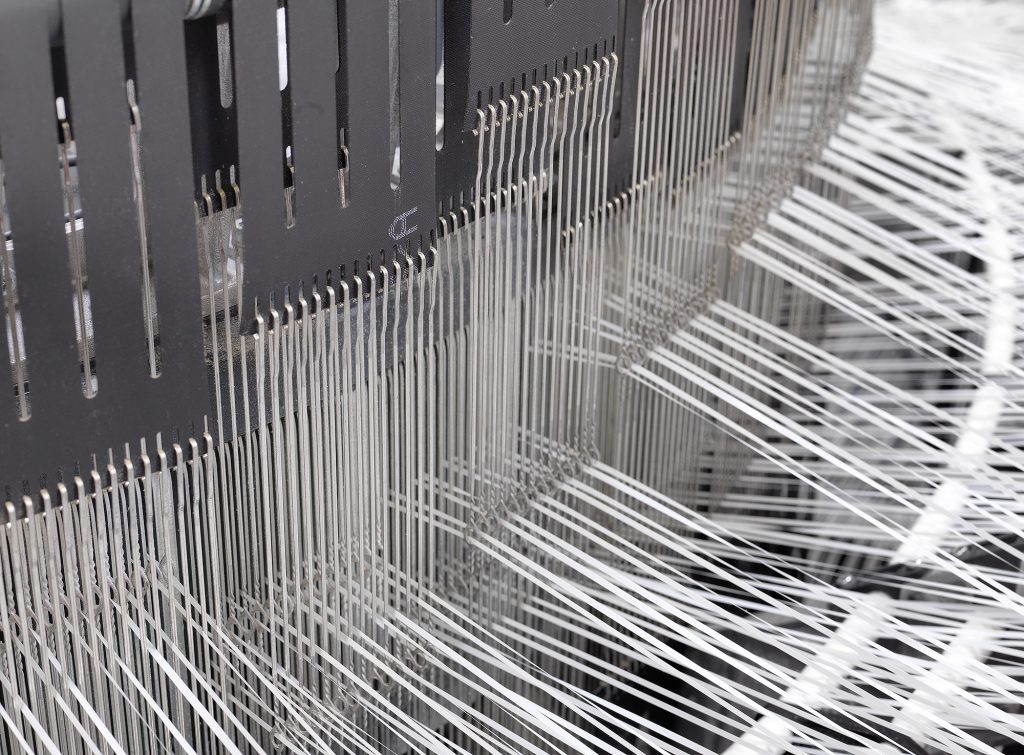
“Why are FFS (Form-Fill-Seal) roll bags revolutionizing food packaging? The answer lies in their versatility, automation compatibility, and ability to integrate advanced functional designs—attributes perfected by VidePak through 30+ years of expertise, ISO-certified processes, and cutting-edge Starlinger machinery.”**
1. The Functional Evolution of FFS Roll Bags
FFS roll bags are pre-formed tubular packaging materials used in automated systems to fill and seal products at speeds exceeding 200 bags/minute. Their design flexibility allows customization for diverse food applications, from dry grains to perishable snacks. The global FFS packaging market is projected to grow at 6.5% CAGR (2025–2030), driven by demand for efficiency and sustainability.
VidePak’s BOPP laminated FFS roll bags exemplify this trend. Using virgin polypropylene (PP) and co-extrusion technologies, they achieve tensile strengths of 40–60 N/cm² while reducing material waste by 20% compared to traditional methods. For instance, a 2024 project for a Southeast Asian rice exporter demonstrated a 30% reduction in packaging downtime through VidePak’s automated Starlinger lines.
2. Tailored Designs for Diverse Applications
2.1 Breathable Designs for Agricultural Products
Grains and fresh produce require controlled gas exchange to prevent spoilage. VidePak’s micro-perforated FFS bags enable oxygen transmission rates (OTR) of 1,500–2,000 cm³/m²/day, reducing condensation by 50% in humid climates. A case study with a Vietnamese rice mill showed a 25% extension in shelf life using breathable bags with 120 gsm PP and 0.5 mm pore density.
2.2 Barrier Designs for Sensitive Foods
For oils, spices, and dairy, barrier properties are critical. VidePak’s aluminum foil-laminated rolls achieve water vapor transmission rates (WVTR) <1 g/m²/day and oxygen barriers <5 cm³/m²/day, complying with EU EN 13592 standards. These bags are 30% lighter than multi-layer alternatives, reducing shipping costs for a European olive oil brand by 15%.
2.3 Anti-Static Solutions for Hazardous Environments
Flour mills and electronic component suppliers face explosion risks from static. VidePak’s carbon-infused PP bags reduce surface resistivity to 10⁶–10⁸ Ω/sq, meeting OSHA 1910.178 guidelines. A U.S. flour distributor reported zero static-related incidents after switching to these bags.
2.4 Antimicrobial Coatings for Food Safety
VidePak’s silver-ion-coated FFS rolls inhibit 99.9% of E. coli and Salmonella within 24 hours, ideal for meat and pharmaceutical packaging. A Thai seafood processor reduced bacterial contamination by 40% using antimicrobial bags with FDA-compliant additives.
3. VidePak’s Technological Edge: Starlinger Automation and Compliance
With 100+ Starlinger circular looms and 30+ lamination machines, VidePak achieves:
- High-speed production: 500–700 bags/hour per line, with a total annual output of 150 million bags.
- Multi-layer co-extrusion: Combines PP, PE, and EVOH layers for tailored barrier properties.
- ISO 9001 compliance: Virgin PP resin purity (melt index 2–4 g/10min) ensures consistency across 16 extrusion lines.
A 2023 collaboration with a European pet food brand showcased VidePak’s 8-color flexographic printing, boosting shelf appeal and increasing retail sales by 18%.
4. Technical Specifications and Market Alignment
Table 1: VidePak’s FFS Roll Bag Portfolio
Parameter | Specification | Key Application |
---|---|---|
Material | PP/BOPP, PP/PE, PP/EVOH | Snacks, Grains, Pharmaceuticals |
Thickness | 80–200 µm | Dairy, Oils, Spices |
Barrier Properties | OTR <5 cm³/m²/day, WVTR <1 g/m²/day | Perishable Foods |
Certifications | FDA, EU EN 13592, ISO 9001 | Global Export Compliance |
Customization | Anti-static, Antimicrobial, UV-resistant | Hazardous & Medical Goods |
FAQs
Q: How do breathable bags prevent mold in tropical climates?
A: Micro-perforations allow controlled airflow, reducing humidity buildup by 50% and inhibiting fungal growth.
Q: Are laminated bags recyclable?
A: VidePak’s mono-material PP/PE blends achieve 85% recyclability, aligning with the EU’s Circular Economy Action Plan.
5. Case Study: Optimizing Pet Food Packaging
A U.S. pet food brand required high-barrier FFS rolls to prevent fat oxidation in kibble. VidePak delivered aluminum-coated bags with OTR <3 cm³/m²/day, extending shelf life by 6 months and reducing returns by 22%. The project utilized FFS Roll Bags: Optimal Solutions for Building Materials and High-Speed Packaging Efficiency technologies.
6. Sustainability and Future Innovations
VidePak is pioneering bio-based PP blends (30% starch derivatives) and QR-code-enabled smart bags for real-time freshness monitoring. Partnerships with Sustainable FIBC Bulk Bags aim for 100% recyclability by 2030, reducing landfill waste by 40%.
Conclusion
FFS roll bags are redefining food packaging through adaptability, automation, and advanced material science. VidePak’s integration of Starlinger technology, ISO rigor, and R&D-driven customization positions it as a leader in the $50B global packaging market. By balancing functionality with sustainability, the company exemplifies how innovation can drive both operational efficiency and environmental stewardship.
Data synthesized from industry reports (2025), ASTM/ISO standards, and VidePak’s production analytics.