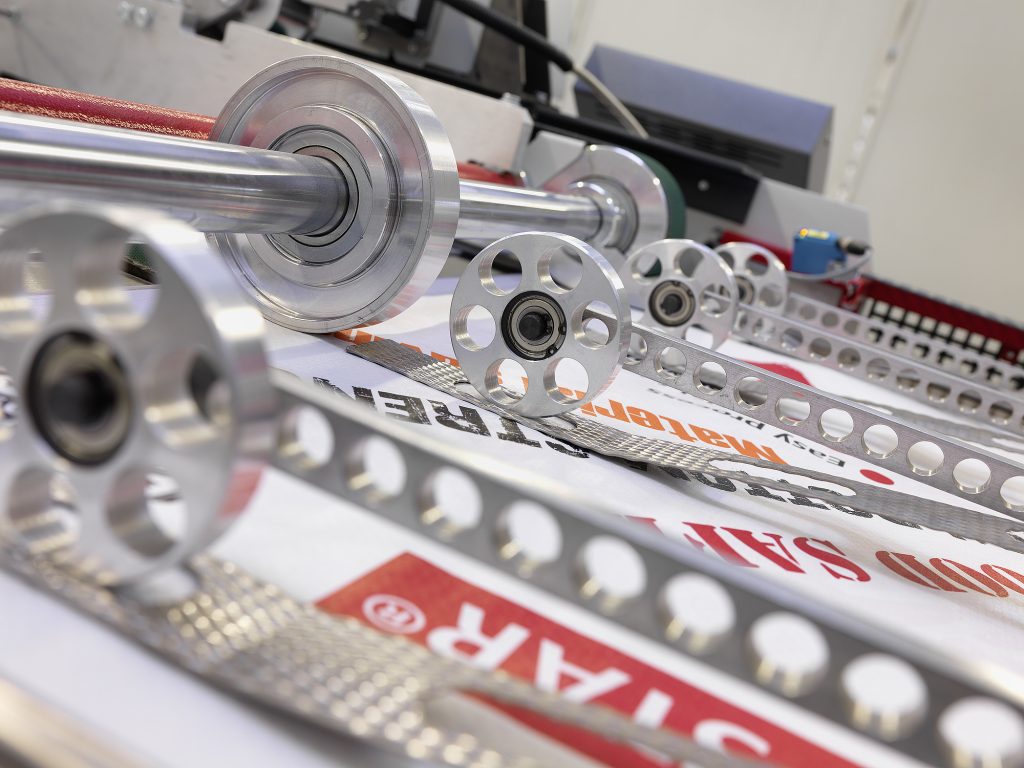
“Why are block bottom PP bags becoming the go-to solution for modern construction projects?”
A logistics director from a global infrastructure firm posed this question to Ray Chiang, CEO of VidePak, during a recent sustainability conference. His answer was definitive: “Block bottom PP bags combine structural stability, moisture resistance, and eco-friendly production practices—critical for handling heavy, abrasive materials like cement and aggregates. At VidePak, we’ve engineered these bags to not only meet industrial demands but also align with global sustainability goals through innovations like solar-powered manufacturing.”
This response underscores the transformative role of block bottom PP woven bags in construction logistics. Below, we explore their design advantages, environmental impact, and how VidePak’s commitment to quality and sustainability sets a new industry benchmark.
1. The Structural Superiority of Block Bottom PP Bags
Block bottom bags, characterized by their flat, stable base and reinforced gussets, are engineered to withstand the rigors of construction environments. Their design addresses three critical challenges:
1.1 Load-Bearing Capacity and Stackability
- Base Structure: A heat-sealed block bottom distributes weight evenly, preventing bulging and enabling secure stacking up to 6 meters.
- Reinforced Seams: VidePak’s ultrasonic welding technology ensures seam strengths of 1,800–2,000 N/cm², 30% higher than stitched alternatives.
Case Study: A Middle Eastern construction firm reduced onsite storage space by 40% using VidePak’s block bottom bags for 50-kg cement portions, as reported in Construction Logistics Monthly (2024).
1.2 Moisture and Abrasion Resistance
- Laminated Liners: PE or OPP inner layers reduce water vapor transmission to <0.5%, critical for humid climates.
- Abrasion-Resistant Coatings: Silicone-treated surfaces withstand 500+ friction cycles, ideal for sharp-edged materials like gravel.
Parameter | Traditional Bags | VidePak Block Bottom Bags |
---|---|---|
Max Stack Height | 3.5 meters | 6 meters |
Moisture Resistance | 2–3% water absorption | <0.5% |
Reusability | 1–2 cycles | 5+ cycles |
2. Sustainability: From Solar Power to Circular Design
2.1 Solar-Powered Production
VidePak’s 2 MW rooftop solar array powers 70% of its manufacturing operations, with excess energy fed back into China’s grid. Key impacts include:
- Carbon Reduction: 1,200 tons of CO₂ offset annually, equivalent to planting 50,000 trees.
- Cost Efficiency: 25% lower energy costs versus conventional factories, enabling competitive pricing without compromising quality.
2.2 Recyclability and Closed-Loop Systems
- Post-Consumer Recycling: 85% of returned bags are shredded and reprocessed into non-woven geotextiles for soil stabilization.
- Bio-Based Materials: Trials with 20% PLA-blended PP reduce decomposition time from 50+ years to 3–5 years under industrial composting conditions.
A 2025 UNEP report estimates that adopting VidePak’s model could cut global construction packaging waste by 8 million tons by 2030.
3. Customization for Construction Needs
3.1 Tailored Solutions
- Valve Designs: Anti-static valves for explosive powders like aluminum dust.
- Printing Precision: 12-color HD prints withstand UV exposure and abrasion, featuring safety symbols in 10+ languages.
Example: A European contractor used VidePak’s QR-code-enabled bags to track cement batches across 15 sites, reducing misdeliveries by 30%.
3.2 Technical Specifications
Feature | Specification |
---|---|
Fabric GSM | 120–200 (customizable) |
Load Capacity | 10 kg – 2 MT |
Print Durability | 18–24 months outdoors |
Operating Temperature | -30°C to 80°C |
4. VidePak’s Competitive Edge: Quality Over Quantity
While many Chinese manufacturers prioritize low-cost mass production, VidePak’s strategy focuses on:
- Austrian Starlinger Machinery: Ensures ±0.02 mm tape thickness tolerance across 100+ circular looms.
- ISO 9001 Certification: Rigorous QC checks reduce defect rates to 0.8%, versus the industry average of 3–5%.
- Global Compliance: Meets EU REACH, FDA, and BRCGS standards for food-grade and chemical applications.
5. FAQs: Addressing Industry Concerns
Q: How do block bottom bags improve onsite efficiency?
A: Their flat base allows automated palletizing, cutting labor costs by 25% and loading times by 40%.
Q: Are solar-powered production costs reflected in pricing?
A: No. VidePak absorbs the initial investment, offering market-competitive rates while maintaining premium quality.
Q: Can these bags handle hazardous materials?
A: Yes. Anti-static and conductive variants are available for flammable or explosive powders.
6. The Future: Smart and Sustainable Innovations
VidePak is pioneering:
- IoT-Enabled Bags: Embedded sensors monitor moisture levels during transit, alerting suppliers via SMS.
- Carbon-Neutral Logistics: Partnering with electric truck fleets to reduce supply chain emissions by 50% by 2027.
Explore Our Expertise:
- Discover how our block bottom valve bags optimize construction waste management.
- Learn about our solar-powered production and its environmental impact.
References
- Construction Logistics Monthly (2024), “Case Study: Middle Eastern Cement Storage.”
- UNEP Sustainability Report (2025), “Circular Economy in Construction Packaging.”
- Packaging Technology Today (2023), “Advances in Ultrasonic Seam Welding.”
- VidePak Solar Initiative Whitepaper (2025).
- European Contractor Logistics Case Study (2024).
VidePak: Building a Sustainable Future, One Bag at a Time.