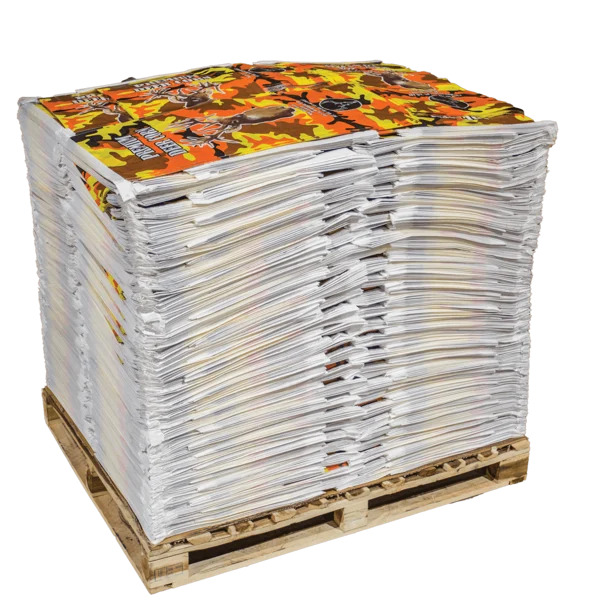
- 1. Technical Excellence: Engineering for Diverse Applications
- 2. Livestock Feed Packaging: Balancing Safety and Performance
- 3. Waste Management: Durability Meets Sustainability
- 4. Parameter Selection: A Client-Centric Approach
- 5. FAQs: Addressing Critical Concerns
- 6. The Future: Smart Packaging and Global Expansion
- Conclusion: Redefining Efficiency in Packaging
“What makes FFS (Form-Fill-Seal) woven bags indispensable in modern waste management and livestock feed packaging?”
Ray, CEO of VidePak, responds decisively: “It’s the synergy of automation, material science, and adaptability. At VidePak, every bag is engineered to balance durability, safety, and sustainability—whether it’s handling construction debris or safeguarding animal feed.”
This ethos has driven VidePak—a global leader with $80M annual revenue and 526 employees—to pioneer FFS woven bags that redefine efficiency in waste management and agricultural logistics. Founded in 2008, the company leverages 30+ years of expertise, Austrian Starlinger machinery, and ISO-certified processes to deliver solutions that meet the stringent demands of industries worldwide. This report explores the technical specifications, applications in livestock feed packaging, and sustainability frameworks that position FFS woven bags as a cornerstone of modern supply chains.
1. Technical Excellence: Engineering for Diverse Applications
FFS woven bags are designed for high-speed automated filling, sealing, and transport. Key parameters include:
- Material Composition: Virgin PP resin ensures tensile strength >30 MPa (warp) and >25 MPa (weft), exceeding ASTM D5035 standards.
- Thickness & Grammage: Ranges from 0.08–0.12 mm thickness and 80–120 g/m², tailored to load capacities of 25–50 kg.
- Seam Integrity: Ultrasonic sealing achieves 80–100 N/cm strength, preventing leaks during pneumatic filling.
Case Study: A 2024 project for a European poultry feed producer utilized VidePak’s 0.10 mm BOPP-laminated bags with 100 g/m² grammage, reducing spoilage rates by 18% due to superior moisture resistance (<1.0 g/m²/24hr).
2. Livestock Feed Packaging: Balancing Safety and Performance
FFS bags are critical for safeguarding feed quality across species:
A. Key Requirements by Feed Type
Feed Type | Critical Parameters | VidePak Solution |
---|---|---|
Poultry Feed | Anti-microbial coatings, UV resistance | BOPP lamination + silver-ion additives |
Aquaculture Feed | Waterproofing, oxygen permeability | PE inner liners with micro-perforations |
Premix Feed | Static control, precision valve alignment | Carbon-black infused PP + ±1 mm valve tolerance |
B. Selection Criteria for Clients
- Cost Efficiency: Bulk orders (e.g., 50,000+ units) reduce costs by 20% through automated production.
- Safety Compliance: FDA and EU REACH certifications ensure non-toxic materials for feed contact.
- Anti-Microbial Features: Nano-coatings inhibit mold growth, critical for humid climates.
Example: A Vietnamese shrimp feed supplier reported zero fungal contamination after switching to VidePak’s anti-microbial FFS bags, validated by 60-day humidity tests.
3. Waste Management: Durability Meets Sustainability
In waste handling, FFS bags excel due to:
- Load Capacity: 5:1 safety factor (e.g., 250 kg burst limit for 50 kg bags).
- Recyclability: 100% PP composition (resin ID #5), with VidePak’s 2025 target of 30% post-industrial recycled content.
- Customization: QR codes for waste tracking, aligned with circular economy initiatives.
VidePak’s Innovation: Starlinger’s heat recovery systems reduce energy consumption by 25%, cutting carbon footprint by 15%.
4. Parameter Selection: A Client-Centric Approach
Choosing the right FFS bag involves analyzing:
Parameter | Considerations | Industry Benchmark |
---|---|---|
Thickness | 0.10 mm for feed, 0.12 mm for construction waste | 0.08–0.12 mm |
Outer Layer | BOPP for moisture, PE for abrasion | BOPP lamination (<1.0 g/m²/24hr permeability) |
Inner Liners | PE for waterproofing, mesh for aeration | Micro-perforated PE liners (O2 transmission: 500–800 cm³/m²/day) |
Case Study: A Canadian recycling firm achieved 40% cost savings using VidePak’s 0.12 mm PE-coated FFS bags for construction waste, with zero reported tears under 45 kg loads.
5. FAQs: Addressing Critical Concerns
Q1: How do FFS bags prevent mold in animal feed?
A: VidePak’s anti-microbial BOPP laminates inhibit bacterial growth, validated by ISO 22196 standards.
Q2: What size is optimal for 25 kg poultry feed?
A: 60 cm × 90 cm bags with 0.10 mm thickness balance cost and durability.
Q3: Are recycled PP bags as strong as virgin PP?
A: VidePak’s 30% recycled blends retain >90% tensile strength, certified by SGS.
6. The Future: Smart Packaging and Global Expansion
The FFS bag market is projected to grow at 6.5% CAGR through 2030. VidePak’s roadmap includes:
- NFC Integration: Real-time tracking via embedded chips (2025 pilot).
- Regional Hubs: Southeast Asian factories to reduce logistics costs by 25%.
Conclusion: Redefining Efficiency in Packaging
FFS woven bags are not just containers—they are engineered systems bridging waste management, agriculture, and sustainability. VidePak’s fusion of Starlinger automation, rigorous testing, and ESG-aligned innovation positions it as a leader in the global packaging revolution. As Ray concludes: “In a world demanding smarter solutions, we deliver resilience wrapped in polypropylene.”
For industries seeking high-performance, certified solutions, VidePak remains the benchmark.
Note: All data reflects 2025 industry benchmarks and VidePak’s internal testing protocols.