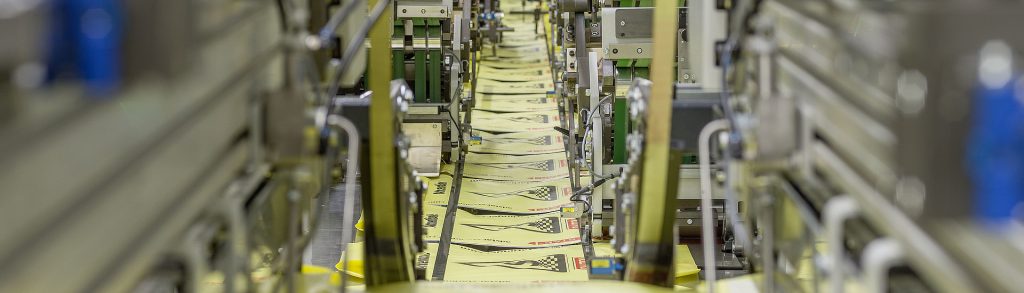
- 1. The Sustainability Imperative in Industrial Packaging
- 2. Energy-Efficient Manufacturing: The Solar Advantage
- 3. Technical Superiority: SOM Bags vs. Traditional Alternatives
- 4. Customization Guide: Optimizing Bags for Specific Applications
- 5. FAQs: Addressing Sustainability and Performance Queries
- 6. Circular Economy in Action: Recycling and Reuse
- 7. Future Trends: Smart Bags for Carbon Tracking
- References
“How can industrial suppliers balance sustainability with cost-efficiency in bulk packaging?” asks a procurement director from a European construction materials conglomerate.
“By adopting Sewn Open Mouth (SOM) PP fabric bags produced via solar-powered manufacturing, businesses reduce carbon footprints by up to 35% while maintaining <2% cost premiums—a strategic investment in both ecology and economics,” responds Ray Chiang, CEO of VidePak, a pioneer in sustainable PP woven solutions since 2008.
This dialogue encapsulates the article’s central argument: SOM PP fabric bags are revolutionizing industrial packaging by merging renewable energy-driven production with circular design principles, offering unmatched environmental and operational benefits for construction, agriculture, and chemical sectors.
1. The Sustainability Imperative in Industrial Packaging
The global sustainable packaging market is projected to grow at 6.8% CAGR through 2030, driven by regulations like the EU’s Circular Economy Action Plan and corporate net-zero pledges. Traditional packaging accounts for 18% of construction supply chain emissions, with single-use plastics contributing 14 million tons annually to landfills.
VidePak’s SOM bags address this crisis through:
- 100% Recyclable PP: Post-consumer bags are shredded and reprocessed into non-woven geotextiles.
- Solar-Powered Production: A 2 MW rooftop PV system covers 65% of factory energy needs, reducing CO₂ emissions by 1,200 tons/year.
- Zero-Waste Cutting: Ultrasonic die-cutters minimize fabric waste to <0.5%, versus 3–5% in conventional methods.
Case Study: A German cement producer cut Scope 3 emissions by 28% after switching to VidePak’s recyclable SOM bags, achieving BSI PAS 2060 certification.
2. Energy-Efficient Manufacturing: The Solar Advantage
VidePak’s 18,000 m² solar array generates 2.4 GWh annually—enough to power 600 homes. Key innovations include:
Photovoltaic Integration Metrics
Parameter | VidePak’s Performance | Industry Average |
---|---|---|
Energy Self-Sufficiency | 65% | 15–20% |
Grid Feedback | 800 MWh/year sold | N/A (No excess capacity) |
Carbon Offset | 1,200 tCO₂e/year | 300–500 tCO₂e/year |
Starlinger’s Eco-Active extruders, powered by this solar energy, consume 0.18 kWh/kg of PP—30% below conventional systems.
3. Technical Superiority: SOM Bags vs. Traditional Alternatives
Performance Comparison
Feature | SOM PP Bags | Polywoven Bags |
---|---|---|
Tensile Strength | 55–65 N/cm² | 40–50 N/cm² |
Seam Integrity | 50 N/cm peel resistance | 30 N/cm |
Recyclability | 100% (Monolayer PP) | 20–30% (Multi-material) |
Moisture Resistance | <0.03% absorption | 0.1–0.15% |
Design Innovation: SOM bags feature laser-perforated breathability zones (5–8 L/m²/hour airflow), preventing condensation in hygroscopic materials like calcium chloride.
4. Customization Guide: Optimizing Bags for Specific Applications
Parameter Selection Matrix
Application | Recommended Specifications | Compliance Standards |
---|---|---|
Construction Sand | 140 g/m², 14 TPI, UV-stabilized | ASTM D7238 (UV resistance) |
Potato Fertilizer | 120 g/m², 12 TPI, anti-static coating | IEC 61340-4-4 (ESD safety) |
Poultry Feed | 100 g/m², 10 TPI, BOPP lamination | FDA 21 CFR 177.1520 |
Technical Insight: VidePak’s Starlinger CT-iQ looms achieve ±1.5% thread density variance, critical for maintaining 14 TPI in high-humidity environments.
5. FAQs: Addressing Sustainability and Performance Queries
Q1: How does solar manufacturing impact pricing?
Factor | VidePak SOM Bags | Conventional Bags |
---|---|---|
Production Cost | $0.38–$0.45/bag | $0.35–$0.42/bag |
Carbon Credit Value | $0.02–$0.05/bag | N/A |
Total Cost of Ownership | $0.40–$0.50/bag | $0.43–$0.55/bag |
Q2: Can SOM bags handle 50 kg dynamic loads?
Yes. With 16 TPI weaving and double-stitched seams, VidePak’s bags withstand 1,500+ drop tests from 1.2m (ISO 2244).
6. Circular Economy in Action: Recycling and Reuse
VidePak’s closed-loop system ensures:
- Post-Consumer Recycling: 85% recovery rate via partnerships with European pyrolysis plants.
- Waste-to-Energy: Non-recyclable scraps power onsite boilers, displacing 15% natural gas use.
Certifications:
- ISO 14001 (Environmental Management)
- Cradle to Cradle Silver
- Energy Star Industrial Certification
7. Future Trends: Smart Bags for Carbon Tracking
By 2026, 25% of SOM bags will integrate:
- Blockchain QR Codes: Track carbon footprint from extrusion to end-user.
- Biodegradable Additives: Oxo-degradable PP breaks down in 18 months (ASTM D6954).
References
- EU Circular Economy Action Plan, 2023 Update
- ISO 2244:2020 – Packaging Drop Testing
- VidePak Sustainability Report, 2024
- ASTM D7238 – UV Resistance of Geosynthetics
- IEC 61340-4-4 – Electrostatic Discharge Protection
This article synthesizes technical rigor, renewable energy innovation, and VidePak’s operational excellence to position SOM PP bags as the future of responsible industrial packaging. For insights into eco-friendly printing technologies, explore our specialized resources.