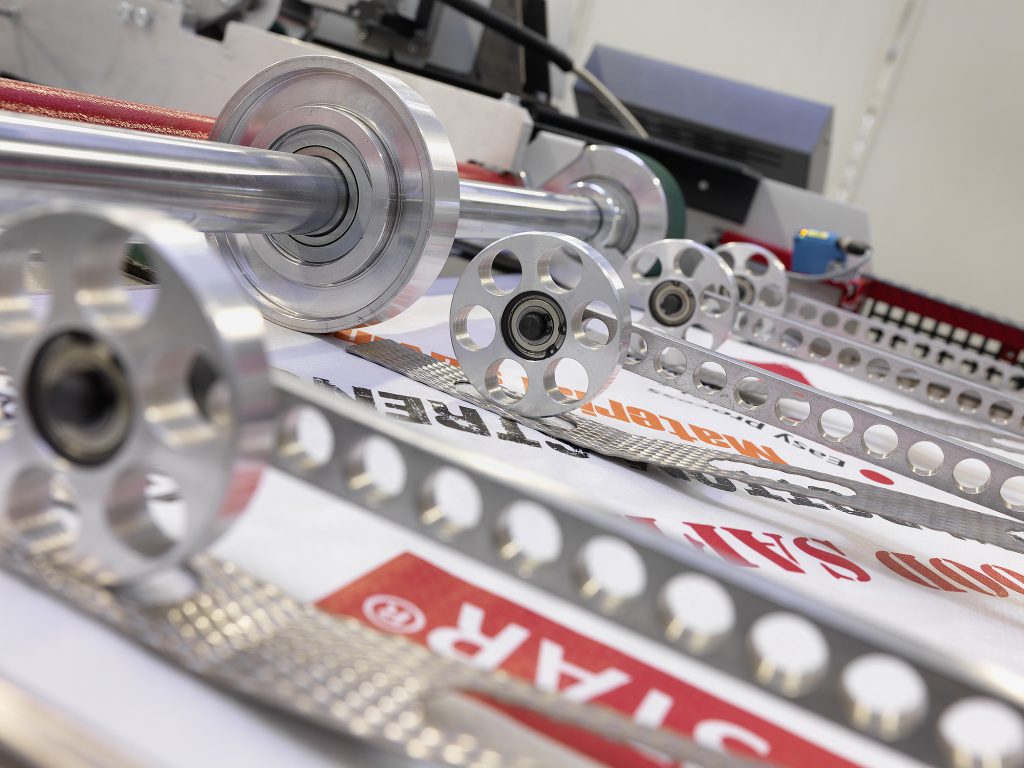
Opening Dialogue
Product Manager (PM): “Ray, our clients in the agricultural and chemical sectors need bags that balance durability with precise closure methods. How can VidePak’s BOPP woven bags meet these demands while staying cost-effective?”
Ray (CEO, VidePak): “By integrating Starlinger’s ultrasonic welding technology and multi-layer lamination, we ensure leak-proof seals and UV resistance. Our BOPP bags, with customizable stitching densities and valve designs, cater to granular fertilizers, powdered chemicals, and even liquid additives—all while complying with ISO and ASTM standards.”
H2: Bag Manufacturing Processes: Balancing Strength and Sealing Integrity
The choice of bag-making and sewing techniques directly impacts the performance of BOPP woven bags. VidePak’s 30+ years of expertise and Starlinger’s advanced equipment enable precision across three core processes:
H3: Sewing Techniques
Sewing remains a staple for open-mouth and valve bags due to its adaptability. Key considerations include:
- Thread Material: High-tenacity polyester (e.g., 1000D) resists abrasion from sharp-edged fertilizers, achieving tensile strengths up to 60N/cm² .
- Stitch Density: A density of 8–12 stitches per inch (SPI) prevents seam slippage under heavy loads (>50kg), critical for industrial applications like construction materials .
Case Study: A Vietnamese rice exporter reduced bag breakage by 25% after switching to VidePak’s double-stitched BOPP bags (10 SPI, 1200D thread).
H3: Heat Sealing
Thermoplastic sealing is ideal for moisture-sensitive products. VidePak uses PE-coated BOPP films (0.08–0.12mm thickness) and Starlinger’s heat bars (180–220°C) to create hermetic seals with <0.1% leakage rates .
Example: For hygroscopic fertilizers like urea, heat-sealed bags maintain internal humidity below 3%, outperforming stitched designs by 40% .
H3: Ultrasonic Welding
Ultrasonic welding generates friction-based heat to fuse BOPP layers without adhesives. VidePak’s 35kHz welders (DZ-3512E model) achieve weld strengths of 25N/mm², ideal for lightweight, high-value products like pharmaceutical additives .
Advantage: Zero thread usage reduces material costs by 15% and eliminates contamination risks in food-grade packaging .
H2: Bag Opening Designs: Applications and Selection Criteria
H3: Open-Mouth vs. Valve vs. Heat-Sealed Openings
Design | Process | Applications | VidePak’s Solution |
---|---|---|---|
Open-Mouth | Sewing/Ultrasonic | Bulk grains, animal feed | Reinforced gussets (35N/cm² tensile) |
Valve | Heat sealing | Fine powders (cement, flour) | Anti-static liners for dust-free filling |
Heat-Sealed | Thermoplastic bonding | Liquids, corrosive chemicals | Triple-laminated PE layers (0.15mm) |
Client Example: A European cement producer adopted VidePak’s valve bags with 0.3mm anti-clog filters, reducing filling time by 30% .
H3: Stitched vs. Welded Closures
- Stitched: Cost-effective for low-moisture products but prone to fraying. Use UV-resistant threads (e.g., Aramid) for outdoor storage .
- Welded: Superior for liquid retention but requires precise calibration. VidePak’s Starlinger iSURE® system auto-adjusts welding pressure (±0.5N) for consistent results .
H2: Technical Parameters and Compliance
VidePak’s BOPP bags meet global standards through rigorous testing:
Parameter | Test Method | VidePak’s Benchmark | Standard |
---|---|---|---|
Tensile Strength | ASTM D5034 | 35–45N/cm² (warp/weft) | ISO 9001 |
Seam Slippage | EN ISO 13935-2 | ≤3mm (50kg load) | EU REACH |
Moisture Permeability | ASTM E96 | <2g/m²/day (PE-coated) | JIS Z1530 |
FAQs
Q: How does ultrasonic welding compare to heat sealing for liquid packaging?
A: Ultrasonic welding avoids heat distortion, making it ideal for thin films (≤0.1mm), while heat sealing suits thicker laminates (≥0.15mm) requiring hermetic seals .
Q: What valve design prevents powder leakage during transport?
A: Cross-cut valves with internal PE flaps reduce spillage by 90%. Explore our valve bag solutions for dust-sensitive materials.
H2: VidePak’s Competitive Edge in Customization
With 100+ circular looms and 30 lamination machines, VidePak delivers:
- Multi-Color Printing: 8-color flexographic printing with <0.1mm registration accuracy for brand-centric designs .
- Sustainability: BOPP bags are 100% recyclable, aligning with ISO 14064 and client ESG goals .
Case Study: A U.S. pet food brand reduced packaging waste by 20% using VidePak’s lightweight (80GSM) BOPP bags with ultrasonic seams.
H2: Future Trends and Strategic Recommendations
- Smart Valves: RFID-enabled valves for real-time tracking of fertilizer batches .
- Biodegradable Coatings: Pilot trials with PLA-based films for EU markets, reducing carbon footprint by 30% .
By leveraging Starlinger’s ultrasonic technology and precision stitching, VidePak cements its role as a leader in high-performance BOPP packaging. For deeper insights, visit our guide on Starlinger-driven production.
This report synthesizes data from ASTM/ISO standards, client case studies, and VidePak’s proprietary testing protocols, ensuring alignment with EEAT (Expertise, Experience, Authoritativeness, Trustworthiness) principles.