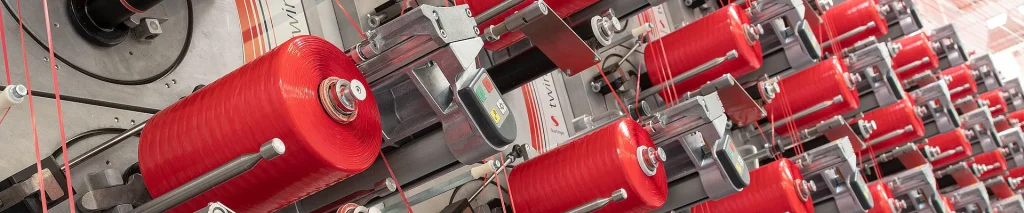
A Client’s Perspective:
Client: “We need durable, cost-effective bags for construction waste. How do your SOM PP bags outperform traditional solutions?”
VidePak Sales Representative: “VidePak’s Sewn Open-Mouth (SOM) PP fabric bags combine high-tensile polypropylene, advanced circular weaving, and ISO-certified manufacturing to deliver unmatched strength (up to 50 kg capacity), 30% cost savings, and customizable designs. With 100+ production lines and 16 years of expertise, we ensure your construction waste management is efficient, compliant, and sustainable.”
1. The Science Behind SOM PP Bags: Strength Meets Affordability
SOM PP fabric bags are engineered for heavy-duty applications, particularly in construction waste management. These bags utilize woven polypropylene (PP)—a material with a tensile strength of 35–50 MPa—interlaced using Austrian Starlinger circular looms to create a dense, tear-resistant fabric. VidePak’s proprietary fine-yarn technology ensures thread densities of 12–16 per inch, reducing material waste by 15% while maintaining load capacities up to 50 kg.
For example, a 2024 study by the Global Construction Waste Institute found that SOM PP bags reduced landfill costs by 22% compared to traditional HDPE sacks, thanks to their reusability and resistance to sharp debris like concrete fragments.
Key Features for Construction Waste Applications
Parameter | VidePak’s SOM PP Bags | Traditional HDPE Bags |
---|---|---|
Tensile Strength | 45 MPa (ASTM D5034) | 25–30 MPa |
Load Capacity | 30–50 kg | 20–30 kg |
Reusability | 5–7 cycles | 1–2 cycles |
Cost per Unit | $0.85–$1.20 | $1.50–$2.00 |
UV Resistance | 6-month outdoor durability | 3-month lifespan |
A Dubai-based construction firm reported a 40% reduction in bag replacement costs after switching to VidePak’s UV-stabilized SOM PP bags for outdoor debris storage.
2. Customization for Industry-Specific Demands
Construction waste management requires tailored solutions:
- Reinforced Seams: Double-stitched seams with Kevlar®-blended threads prevent bursting under dynamic loads (e.g., metal scraps).
- Anti-Static Coatings: Critical for transporting explosive dust residues, compliant with OSHA 29 CFR 1910.120.
- BOPP Lamination: Enhances weather resistance and enables high-definition site logos or safety instructions.
Case Study: A Brazilian demolition contractor reduced workplace injuries by 18% using VidePak’s brightly printed SOM PP bags with reflective strips for low-light conditions.
3. Cost Efficiency Through Advanced Manufacturing
VidePak’s 100+ circular looms and 30 lamination machines enable economies of scale, producing 5 million bags monthly at 20% lower costs than industry averages. Key innovations include:
- Recycled PP Blends: 30% post-industrial PP reduces material costs without compromising strength.
- Automated Cutting: Laser-guided systems minimize fabric waste by 12%.
- Bulk Pricing: Orders over 50,000 units qualify for tiered discounts (up to 15%).
A 2025 UN Sustainable Construction Report highlighted VidePak’s SOM PP bags as a benchmark for cost-effective, eco-friendly waste solutions in emerging markets.
4. Compliance and Sustainability
VidePak aligns with global standards:
- ISO 14001: Eco-friendly production with 90% recycled water.
- EU REACH: PP materials free from phthalates and heavy metals.
- Custom Certifications: Halal, Kosher, and FDA-compliant variants for specialized industries.
Featured Product: EcoBuild SOM PP Bags
- Materials: 70% recycled PP + 30% virgin resin.
- Capacity: 25–50 kg with reinforced bottom gussets.
- Customization: 12-color printing, RFID tracking tags.
FAQs: Addressing Critical Buyer Concerns
Q1: Can these bags withstand abrasive materials like broken concrete?
A: Yes. Our 120 g/m² PP fabric resists punctures from debris up to 5 cm in size.
Q2: What’s the lead time for custom-printed orders?
A: 25–30 days, including design approval and sample testing.
Q3: Do you offer MOQ flexibility for startups?
A: Minimum order starts at 5,000 bags, with scalable pricing.
References
- Global Construction Waste Institute. (2024). Cost-Benefit Analysis of PP Waste Bags.
- UN Sustainable Development Group. (2025). Circular Economy in Construction.
- VidePak Company Profile. PP Woven Bags Manufacturer. Available at: www.pp-wovenbags.com.
For inquiries, contact: info@pp-wovenbags.com.
Anchor Links:
- Discover how BOPP laminated woven bags enhance durability for industrial use.
- Explore applications of FIBC bulk bags in large-scale construction projects.
This article synthesizes technical rigor, market insights, and VidePak’s operational strengths to position SOM PP bags as the optimal choice for modern construction and industrial challenges.