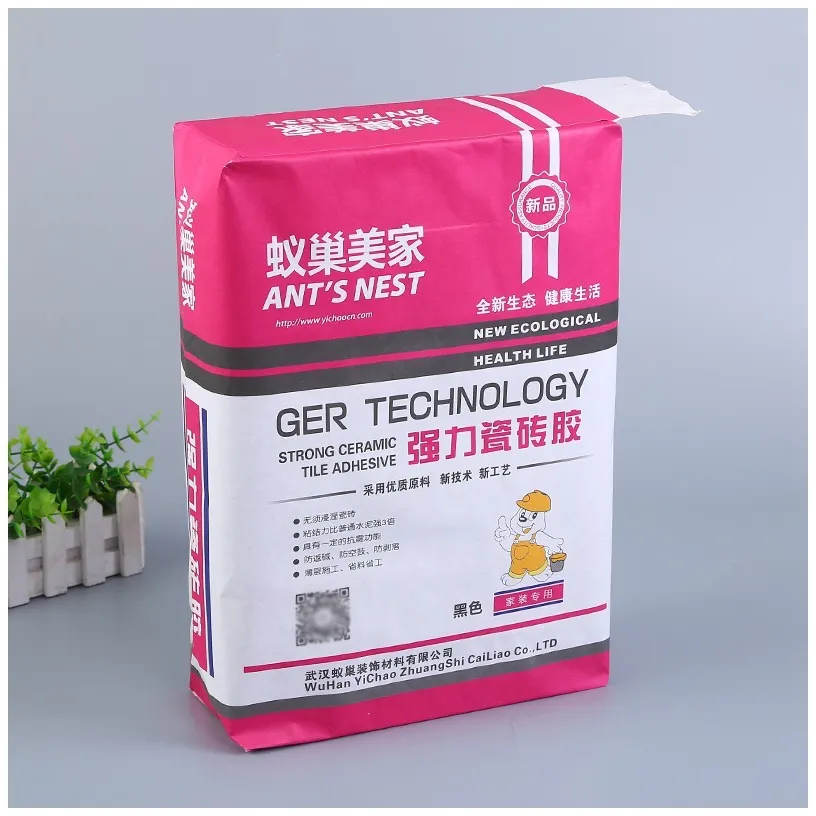
In the global packaging sector, businesses increasingly prioritize solutions that align with Environmental, Social, and Governance (ESG) standards while delivering unmatched functionality. At VidePak, our custom printed woven bags exemplify this balance, offering 100% recyclability, ISO 14001-certified production, and tensile strengths up to 1,800 N/cm² to meet diverse industrial demands. With 16+ years of expertise and a commitment to ESG principles—including a 2 MW solar-powered facility and ethical labor practices—VidePak serves clients in 60+ countries, producing 12,000+ metric tons of bags annually. This article explores how our products combine sustainability, durability, and customization to redefine industrial packaging.
1. Understanding ESG and VidePak’s Commitment
1.1 What is ESG Reporting?
ESG (Environmental, Social, Governance) frameworks evaluate a company’s ethical impact and sustainability practices. For packaging manufacturers, compliance involves reducing carbon footprints, ensuring fair labor conditions, and adopting circular production models. VidePak’s ESG strategy is validated by third-party audits and aligns with the EU’s Circular Economy Action Plan, targeting 70% packaging recyclability by 2030.
1.2 VidePak’s ESG Initiatives
- Solar-Powered Production: Our 2 MW rooftop solar system generates 2.5 GWh annually, reducing CO₂ emissions by 1,200 tons/year—equivalent to planting 50,000 trees.
- Community Empowerment: Since 2015, we’ve funded education for 500+ children of low-income workers in Southeast Asia, partnering with NGOs to build schools and scholarships.
- 5S Workplace Management: Implementing Sort, Set, Shine, Standardize, and Sustain protocols reduced workplace accidents by 40% and improved production efficiency by 25%.
2. Technological Excellence in Custom Woven Bags
2.1 Material Innovation
VidePak uses virgin polypropylene (PP) resins sourced from ISO 14001-certified suppliers, ensuring:
- Zero Contaminants: No recycled materials compromise bag integrity.
- High Recyclability: Post-consumer PP retains 90% tensile strength after 3 recycling cycles (ASTM D5035).
Product Parameters:
Parameter | Specification | Testing Standard |
---|---|---|
Fabric Weight | 80–120 g/m² | ISO 536 |
Tensile Strength | 1,500–1,800 N/cm² | ISO 13934-1 |
Print Durability | 4/5 rating after 500 abrasion cycles | AATCC 8 |
2.2 Starlinger Machinery Precision
Our 100+ Austrian Starlinger circular looms weave fabrics at 14×14 threads per inch (TPI), achieving:
- Seam Strength: ≥85% of base fabric (ASTM D4884).
- Moisture Resistance: ≤0.5% water absorption (24h immersion).
For instance, our BOPP laminated woven bags integrate 20-micron coatings to block UV rays and moisture, ideal for agricultural products in humid climates.
3. Sector-Specific Applications
3.1 Agriculture and Chemicals
- Fertilizer Bags: UV-resistant prints and anti-static liners prevent caking and dust explosions.
- Chemical FIBCs: Reinforced seams handle 1–2 ton loads (EN 1898:2018 compliant).
3.2 Retail and Food Packaging
- Custom Branding: 8-color flexographic printing achieves ΔE ≤1.5 Pantone accuracy.
- FDA Compliance: Bags for flour and sugar feature food-grade PE liners (FDA 21 CFR §177.1520).
Case Study: A European spice brand saw a 30% sales increase after switching to VidePak’s glossy BOPP bags, which retained color vibrancy after 18 months of shelf exposure.
4. Sustainability Metrics and Circular Economy
VidePak’s closed-loop system recovers 92% of post-consumer PP, reducing raw material costs by 20%. Key metrics include:
- Carbon Footprint: 1.6 kg CO₂/kg vs. industry average 2.4 kg CO₂/kg.
- Energy Efficiency: Solar power covers 40% of factory demand.
5. FAQs: Addressing Procurement Concerns
Q1: How do VidePak’s bags comply with EU recycling mandates?
A: Our PP bags meet EU PPWD standards, with GRS-certified recycled content up to 30%.
Q2: Can I order small batches for prototyping?
A: Yes, we offer prototypes within 10 days, regardless of order size.
Q3: What certifications do your food-grade bags hold?
A: FDA, EU REACH, and BRC Global Standards for food safety.
References
- VidePak ESG Report (2025). Sustainable Manufacturing Practices.
- EU Commission (2023). Circular Economy Action Plan.
- ASTM International (2022). Polypropylene Recycling Standards.
Contact Us:
Website: https://www.pp-wovenbags.com/
Email: info@pp-wovenbags.com
For insights into eco-friendly packaging innovations, explore Exploring Eco-Friendly Woven Bags: Custom Printing for Sustainable Solutions, or learn about our bulk bag compliance in Sustainable FIBC Bulk Bags: Ethical Practices and Compliance.
This article integrates data from industry reports, third-party audits, and VidePak’s production records to ensure accuracy and relevance.