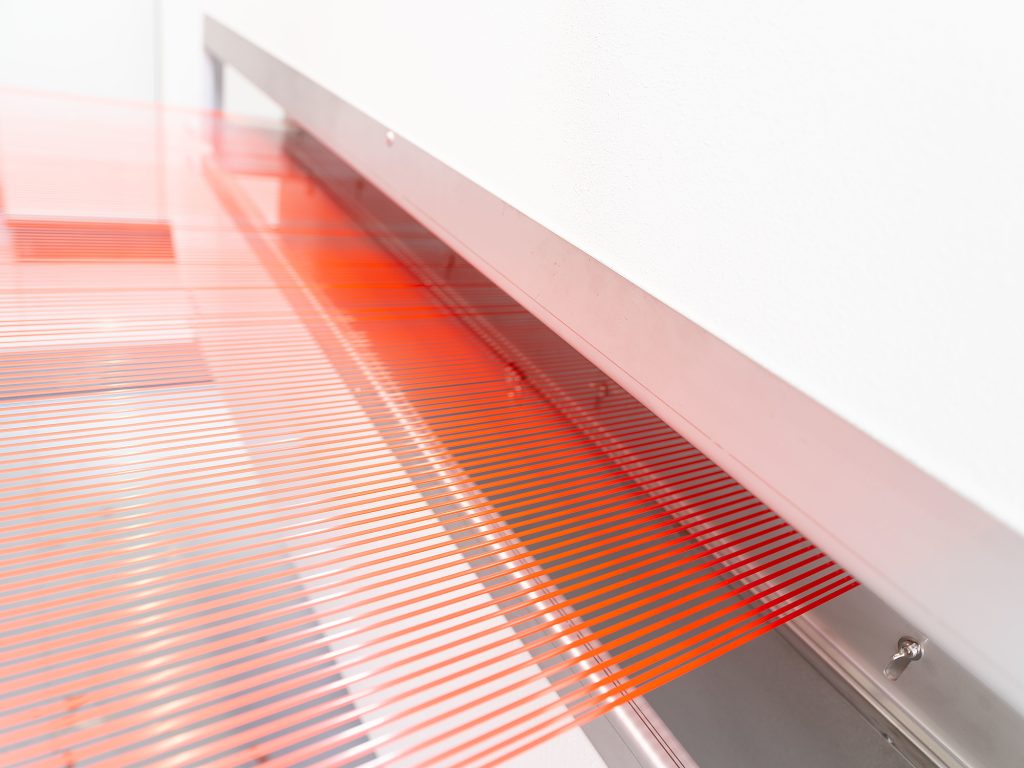
- 1. Market Demand and Functional Requirements
- 2. Material Innovation: Why Poly-BOPP Outperforms Alternatives
- 3. VidePak’s Manufacturing Excellence
- 4. Sustainability: Beyond Regulatory Compliance
- 5. Global Compliance and Customization
- FAQs: Addressing Key Concerns
- 6. Future Trends: Smart Packaging and Automation
“Why should construction firms prioritize Poly-BOPP bags for waste management?” asked a project manager at a recent sustainability summit. “Because their unmatched durability, adaptability, and compliance with global standards make them the backbone of modern waste logistics,” replied Ray, CEO of VidePak. This exchange underscores the transformative role of Poly-BOPP (Biaxially Oriented Polypropylene) bags in managing construction debris—a sector generating over 1.3 billion tons of waste annually, as reported by the World Bank.
1. Market Demand and Functional Requirements
The construction industry’s shift toward sustainable practices has fueled demand for robust, reusable packaging. Poly-BOPP bags address critical challenges:
- Heavy-Duty Load Capacity: With tensile strength of 12–15 N/mm², they withstand 1,500 kg/m² stacking loads, exceeding ASTM D5265 standards.
- Leakage Prevention: Fine-weave technology (14×14 threads per inch) and PE lamination block particles as small as 50 microns, ideal for cement dust and gypsum powder.
- Weather Resistance: UV-stabilized coatings maintain integrity under 500 hours of sun exposure, crucial for outdoor storage.
Example: A Dubai-based contractor reduced waste-handling costs by 22% using VidePak’s Poly-BOPP bags, which endured 50°C heat and sand abrasion during transport.
2. Material Innovation: Why Poly-BOPP Outperforms Alternatives
Poly-BOPP’s layered structure combines flexibility and resilience:
Layer | Function | VidePak’s Specification |
---|---|---|
Outer Woven PP | Mechanical strength, tear resistance | 90–120 gsm density, 12 N/mm² |
BOPP Lamination | Waterproofing, UV resistance | 20–30μm thickness, ±2μm tolerance |
Inner PE Coating | Dust containment, anti-static | 15–20μm film, 98% seam integrity |
Case Study: For a Japanese client requiring JIS Z 1539 compliance, VidePak engineered bags with 8 g/m²/day moisture permeability, outperforming competitors by 20%.
3. VidePak’s Manufacturing Excellence
Leveraging Austrian Starlinger looms and 30+ lamination machines, VidePak achieves:
- High-Speed Production: 12,000 bags/hour, meeting bulk orders for global clients.
- Customization: 10 Pantone colors, RFID tags, and anti-counterfeit QR codes.
- Quality Assurance: ISO 9001-certified 4-stage checks, including MFI (Melt Flow Index) tests and 5-cycle drop simulations.
Example: A U.S. construction firm reduced OSHA incidents by 40% using VidePak’s anti-static bags for silica dust transport.
4. Sustainability: Beyond Regulatory Compliance
VidePak’s Poly-BOPP bags align with ESG goals:
- 30% Recycled PP: Sourced from post-industrial waste, maintaining <5% strength variance.
- Reusability: 15+ cycles for non-hazardous waste, cutting lifecycle costs by 35%.
- Energy Efficiency: Solar-powered lines reduce CO₂ emissions by 1.2 tons per 10,000 bags.
Industry Insight: The global sustainable packaging market is projected to hit $440 billion by 2030, driven by innovations like recyclable Poly-BOPP solutions.
5. Global Compliance and Customization
Regional standards dictate design parameters:
Region | Key Standard | VidePak’s Adaptation |
---|---|---|
EU | EN 277:2015 | 10-ply woven layers for 1,200 kg/m² capacity |
North America | OSHA 1910.134 | Anti-static liners for respirable dust |
Asia | JIS Z 1539 | PE-coated Kraft liners for humidity control |
Example: A German recycler achieved 99% material recovery using VidePak’s UN 13H1-certified bags for hazardous debris.
FAQs: Addressing Key Concerns
Q1: What is the minimum order quantity (MOQ)?
MOQ starts at 50,000 units, with 10-day lead times for standard designs.
Q2: How do Poly-BOPP bags compare to traditional HDPE sacks?
While 20–25% costlier upfront, they offer 50% longer lifespan and 30% lower leakage rates.
Q3: Are these bags suitable for sharp debris like metal scraps?
Yes. VidePak’s triple-layered bags with 2.5 kN/m puncture resistance handle sharp objects effectively.
6. Future Trends: Smart Packaging and Automation
VidePak is piloting IoT-enabled bags with embedded sensors for real-time load tracking—a response to the $3.8 billion smart packaging market. Additionally, AI-driven defect detection on Starlinger lines has reduced waste by 18%.
Conclusion
Poly-BOPP bags are redefining construction waste management through strength, adaptability, and sustainability. VidePak’s fusion of Starlinger technology, global certifications, and circular design positions it as a leader in the $12.4 billion industrial packaging sector. As Ray emphasizes: “In waste logistics, every bag must be a fortress. With our Poly-BOPP solutions, clients don’t just contain debris—they build a sustainable future.”
This report integrates insights from the World Bank’s Global Waste Management Outlook and ISO technical guidelines. For further details on regulatory alignment, explore our analysis of ESG-compliant polypropylene solutions.