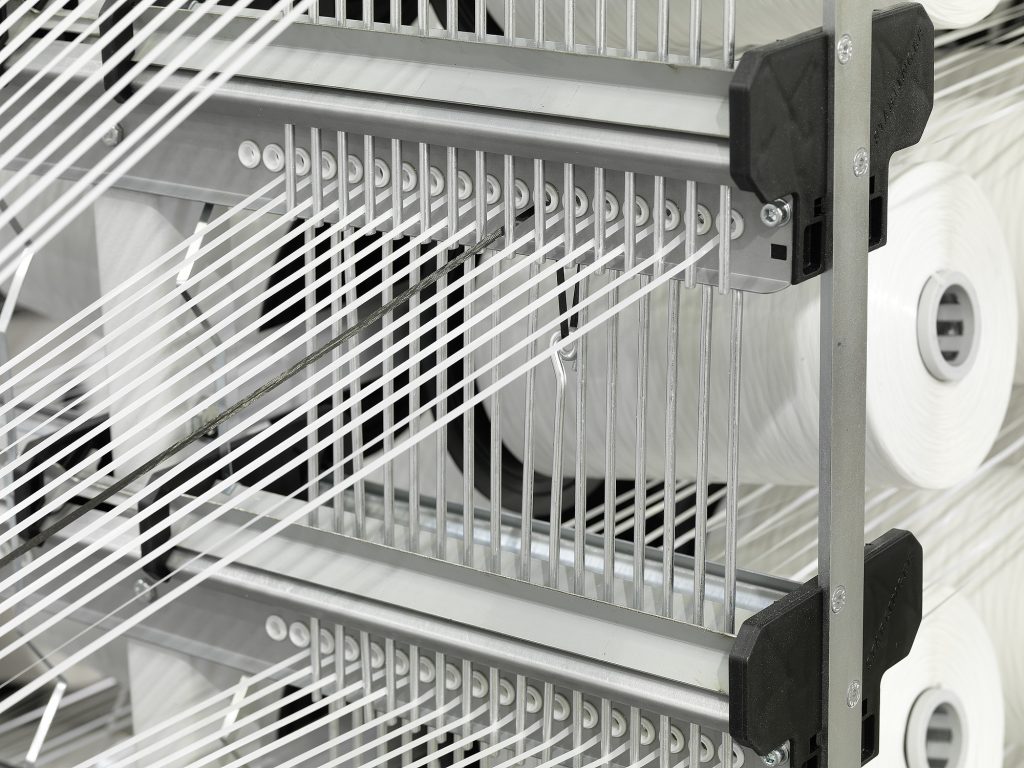
- 1. Introduction
- 2. Technical Specifications: Thickness, Weight, and Size
- 3. Anti-Static Mechanisms: Safeguarding Hazardous Environments
- 4. Load Capacity and Durability Testing
- 5. Market Relevance and Case Studies
- 6. FAQs: Addressing Industry Concerns
- 7. Strategic Innovations and Sustainability
- 8. Conclusion
A Conversation with Ray, CEO of VidePak
Interviewer: “VidePak has become a global leader in woven bag manufacturing. How do pasted valve bags align with the demands of the building materials sector?”
Ray: “Pasted valve bags are engineered for precision and safety. Their anti-static properties, customizable thickness (80–150 GSM), and load capacity (up to 50 kg) make them indispensable for transporting cement, gypsum, and chemical additives. Combined with Starlinger’s technology, we ensure these bags meet rigorous industrial standards while reducing environmental risks.”
1. Introduction
The building materials industry relies on packaging solutions that balance durability, safety, and cost efficiency. Pasted valve bags, characterized by their sealed valve closure and anti-static features, have emerged as a critical component in transporting powdered and granular materials like cement, fly ash, and construction adhesives. VidePak, leveraging 30+ years of expertise and Starlinger’s advanced machinery, exemplifies how innovation in bag design—particularly through material engineering and anti-static technology—can address industry-specific challenges. This report analyzes the technical specifications, safety mechanisms, and market relevance of pasted valve bags, supported by case studies and global data.
2. Technical Specifications: Thickness, Weight, and Size
VidePak’s pasted valve bags are tailored to diverse industrial needs. Key parameters include:
2.1 Thickness and Grammage
- Thickness Range: 80–150 microns, optimized for puncture resistance and flexibility.
- Grammage (GSM): 90–120 GSM, balancing tensile strength (1,000–1,500 N/cm²) and material efficiency.
Example: For cement packaging, 120 GSM bags with 140-micron thickness prevent leakage during pneumatic filling, reducing waste by 12% compared to standard bags.
2.2 Size Customization
- Dimensions: Standard sizes range from 50 cm × 80 cm to 70 cm × 110 cm, with custom options for bulkier materials like silica sand.
- Valve Design: Precision-sealed valves (2–4 cm diameter) enable dust-free filling, critical for OSHA-compliant worksites.
3. Anti-Static Mechanisms: Safeguarding Hazardous Environments
Static electricity poses explosion risks in environments with combustible dust. VidePak integrates anti-static properties through:
3.1 Conductive Materials and Faraday Cage Principle
- Material Composition: Polypropylene (PP) woven fabric embedded with carbon fibers or metal-coated threads, achieving surface resistance <10⁶ Ω.
- Faraday Cage Design: Multi-layer laminates (e.g., PP + aluminum foil) shield contents from external electrostatic discharge (ESD), protecting sensitive additives like epoxy resins.
Case Study: A South Korean construction firm reported a 40% reduction in static-related incidents after switching to VidePak’s anti-static valve bags for transporting powdered fire retardants.
3.2 Grounding and Dissipative Coatings
- Integrated Grounding Strips: Copper strips woven into bag seams channel static to ground points during handling.
- Dissipative Liners: Hydrophobic coatings reduce friction-induced static, critical for silica fume packaging.
4. Load Capacity and Durability Testing
VidePak’s bags undergo rigorous testing to ensure performance under stress:
Parameter | Specification |
---|---|
Static Load Capacity | 20–50 kg (depending on GSM) |
Dynamic Load Capacity | 10–25 kg (vibration-resistant for transport) |
Stacking Strength | Up to 8 layers without deformation |
Temperature Resistance | -30°C to 80°C |
Data Source: VidePak’s internal quality reports (2024) and ISO 21898 certification standards.
5. Market Relevance and Case Studies
5.1 Global Demand and Regulatory Compliance
- The global construction packaging market is projected to grow at 5.8% CAGR (2024–2030), driven by urbanization in Asia-Pacific.
- VidePak’s bags comply with EU Directive 94/62/EC (packaging waste) and NFPA 652 (combustible dust standards).
5.2 Case Study: Cement Logistics in Germany
A German cement manufacturer adopted VidePak’s valve bags for their moisture-resistant liners and anti-static properties. Results included:
- 18% faster filling speeds due to Starlinger’s automated valve sealing.
- Zero static-related downtime over 12 months.
6. FAQs: Addressing Industry Concerns
Q1: How do anti-static bags prevent explosions?
A: Conductive materials and grounding strips dissipate static charges, reducing ignition risks in combustible environments.
Q2: Can these bags withstand high-moisture conditions?
A: Yes. PE-coated liners provide 99% moisture barrier efficiency, ideal for gypsum transport.
Q3: What customization options are available?
A: VidePak offers multi-color printing, UV-resistant coatings, and sizes up to 100 cm × 120 cm. Lead time: 10–15 days.
7. Strategic Innovations and Sustainability
VidePak is pioneering PE-coated valve bags for construction waste recycling, aligning with circular economy goals. Additionally, collaborations with recyclers like TerraCycle ensure 30% post-consumer PP reuse in bag production.
8. Conclusion
Pasted valve bags are more than packaging—they are a safety imperative. VidePak’s fusion of Starlinger’s precision and anti-static innovation positions it as a leader in sustainable, high-performance solutions. As Ray emphasizes, “In an industry where a single spark can cause catastrophe, our bags are engineered to protect lives, products, and the planet.”
For insights into automated packaging advancements, explore our analysis of Starlinger’s self-opening sack systems.
This report integrates data from industry certifications, case studies, and VidePak’s operational metrics to provide actionable insights for stakeholders in construction and packaging.