manufacturing renaissance.
1. Technical Specifications: Defining Performance Boundaries
Block bottom valve bags are engineered for stability and efficiency, with parameters tailored to diverse applications:
A. Thickness and Grammage Ranges
- Fabric Thickness: 0.08–0.12 mm (±0.02 mm tolerance), ensuring durability without sacrificing flexibility.
- Grammage: 80–120 g/m², optimized for load capacities up to 50 kg.
- Dimensions: Customizable from 40 cm × 60 cm to 100 cm × 120 cm, accommodating everything from powdered chemicals to bulk grains.
Parameter | VidePak Standard | Industry Average |
---|---|---|
Thickness Tolerance | ±0.02 mm | ±0.05 mm |
Valve Alignment | ±1 mm | ±3 mm |
Seam Strength | 80–100 N/cm | 60–80 N/cm |
Case Study: A chemical client required 100 cm × 120 cm bags for 50 kg polymer pellets. VidePak’s 0.12 mm thick bags reduced transit damage by 30% compared to competitors’ 0.10 mm variants.
2. Anti-Static Technology: Safeguarding Sensitive Materials
Static electricity poses risks in industries handling flammable powders (e.g., flour, pharmaceuticals). VidePak’s anti-static bags dissipate charges through:
A. Conductive Additives
- Carbon-Black Infusion: PP tapes blended with 2–4% carbon black achieve surface resistivity <10¹² Ω/sq (per ASTM D257).
- Metallic Threads: Interwoven stainless steel fibers create a Faraday cage effect, redirecting charges harmlessly.
B. Testing Protocols
- Charge Decay Test: <2.0 seconds (EN 61340-4-1), ensuring rapid dissipation.
- Surface Resistivity: <10¹¹ Ω/sq validated via 4-point probe method.
Example: A 2023 audit of VidePak’s anti-static bags for a lithium battery manufacturer showed zero static-related incidents across 10,000 units.
3. Load-Bearing Capacity: Engineering for Safety
Block bottom valve bags are designed to withstand dynamic stresses during filling, transport, and stacking:
- Safe Working Load (SWL): 25–50 kg, with a 5:1 safety factor (e.g., 250 kg burst limit for a 50 kg bag).
- Stacking Strength: Up to 8 layers (4 meters) without deformation, validated via 72-hour compression tests (ISO 2233).
Key Determinants of Strength:
- Weave Density: 12×12 strands/inch (vs. industry standard 10×10).
- UV Stabilization: HALS (hindered amine light stabilizers) additives extend tensile strength retention to 85% after 500 UV hours (ASTM D4329).
4. Innovation in Chinese Manufacturing: Beyond Cost Efficiency
China’s packaging sector, once synonymous with low-cost mass production, now leads in technological innovation. VidePak exemplifies this shift through:
A. Automation and Precision
- Starlinger’s Circular Looms: 200+ picks per minute (PPM) with ±2% weave density variance.
- AI-Driven Defect Detection: Reduces defect rates to 0.3% (industry average: 1.5%).
B. Sustainability Initiatives
- Recyclable PP Blends: 30% post-industrial recycled content without compromising tensile strength (>30 MPa).
- Energy Recovery: 85% of extrusion line heat reused, cutting carbon emissions by 15%.
Case Study: VidePak’s 2024 partnership with a European food brand reduced packaging waste by 40% via lightweight, high-strength valve bags.
FAQs: Addressing Critical Concerns
Q1: How do block bottom bags prevent “炸包” (bursting) during pneumatic filling?
A: VidePak’s 5:1 safety factor and ultrasonic seams (80–100 N/cm) ensure valve integrity under 0.5 bar pressure.
Q2: Are anti-static bags suitable for food-grade applications?
A: Yes. VidePak’s food-grade anti-static bags use FDA-compliant carbon-black blends.
Q3: What certifications validate load-bearing claims?
A: ISO 9001, ISO 22000, and BRCGS, with third-party testing by SGS.
5. The Future: Smart Packaging and Global Expansion
The valve bag market is projected to grow at 5.8% CAGR through 2030. VidePak’s roadmap includes:
- NFC Integration: Track shipments in real-time via embedded chips (2025 pilot).
- Regional Hubs: Expanding in Southeast Asia to cut logistics costs by 25%.
Conclusion: Redefining Industrial Packaging
Block bottom valve bags are no longer mere containers—they are engineered solutions bridging safety, efficiency, and sustainability. VidePak’s fusion of Starlinger precision, anti-static innovation, and ESG-aligned practices positions it as a leader in China’s manufacturing revolution. As Ray asserts: “Innovation isn’t optional; it’s the price of entry in today’s global market.”
For industries seeking certified, high-performance solutions, VidePak remains the benchmark.
Note: All data reflects 2025 industry benchmarks and VidePak’s internal testing protocols.