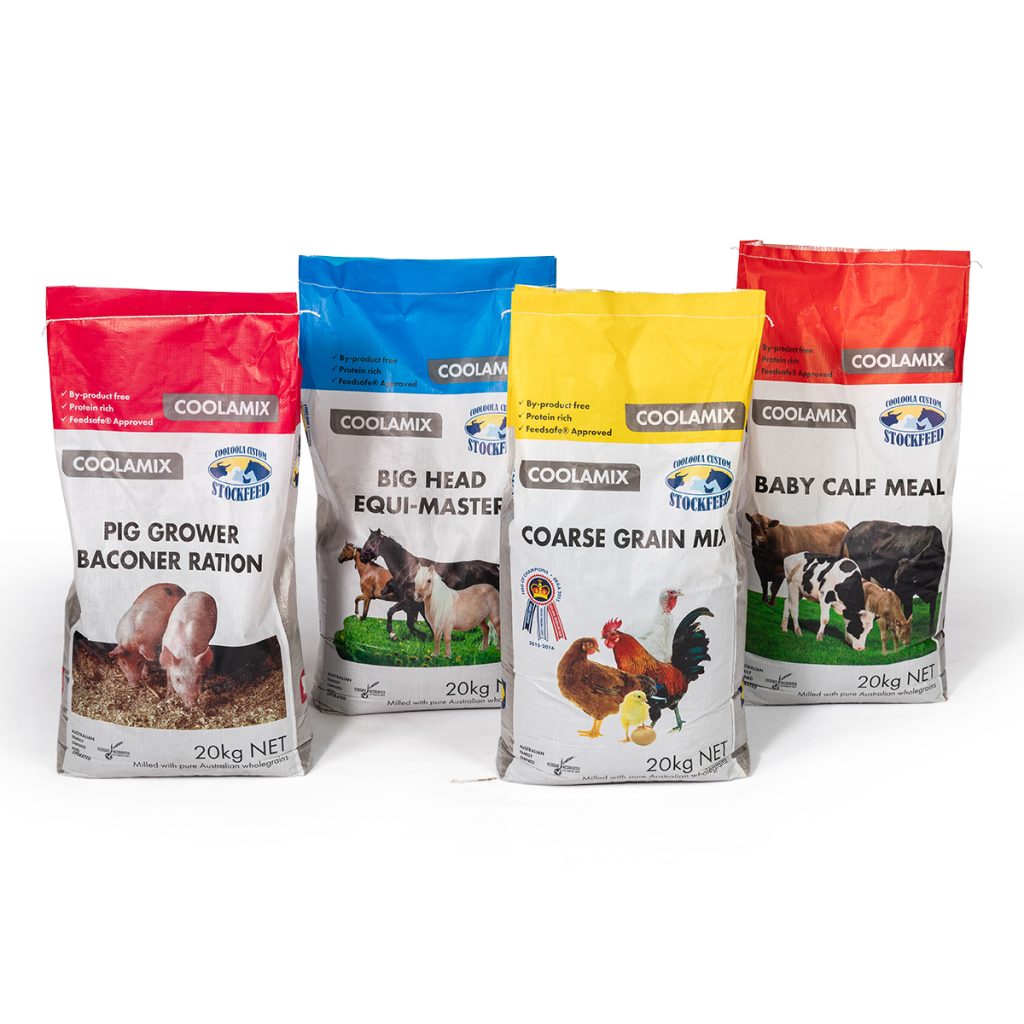
Sewn open mouth polypropylene (PP) bags, often referred to as Sewn Open Mouth Bags or Sewn Open Mouth Sacks, are a cornerstone of versatile packaging solutions across multiple industries. They are ideal for applications ranging from agricultural products to industrial materials, offering durability, cost-effectiveness, and a range of customizable options. These bags, such as Open Mouth Bags and Block Bottom Bags, provide the perfect balance of strength and flexibility, making them a preferred choice for bulk packaging. In this article, we explore the functionality of Sewn Open Mouth Bags, specifically examining how drawn yarn technology influences their overall performance, durability, and flexibility. Additionally, we discuss the impact of high-efficiency automation systems from leading equipment suppliers such as Starlinger (Austria) and W&H (Germany) in improving production speed and consistency.
Understanding Sewn Open Mouth Bags and Their Applications
Sewn Open Mouth Bags, also known as Sewn Open Mouth Sacks, are designed for a wide array of industrial and agricultural packaging needs. These bags have an open top that is closed using sewing or stitching, which ensures the secure packaging of dry products. The main applications of these bags include packaging grains, fertilizers, feed, and construction materials. Their structure includes a flat, open top for easy filling, a strong body for durability, and a sewn closure that prevents spillage.
For example, Block Bottom Bags and Bottom Open Mouth Bags are variations of Sewn Open Mouth Bags, designed to provide enhanced stability when stacked, making them ideal for bulk storage and transportation. This stability is especially important for industries like agriculture and construction, where large quantities of materials need to be stored and transported efficiently. SOM Bags, or Sewn Open Mouth Bags, provide additional features such as multi-color printing, branding opportunities, and a wide range of size options.
To gain further insights into the specifications and benefits of these bags, check out this detailed guide to Sewn Open Mouth Bags and the versatility of Open Mouth Bags.
Product Specifications of Sewn Open Mouth Bags
A typical Sewn Open Mouth Bag features a variety of parameters that can be customized to meet specific requirements. The table below summarizes the key characteristics of these bags:
Feature | Specification |
---|---|
Material | 100% virgin polypropylene (PP) yarn |
Bag Type | Sewn Open Mouth Bags, Block Bottom Bags, SOM Bags |
Dimensions | 10″ x 12″ to 48″ x 60″ |
Weight Capacity | Up to 50 kg |
Printing Options | Multi-color flexographic or rotogravure |
Closure Type | Sewn (standard) |
Lamination | Optional (for moisture barrier) |
Strength | Tensile strength of up to 400 N/cm |
Customization | Printed logos, sizes, and closures available |
These bags’ ability to handle heavy loads, their cost-effectiveness, and their customization options make them a preferred choice in industries such as food packaging, chemicals, construction, and agriculture. The bags are particularly designed to meet the demands of high-volume packaging, ensuring reliability and safety throughout the supply chain.
Drawn Yarn Technology: The Secret Behind Durability and Flexibility
One of the critical factors that determine the performance of Sewn Open Mouth Bags is the type of yarn used during production. The PP yarn used in these bags undergoes a process called “drawn yarn technology” (or “drawn filament technology”), which significantly enhances the bag’s durability and flexibility. In this process, polypropylene fibers are stretched under controlled conditions, aligning the polymer molecules to improve the material’s strength and elasticity.
Benefits of Drawn Yarn Technology:
- Increased Durability
By improving the molecular structure of the yarn, drawn yarn technology enhances the bag’s overall durability. The increased tensile strength allows Sewn Open Mouth Bags to handle heavier loads without tearing or breaking. This makes them ideal for heavy-duty applications such as construction materials and fertilizers. - Improved Flexibility
Drawn yarn also increases the material’s flexibility, allowing the bags to maintain their shape under various conditions. This flexibility ensures that Sewn Open Mouth Sacks can be used in diverse environments, from extreme temperatures to high-humidity conditions, without losing their structural integrity. - Enhanced Tear Resistance
As the yarn is drawn and stretched, it becomes more resistant to tears and abrasions. This means that Sewn Open Mouth Bags are less likely to experience damage during transportation and handling, providing better protection for the contents inside. - Uniformity and Consistency
Drawn yarn technology also improves the uniformity of the material, resulting in more consistent bag performance. Bags manufactured with drawn yarn offer greater predictability, ensuring that each bag meets the required specifications for strength, flexibility, and load capacity.
Automation and Efficiency: The Role of Starlinger and W&H Equipment
To further enhance the performance of Sewn Open Mouth Bags, manufacturers have embraced advanced automation technologies from leading equipment suppliers, including Starlinger and W&H. These companies are renowned for producing high-efficiency machinery that integrates seamlessly into the production process. By using automated systems, manufacturers can increase the production speed of Sewn Open Mouth Bags while ensuring consistent quality.
Key Features of Starlinger and W&H Equipment:
- Automation for High Throughput
Modern machinery from Starlinger and W&H can produce more than 200 bags per minute, significantly increasing production capacity and reducing lead times. This high-speed production is essential for manufacturers looking to meet growing demand while maintaining product quality. - Multi-Machine Integration
Both Starlinger and W&H machines support multi-machine operations, where several machines work in tandem to optimize production. This interconnectivity ensures that the production process is streamlined, and the production lines are more efficient. - Precision Control
These machines offer precise control over the entire manufacturing process, from weaving the PP yarn to printing and stitching the bags. The automated systems minimize human error, resulting in higher-quality Sewn Open Mouth Bags with fewer defects. - Sustainability and Waste Reduction
The high efficiency of these automated systems also contributes to sustainability efforts. By optimizing material usage and minimizing waste, these machines help manufacturers reduce their environmental footprint. - Customization Flexibility
Advanced printing and lamination technology allow for high levels of customization on Sewn Open Mouth Bags. Manufacturers can produce bags in a variety of colors, designs, and closures, offering tailored solutions for different industries.
Conclusion: The Future of Sewn Open Mouth Bags
Sewn Open Mouth Bags continue to be a cornerstone of packaging solutions due to their durability, flexibility, and customizability. The impact of drawn yarn technology on enhancing the performance of these bags cannot be overstated, as it significantly improves their strength, tear resistance, and flexibility. With the integration of cutting-edge machinery from Starlinger and W&H, the production process has become more efficient, allowing for faster turnaround times and reduced costs.
As industries continue to demand higher-quality, more sustainable packaging solutions, Sewn Open Mouth Bags will remain a top choice for bulk packaging. The continuous improvements in material science, production technology, and automation will only serve to further elevate the performance of these bags, making them even more integral to the future of packaging solutions.
For more detailed insights on the versatility of Sewn Open Mouth Bags and the innovations in Open Mouth Bags production, explore this comprehensive guide and learn more about Open Mouth Bags.