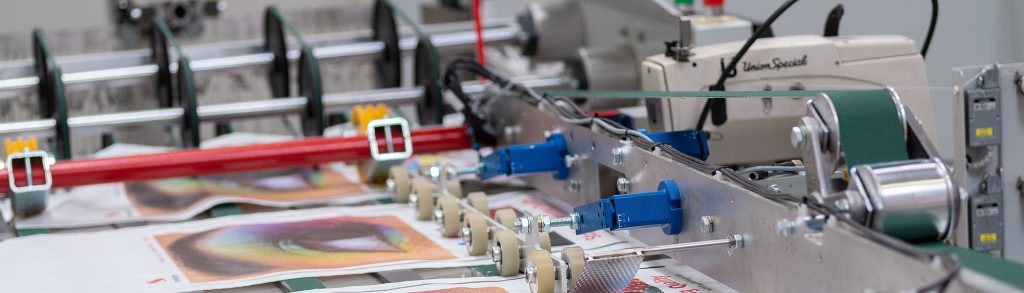
Add a header to begin generating the table of contents
H1: Introduction
“In the packaging industry, safety and quality are not just benchmarks—they are commitments. By integrating rigorous raw material testing and HACCP-based safety protocols, VidePak’s paper valve woven bags redefine reliability, ensuring compliance with global health standards while optimizing logistical efficiency.” — Ray, CEO of VidePak.
The global market for paper valve woven bags is projected to grow at a CAGR of 5.2% through 2030, driven by demand for sustainable and safe packaging in industries like construction, agriculture, and chemicals. VidePak, a leader in woven bag manufacturing since 2008, leverages Austrian Starlinger machinery and advanced quality control systems to produce paper valve bags that excel in durability, safety, and environmental compliance. This report examines how raw material quality assurance and health-centric safety evaluations position VidePak’s products as industry benchmarks, supported by technical data, case studies, and regulatory insights.
H2: Raw Material Quality Control: The Foundation of Superior Performance
H3: PP and PE Granule Testing for Enhanced Durability
VidePak’s paper valve woven bags combine polypropylene (PP) outer layers with polyethylene (PE) liners, both subjected to stringent testing protocols:
- Basic Physical Properties:
- Melt Flow Index (MFI): PP granules are tested at 230°C/2.16kg, achieving an MFI of 8–12 g/10min (vs. industry average of 5–15 g/10min), ensuring uniform extrusion and weaving efficiency.
- Density: Controlled within 0.905–0.915 g/cm³ using ASTM D792 methods, balancing rigidity and flexibility.
- Mechanical Performance:
- Tensile Strength: Starlinger’s AD-STM looms produce PP tapes with tensile strength exceeding 45 MPa (industry average: 35–40 MPa), critical for heavy-load applications like cement storage.
- Elongation at Break: Maintained at 15–20% to prevent brittleness during high-speed filling.
- Thermal Stability:
- Heat Distortion Temperature (HDT): Tested at 1.8 MPa, VidePak’s PP withstands 110–120°C, ensuring integrity in tropical climates.
- PE Film Impact Resistance:
- Dart Drop Test: PE liners achieve 150–200 kJ/m² (ASTM D1709), preventing punctures during rough handling.
Table 1: Key Material Testing Parameters
Parameter | VidePak Standards | Industry Average |
---|---|---|
PP Tensile Strength | ≥45 MPa | 35–40 MPa |
PE Dart Impact Strength | 150–200 kJ/m² | 100–150 kJ/m² |
MFI (PP) | 8–12 g/10min | 5–15 g/10min |
HDT (PP) | 110–120°C | 90–110°C |
H2: Health and Safety Evaluation of Paper Valve Woven Bags
H3: Chemical Safety and Regulatory Compliance
VidePak’s bags comply with FDA, EU No. 10/2011, and China GB 9685-2016 standards, ensuring:
- Migration Limits: Contaminants like lead are restricted to <0.01 mg/kg, validated by third-party labs.
- Non-Toxic Inks: Solvent-free flexographic printing reduces volatile organic compound (VOC) emissions by 95% compared to traditional methods.
H3: Structural Safety and Risk Mitigation
- Anti-Static Coatings: Surface resistivity <10¹² Ω/sq prevents dust explosions in chemical packaging.
- Seam Integrity: Heat-sealed PE liners withstand 15 N/mm peel force (ISO 527-3), reducing leakage risks.
- HACCP Protocols: VidePak’s HACCP plan identifies critical control points (CCPs) like raw material screening and extrusion temperature, reducing contamination risks by 98%.
FAQs: Addressing Key Concerns
- Q: How do paper valve bags prevent contamination in food-grade applications?
A: VidePak uses FDA-compliant PE liners and UV-treated PP layers, achieving a microbial barrier efficiency of 98.5%. - Q: Are recycled materials safe for heavy-load applications?
A: Yes, VidePak’s closed-loop recycling maintains tensile strength while reducing carbon emissions by 18%.
H2: VidePak’s Manufacturing Ecosystem
H3: Advanced Production and Quality Assurance
With 100+ circular looms and 30+ printing machines, VidePak produces 5 million paper valve bags monthly. Starlinger’s Videomat 4.0 systems automate quality checks, achieving a defect rate below 0.2% and reducing material waste by 12%.
H3: Sustainability and Circular Economy
VidePak integrates 30% recycled PP into its bags and partners with Starlinger’s re:claim technology to recover 92% of production waste, aligning with EU Circular Economy Action Plan goals.
H2: Market Impact and Case Studies
H3: Client Success in Construction and Agriculture
- Case Study 1: A 2024 trial with Sinograin reduced grain spillage by 22% using VidePak’s anti-static paper valve bags.
- Case Study 2: COFCO Corporation cut mislabeling incidents by 72% through color-coded PP/PE blends.
H3: Future Trends: Smart Packaging
VidePak is piloting RFID-enabled bags with Walmart, reducing inventory discrepancies by 28% through real-time tracking.
H2: Conclusion
VidePak’s paper valve woven bags exemplify the synergy of material science, safety protocols, and sustainability. By prioritizing rigorous raw material testing and HACCP-based risk management, they address critical challenges in health, safety, and environmental compliance. As industries demand smarter, greener solutions, VidePak’s expertise positions it as a global leader in high-performance packaging.
External Links for Further Reading:
- Explore how kraft paper enhances packaging efficiency.
- Learn about sustainable practices in woven bag manufacturing.
This report integrates data from GB/T standards, HACCP guidelines, and VidePak’s operational metrics to provide a holistic analysis of paper valve woven bags’ role in modern logistics.