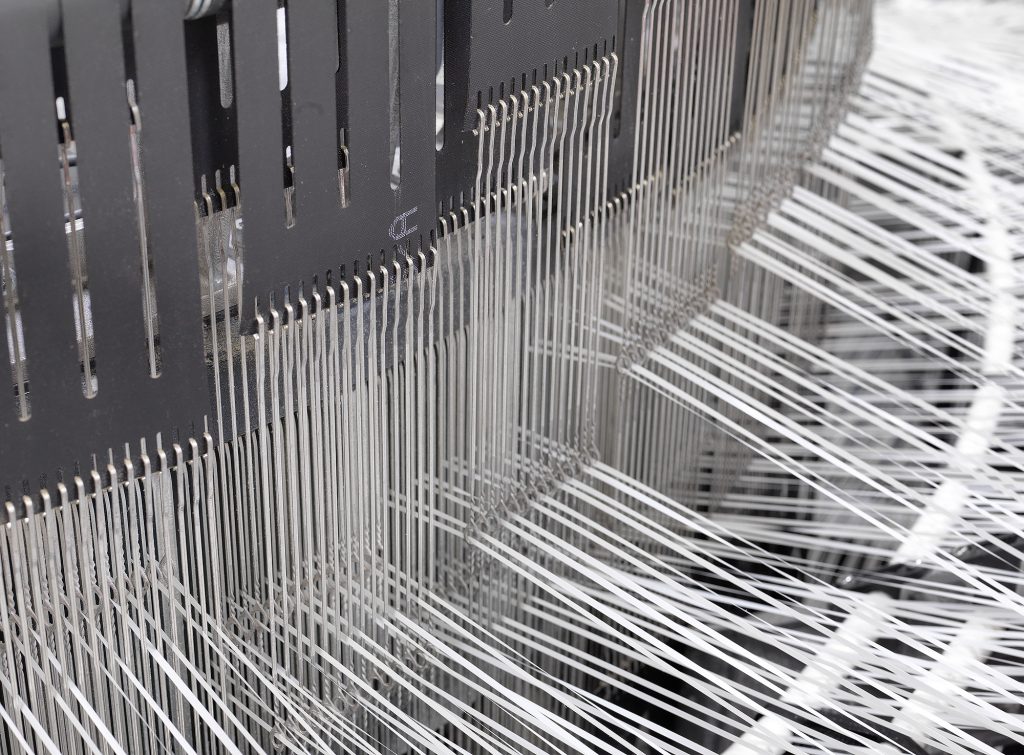
Sewn Open Mouth (SOM) polypropylene (PP) bags are a critical solution for food packaging, renowned for their durability, customizability, and cost efficiency. This report explores the meticulous production process that ensures product reliability, highlights the advanced technology used, and discusses the quality control measures that set industry leaders like VidePak apart.
Production Process for SOM PP Bags
1. Extrusion
High-quality polypropylene granules are melted and extruded into thin, consistent tapes, which form the foundation of SOM PP bags. This stage directly affects the strength and flexibility of the final product. VidePak uses advanced extrusion systems from Starlinger, which ensure uniformity and minimize material waste.
Key Quality Controls:
- Material Integrity: Only virgin polypropylene is used to maintain tensile strength and reduce contamination.
- Temperature Precision: Automated systems maintain optimal extrusion conditions to prevent tape inconsistencies.
2. Drawing (Stretching)
The tapes are stretched to align polymer chains, enhancing their tensile strength and flexibility. This process is crucial for creating a fabric that resists tearing under heavy loads.
Key Quality Controls:
- Controlled Tensioning: Prevents over-stretching, which can weaken tapes.
- Thickness Verification: Laser systems measure tape dimensions to ensure uniformity.
3. Weaving
The stretched tapes are woven into fabric using high-speed looms. The weaving pattern determines the bag’s strength and load capacity. For instance, a 12×12 weave is preferred for heavier applications like rice or flour packaging.
Key Quality Controls:
- Weave Density Checks: Ensures that the fabric can support specified loads.
- Defect Monitoring: Automated systems detect and correct broken or loose tapes.
4. Lamination
The woven fabric is laminated with a polypropylene film for added moisture resistance and printability. VidePak uses cutting-edge lamination technology from W&H to achieve seamless bonding and a smooth surface for printing.
Key Quality Controls:
- Adhesion Testing: Ensures the lamination withstands environmental stressors like humidity.
- Surface Smoothness: Verifies that the laminated fabric is free from bubbles or creases.
5. Printing
High-definition flexographic and gravure printing methods allow for precise, multi-color designs. VidePak’s printing capabilities include both matte and glossy finishes, enhancing branding opportunities for food packaging.
Key Advantages:
- High Clarity: Advanced printing technology ensures vibrant colors and sharp details.
- Customizable Designs: Accommodates complex branding requirements, boosting market appeal.
6. Bag-Making
The fabric is cut and sewn or sealed into bags. Closure options include sewn, heat-sealed, and ultrasonic sealing, each tailored to specific packaging needs.
Comparison of Closure Methods:
- Sewn Closures: Offer durability for heavy loads but may allow minimal moisture ingress.
- Heat-Sealed Closures: Provide airtight sealing, ideal for moisture-sensitive products like flour.
- Ultrasonic Sealing: Combines strength with superior moisture resistance, eliminating the need for stitching threads.
Advantages of SOM PP Bags in Food Packaging
SOM PP bags offer unmatched performance in food packaging due to their versatile features and robust design.
Feature | Benefit |
---|---|
Strength and Durability | Supports heavy loads, thanks to the woven structure and high-quality lamination. |
Moisture Resistance | Laminated surfaces protect food from environmental humidity. |
Customizability | Available in various sizes, colors, and finishes to meet branding needs. |
Eco-Friendliness | Recyclable materials minimize environmental impact. |
These qualities make SOM PP bags a preferred choice for packaging products like rice, flour, and pet food, where strength, safety, and presentation are critical.
Innovations in Production Technology
Advanced Machinery
VidePak leverages equipment from Starlinger and W&H, leaders in bag production technology, ensuring high precision and efficiency at every stage of manufacturing. For example, Starlinger’s extrusion lines enable tighter control over tape dimensions, while W&H’s printing systems deliver exceptional color accuracy.
Sustainable Practices
Sustainability is at the forefront of modern packaging. SOM PP bags are fully recyclable, and production processes are optimized to reduce energy consumption and waste. VidePak also aligns with global standards, as seen here.
FAQs
Q: What makes SOM PP bags suitable for heavy food products?
A: The woven polypropylene fabric, reinforced by lamination, provides excellent tensile strength and puncture resistance. Additionally, closure options like ultrasonic sealing ensure secure packaging.
Q: Are these bags customizable for different branding needs?
A: Yes, VidePak offers multi-color printing with matte or glossy finishes, making SOM PP bags a powerful branding tool.
Q: How do you ensure consistent quality across production?
A: VidePak employs rigorous quality checks at each stage, from extrusion to bag-making. Advanced machinery and automated systems ensure adherence to the highest standards.
Technical Specifications
Specification | Detail |
---|---|
Material | Woven Polypropylene |
Capacity Range | 5–50 kg |
Closure Options | Sewn, Heat-Sealed, Ultrasonic |
Printing Capability | Up to 8 colors, matte/glossy finishes |
Lamination Thickness | 30–50 microns |
Conclusion
The production of SOM PP bags is a precise and quality-driven process that ensures reliability and versatility in food packaging. From extrusion to printing, every stage is optimized using advanced equipment from Starlinger and W&H. VidePak’s commitment to innovation, sustainability, and quality control makes it a trusted partner for food packaging solutions.
For more on VidePak’s approach to quality and customization, visit this link.