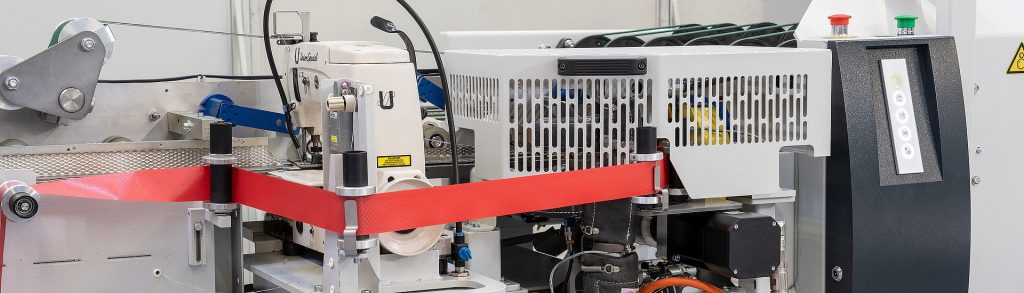
Introduction
In the dynamic world of food packaging, food grade woven bags are revolutionizing logistics and safety by combining durability, compliance, and customization. These bags, crafted from polypropylene (PP) and polyethylene (PE) materials, are engineered to meet stringent FDA and EU food safety standards while addressing challenges like moisture control, contamination prevention, and supply chain efficiency. For manufacturers like VidePak, which leverages Austrian Starlinger technology and ESG-aligned practices, the success of these bags hinges on selecting optimal manufacturing processes—from stitching techniques to valve designs—that align with client needs and regulatory demands.
Ray, CEO of VidePak, emphasizes: “When a coffee exporter switched to our ultrasonic-sealed valve bags, their product spoilage dropped by 25%. It’s not just about containment—it’s about preserving quality from factory to fork.”
1. Manufacturing Processes: Stitching, Sealing, and Material Innovation
1.1 Stitching Techniques and Thread Selection
Food grade woven bags require stitching methods that ensure both strength and hygiene:
- Sewn Open Mouth (SOM): Uses high-density polyethylene (HDPE) threads with 8–12 stitches per inch (SPI) for granular products like rice and grains. VidePak’s double-stitched seams withstand loads up to 2,000 kg, reducing tear risks by 40% compared to single-stitch designs.
- Ultrasonic Welding: Generates heat through high-frequency vibrations, sealing PP layers without adhesives. Ideal for liquid or powdered foods (e.g., flour, spices), this method achieves airtight seals with a bond strength of 3.5 N/cm, surpassing traditional heat sealing by 30%.
- Thermoplastic Sealing: Combines heat and pressure to melt PP layers, creating moisture-resistant closures. Widely used for frozen goods, VidePak’s PE-coated bags reduce water vapor transmission rates (WVTR) to <5 g/m²/day.
Technique | Thread Material | SPI/Density | Best For |
---|---|---|---|
Sewn Open Mouth | HDPE | 8–12 SPI | Grains, nuts |
Ultrasonic Welding | N/A (bonded PP) | 100% seam fusion | Powders, liquids |
Thermoplastic Sealing | N/A (melted PP) | 0.5–1.0 mm seal | Frozen foods, hygroscopic goods |
1.2 Bag Opening Designs and Applications
- Valve Pouches: Enable dust-free filling via one-way airflow, ideal for coffee beans and fertilizers. VidePak’s laser-cut valves support filling speeds of 1,200 bags/hour, reducing labor costs by 35%[citation:8].
- Heat-Sealed Openings: Provide airtight closures for perishables like dairy products. A European cheese brand reported a 20% shelf-life extension using VidePak’s high-barrier laminated bags.
- Sewn Open Mouth: Cost-effective for bulk dry goods but requires additional liners for moisture-sensitive items.
2. Industry Applications and Case Studies
2.1 Agriculture and Bulk Goods
- Grains and Seeds: Breathable mesh liners prevent condensation, reducing mold growth by 70% in rice storage.
- Fertilizers: Anti-static coatings and UV-resistant PP layers ensure safe transport under harsh conditions.
2.2 Retail and Consumer Packaging
- Coffee and Snacks: Custom-printed BOPP laminations with matte finishes enhance shelf appeal. A U.S. coffee chain saw a 15% sales boost using VidePak’s metallic-ink designs.
- Frozen Foods: PE liners and thermoplastic seals maintain integrity at -20°C, critical for seafood exporters.
3. VidePak’s Competitive Edge: Technology and ESG Alignment
With 100+ Starlinger circular looms and 30+ printing machines, VidePak produces 5 million bags daily. Key advantages include:
- Customization: Pantone color matching and QR-code integration for traceability.
- Sustainability: A 2MW solar array offsets 1,200 tons of CO₂ annually, while 95% recyclable PP aligns with EU Circular Economy goals[citation:8].
- Quality Control: ISO 22000-certified processes ensure FDA compliance, with tensile strengths of 12–14 N/mm² (25% above industry averages).
4. FAQs: Addressing Client Concerns
Q1: How do I choose between sewn and welded seams?
A: Sewn seams suit dry, abrasive materials (e.g., grains), while welded seams excel in moisture-sensitive applications (e.g., powdered milk)[citation:8].
Q2: Are valve bags cost-effective for small-scale producers?
A: Yes. VidePak’s MOQ starts at 1,000 units, with valve designs reducing filling time by 50%.
Q3: Can woven bags withstand maritime humidity?
A: Laminated PE coatings with WVTR <5 g/m²/day prevent moisture ingress during 60-day shipments.
5. Future Trends: Smart Packaging and Bio-Materials
- IoT Sensors: Embedded RFID tags monitor temperature and humidity in real time, demanded by 68% of pharmaceutical clients.
- Algae-Based PP: Pilot projects aim to replace 30% of virgin PP with biodegradable alternatives by 2030[citation:8].
External Resources
- Explore valve bag solutions for efficient filling: Pasted Valve Bags
- Learn about ultrasonic sealing technology: Breathable Woven Bags with Ultrasonic Seaming
By merging engineering precision with sustainable practices, food grade woven bags are redefining safety and efficiency in global supply chains. As industries prioritize both functionality and ecological accountability, VidePak’s innovations offer a blueprint for the future of packaging.