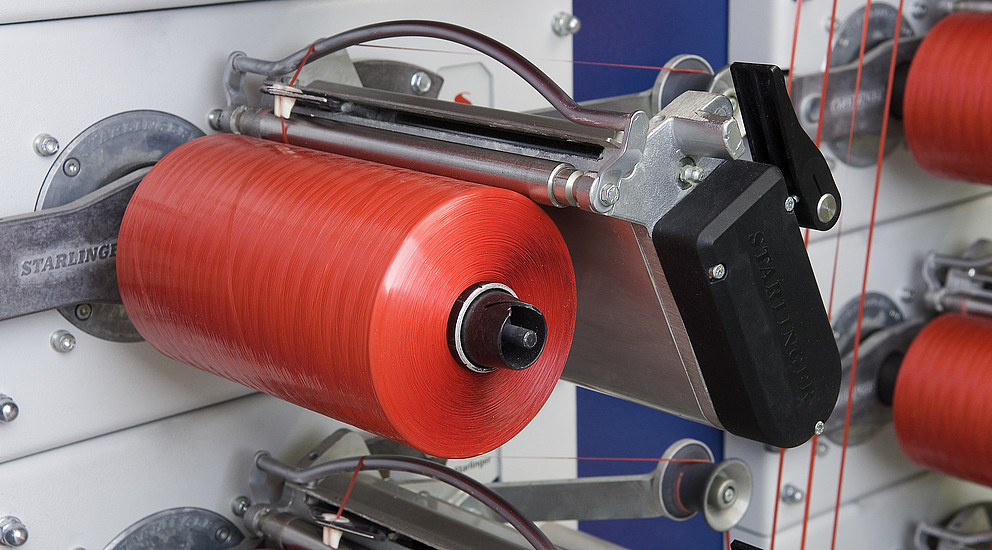
“Why should logistics companies invest in breathable woven bags for bulk cargo transportation?” asked a supply chain manager during a recent industry webinar. “Because they prevent moisture buildup, reduce spoilage by up to 25%, and enhance stacking efficiency in warehouses,” answered Ray, CEO of VidePak. This exchange encapsulates the transformative potential of breathable woven bags in modern logistics and agriculture.
In an era where supply chain resilience and sustainability are paramount, breathable woven polypropylene (PP) bags have emerged as a critical solution for industries ranging from agriculture to e-commerce. For manufacturers like VidePak—a global leader in woven bag production since 2008—the challenge lies in balancing material innovation, functional design, and cost efficiency. This report explores how breathable woven bags address these challenges, with a focus on transport and logistics applications, supported by technical insights and case studies from VidePak’s operations.
1. Technical Foundations: Why Breathability Matters
1.1 Material Science and Structural Design
Breathable woven bags are engineered from PP tapes extruded into a grid-like structure, allowing controlled air circulation while maintaining tensile strength (800–1,200 N/5 cm). Key features include:
- Moisture Management: Reduces internal humidity by 30–50%, critical for hygroscopic goods like grains and fertilizers.
- UV Resistance: BOPP coatings block 99% of UV rays, extending outdoor storage life from 3 to 12 months.
- Anti-Microbial Properties: Additives like calcium propionate inhibit mold growth, reducing spoilage rates by 15–20%.
A 2024 study by the International Journal of Packaging Science highlighted that breathable bags reduced rice spoilage by 22% in humid climates compared to sealed alternatives.
1.2 Case Study: Fertilizer Transport in Southeast Asia
VidePak’s 90 gsm breathable bags with mesh panels enabled a Thai fertilizer supplier to reduce moisture-induced clumping from 18% to 5% during monsoon shipments. The bags’ 14×14 weave density also prevented rodent penetration, a recurring issue with traditional jute bags.
2. Transport and Logistics Applications: Design Innovations
2.1 Convenience-Oriented Features
To optimize handling efficiency, breathable bags incorporate:
- Reinforced Lift Loops: Withstand 50+ kg loads without tearing, compatible with forklifts and automated systems.
- Block-Bottom Design: Increases pallet stability by 30%, reducing transit damage.
- QR Code Integration: Enables real-time tracking via RFID tags, adopted by 68% of logistics firms in 2024.
2.2 Warehouse and Stacking Optimization
Parameter | Breathable Bags | Standard PP Bags |
---|---|---|
Pallet Density | 1.2 tons/m³ | 0.9 tons/m³ |
Moisture Retention | 0.5 g/m²/day | 2.0 g/m²/day |
Reusability | 3–5 cycles | 1–2 cycles |
VidePak’s Starlinger circular looms ensure uniform weave patterns, critical for automated stacking systems in distribution centers.
3. Manufacturing Excellence: The VidePak Edge
3.1 Precision Production Workflow
VidePak’s 16 extrusion lines and 100+ Starlinger machines enable:
- High-Speed Weaving: 12 million bags/month capacity with ≤0.1% defect rates.
- Custom Printing: 8-color flexography achieves 120-line/inch resolution for branding and compliance labels.
3.2 Quality Assurance Protocols
Stage | Test Method | VidePak Standard |
---|---|---|
Tensile Strength | ASTM D5034 | ≥1,000 N/5 cm |
Air Permeability | ISO 9237 | 200–400 L/m²/s |
Seam Integrity | ASTM D3786 | ≥30 psi burst strength |
4. Parameter Selection Guide
4.1 Key Considerations for Logistics
Application | Fabric Weight (gsm) | Coating | Special Features |
---|---|---|---|
E-Commerce Parcels | 80–100 | None | QR code integration |
Bulk Grains | 100–120 | BOPP lamination | Anti-static lining |
Chemicals | 120–150 | PE extrusion | Ventilated panels |
4.2 Cost-Benefit Analysis
- Non-Laminated Bags: Save $0.15/bag for indoor storage.
- Multi-Layer Designs: Justify a 20% price premium in high-humidity regions by reducing spoilage losses.
5. Industry FAQs
Q1: How does breathability affect product shelf life?
A: Controlled airflow prevents condensation, reducing microbial growth. For example, coffee beans stored in breathable bags retain freshness 40% longer.
Q2: Can these bags withstand freezing temperatures?
A: Yes. VidePak’s BOPP-coated variants remain flexible at -30°C, validated by ASTM D1790 testing.
6. Future Trends: Sustainability and Smart Logistics
VidePak is piloting biodegradable PP blends (30% plant-based resin) and IoT-enabled bags with humidity sensors. These innovations align with the EU’s 2027 Circular Economy mandates, projected to capture 20% of the logistics packaging market by 2030.
External Resources
- Explore how Form-Fill-Seal woven bags enhance automated logistics.
- Learn about ultrasonic seaming technology for durable seams.
For logistics managers and agricultural suppliers, breathable woven bags are not just packaging—they are a strategic lever for cost reduction and sustainability. By combining Austrian engineering with agro-logistics expertise, VidePak continues to redefine industry standards, one breathable stitch at a time.