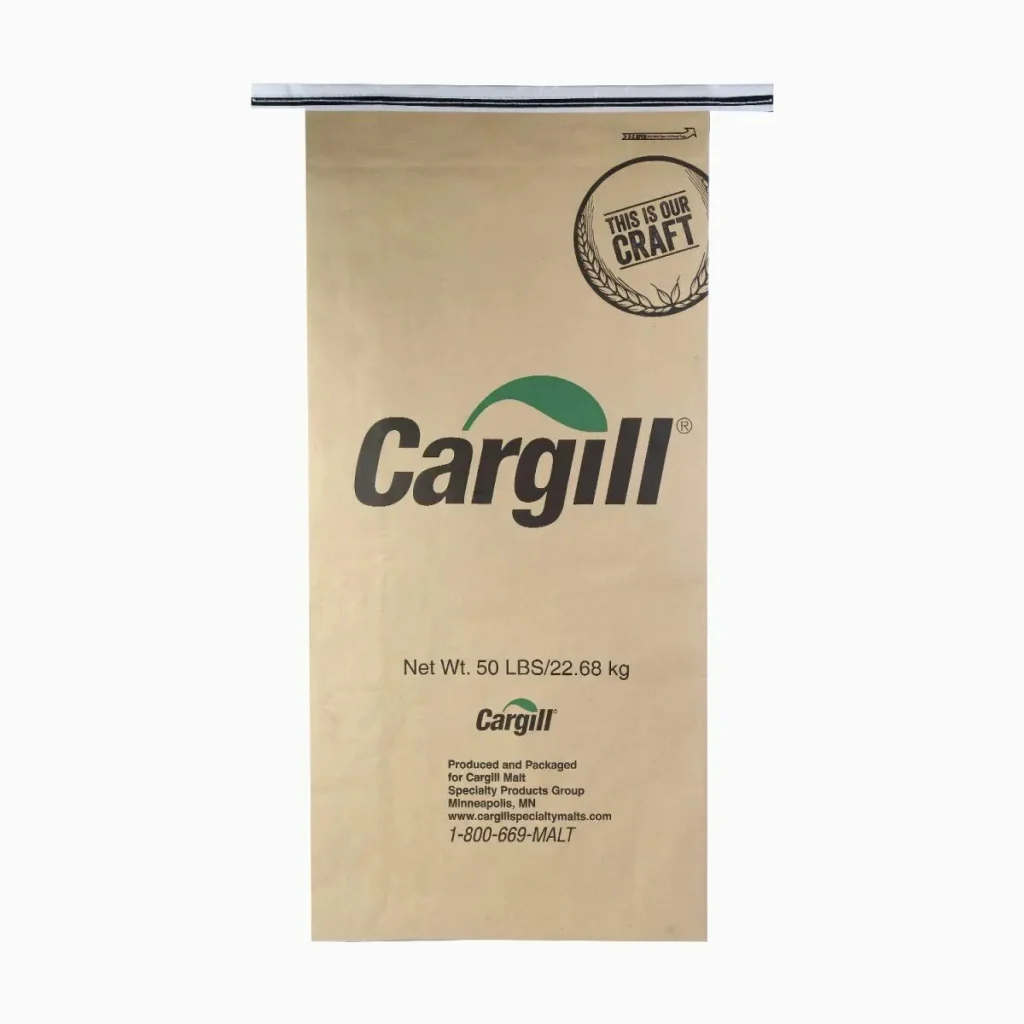
Woven bags are becoming increasingly popular in packaging for a wide variety of industries due to their durability, cost-effectiveness, and customizable nature. When it comes to enhancing the visual appeal and functionality of woven bags, the ability to print on them opens up a wealth of opportunities. Custom printed woven bags (also referred to as custom printed woven sacks) allow companies to create a unique identity, improve product visibility, and communicate their branding message directly on the packaging itself. This blog explores common printing techniques used on woven bags, along with various finishes available to elevate their appearance.
Custom Printed Woven Bags: Tailoring Design and Functionality
Custom printed woven bags, especially those made of polypropylene (PP) or biaxially oriented polypropylene (BOPP), offer versatile printing options and surface finishes to meet specific branding and functional needs. Whether for retail, construction, or agricultural applications, these bags can be tailored with custom logos, branding, and other design elements.
Common Printing Techniques for Custom Printed Woven Bags
- Flexographic Printing:
Flexographic printing is one of the most widely used techniques for printed woven bags. It is a high-speed, cost-effective method that uses flexible relief plates to transfer ink onto the surface of the woven bag. This process is ideal for large-volume orders as it ensures consistency and quality across multiple prints. - Gravure Printing:
Gravure printing, also known as intaglio printing, uses a rotary press with engraved cylinders to transfer ink onto the surface. While more expensive than flexographic printing, gravure printing offers higher-quality results, especially for detailed designs. It’s commonly used for printed BOPP woven bags that require high-quality, photo-realistic images and rich colors. - Screen Printing:
Screen printing is often used for printing on woven fabrics, including polypropylene (PP) woven bags. In this process, a mesh screen is used to apply ink onto the bag’s surface. This method is perfect for bold designs, and it’s especially useful when limited colors are required. - Digital Printing:
Digital printing involves the direct application of digital designs onto woven bags using specialized inkjet printers. This is an ideal choice for small runs or highly intricate designs that may require detailed color gradients or variable data. As digital printing doesn’t require plates, it allows for more flexibility and lower setup costs.
Each of these methods has its strengths and applications. Flexographic and gravure printing are better suited for large-volume orders, while screen and digital printing are ideal for smaller runs or complex designs.
Aesthetic and Functional Finishes: Elevating the Appearance of Printed Woven Bags
In addition to the printing techniques, the finish applied to custom printed woven bags can significantly affect both the visual appeal and the performance of the bags. Let’s explore a few popular finishes.
Matte and Gloss Lamination Finishes
- Matte Lamination: Matte lamination is a popular choice for businesses looking to create a subtle, elegant look. This finish gives the bag a smooth, non-reflective surface while preserving the vibrancy of the printed colors. It is often used for premium product packaging and luxury items, as it imparts a sophisticated and high-end appearance to the woven bags.
- Gloss Lamination: For those looking to enhance color depth and vibrancy, gloss lamination is an excellent option. The shiny, reflective surface not only makes the printed design stand out but also adds an extra layer of protection against dirt and moisture. Printed BOPP woven bags with gloss lamination are commonly used for food packaging, where visibility and appeal are essential.
Pearl and Transparent Finishes
- Pearl Lamination: Pearl lamination offers a subtle shimmer that gives printed woven bags a pearlescent finish. This unique effect catches the light and adds a touch of elegance to the packaging. It’s often used for high-end products or special promotions.
- Transparent Woven Bags: One of the most innovative trends in the woven bag market is the use of transparent woven bags. These bags are made with a transparent polypropylene material, allowing the contents to be seen while still offering the strength and durability of a woven bag. Transparent woven bags are ideal for showcasing products, especially in retail packaging, as they allow consumers to see exactly what they are purchasing without opening the packaging.
Specialized Coatings
- UV Coating: UV coating is a protective finish applied to the surface of printed woven bags. It not only enhances the durability of the print but also helps protect the bag from fading due to exposure to sunlight. This is especially useful for outdoor packaging applications such as construction materials or agricultural products.
- Anti-slip Coating: Some custom printed woven sacks are designed with an anti-slip coating. This coating prevents the bags from sliding during transportation and handling, making them safer and easier to stack.
Table: Key Characteristics of Custom Printed Woven Bags
Feature | Flexographic Printing | Gravure Printing | Screen Printing | Digital Printing |
---|---|---|---|---|
Ink Type | Water-based / Solvent-based | Solvent-based | Solvent-based / UV | Water-based / UV |
Cost | Low (High Volume) | High (High Quality) | Moderate | High (Small Run / Complex) |
Design Detail | Moderate | High | Moderate | Very High |
Best For | Large-Scale Production | Detailed, High-Quality Designs | Bold, Simple Designs | Detailed, High-Resolution |
Production Speed | Very Fast | Fast | Moderate | Moderate |
Unique Styles of Custom Printed Woven Bags: Enhancing Aesthetic Appeal
Beyond the printing techniques, the overall design and finish of woven bags can be customized in various ways. Some of the most popular styles include:
- Custom Printed BOPP Woven Bags: These bags are made by laminating a layer of BOPP film onto woven polypropylene fabric. The result is a smooth surface perfect for high-quality printing, which is essential for brands looking for vibrant, eye-catching designs. BOPP bags are often used in food packaging, agricultural products, and retail.
- Jumbo Woven Bags: Jumbo bags, or FIBC (Flexible Intermediate Bulk Containers), are used for bulk packaging and storage. While their size and strength make them suitable for large-scale applications, these bags can also be customized with printed designs to reinforce brand identity. Typically, jumbo bags are used for transporting industrial goods, chemicals, or food grains.
- Kraft Paper-Laminated Woven Bags: Combining the durability of woven fabric with the classic appeal of kraft paper, these bags are ideal for products requiring a rustic or eco-friendly appearance. The kraft paper can be printed with custom designs, making it a versatile choice for both high-end retail and agricultural uses.
Conclusion
Custom printed woven bags and sacks are versatile packaging solutions that offer both functionality and brand visibility. The printing techniques used, such as flexographic, gravure, screen, and digital printing, allow for the creation of unique, eye-catching designs, while the finishes like matte, gloss, and pearl lamination further enhance the aesthetic appeal. By combining high-quality prints with innovative finishes, businesses can create woven bags that not only serve as a practical packaging solution but also help promote their brand in a competitive market. For further insight into these solutions, check out the following links: