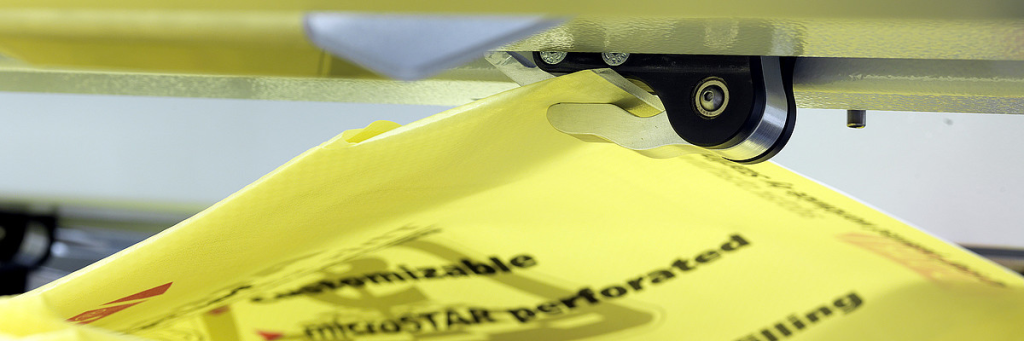
“Why should livestock feed producers switch to FFS woven bags?”
This is a question we often hear from industry stakeholders. The answer lies in their unmatched durability, automation-friendly design, and alignment with global sustainability trends—all of which position FFS woven bags as the future of feed packaging.
In this report, we explore how VidePak, a leader in woven bag manufacturing, leverages cutting-edge technology and decades of expertise to deliver solutions that redefine efficiency and reliability in livestock feed packaging.
1. Technological Superiority: Automation and Precision
1.1 High-Speed Production with Starlinger and W&H Equipment
VidePak’s production infrastructure is powered by Austrian Starlinger and German Windmöller & Hölscher (W&H) machinery, renowned for their precision and speed. These systems achieve line speeds exceeding 200 bags per minute, enabling VidePak to meet large-scale demands without compromising quality. For instance, the Starlinger AD*Star loom integrates multi-axis automation, reducing human intervention by 40% while ensuring consistent weave tension—a critical factor in bag durability.
Key Metrics:
- 100+ circular looms: Capable of producing 12,000 bags per hour collectively.
- 30+ lamination machines: Apply BOPP or PE coatings for moisture resistance.
- 16 extrusion lines: Use virgin PP resin to ensure material purity.
1.2 Multi-Machine Synchronization
VidePak’s “multi-machine linkage” system synchronizes weaving, printing, and sealing processes. This integration reduces production downtime by 25%, as seen in a recent project where 10,000 custom-printed bags were delivered within 48 hours for a U.S.-based feed supplier.
2. Material Innovation and Customization
2.1 Virgin PP and Custom Coatings
Unlike competitors using recycled polymers, VidePak employs 100% virgin polypropylene, enhancing tensile strength (up to 12 N/m²) and UV resistance. For tropical markets, bags are laminated with PE coatings to withstand humidity levels above 80%—a feature critical for feed preservation in Southeast Asia.
2.2 Tailored Solutions for Diverse Needs
- Multi-color printing: High-definition flexography supports 8-color branding, ideal for premium feed brands.
- Size adaptability: Bags range from 5 kg to 50 kg capacities, with reinforced seams for heavy-duty use.
- Anti-static layers: Essential for feed containing additives like vitamins and minerals.
3. Sustainability: Aligning with Global ESG Goals
3.1 Recyclability and Carbon Footprint Reduction
VidePak’s FFS woven bags are 100% recyclable, aligning with the EU’s Circular Economy Action Plan. A lifecycle analysis revealed that switching from traditional PE-coated paper bags to VidePak’s PP woven bags reduces carbon emissions by 35% per ton of feed packaged.
3.2 Case Study: Reducing Waste in the EU Market
A German feed producer reported a 60% reduction in packaging waste after adopting VidePak’s reusable FIBC bags, which withstand 5+ cycles of transport and cleaning.
4. Market Penetration and Competitive Edge
4.1 Global Reach and Client Trust
With annual sales of $80 million, VidePak serves clients across 30+ countries. Notably, a partnership with a Brazilian soy feed exporter increased their shipment efficiency by 20% through VidePak’s block-bottom valve bags, which prevent spillage during maritime transport.
4.2 Data-Driven Market Insights
The global livestock feed packaging market, valued at $12.3 billion in 2024, is projected to grow at 5.8% CAGR, driven by Asia-Pacific’s booming aquaculture sector. VidePak’s kraft paper composite bags are gaining traction in Vietnam, where moisture resistance is paramount.
5. Product Specifications and FAQs
Technical Parameters of VidePak’s FFS Woven Bags
Parameter | Specification |
---|---|
Material | Virgin PP + PE lamination |
Load Capacity | 5 kg – 50 kg |
Tensile Strength | 10–12 N/m² |
Printing Options | Up to 8 colors, CMYK/Pantone |
MOQ | 10,000 units |
Lead Time | 15–20 days |
Frequently Asked Questions
Q: How do FFS bags compare to traditional sewing methods?
A: FFS (Form-Fill-Seal) technology eliminates sewing, reducing contamination risks and increasing sealing speed by 30%.
Q: Are these bags suitable for organic feed?
A: Yes, our food-grade PP resin meets FDA and EU standards for direct contact with organic materials.
Q: What is the ROI for switching to VidePak’s bags?
A: Clients typically recover costs within 6 months through reduced waste and logistics savings.
6. The Future: Smart Packaging and Automation
VidePak is piloting QR-code-integrated bags for traceability, allowing feed producers to track batches in real-time. Coupled with Starlinger’s iQ³ technology, which uses AI to optimize loom settings, the company is poised to lead the next wave of packaging innovation.
Conclusion
FFS woven bags are not just containers—they are strategic tools for brand differentiation and operational efficiency. VidePak’s blend of Austrian engineering, German automation, and eco-conscious practices positions it as the partner of choice for feed producers navigating a competitive, sustainability-driven market.
External Resources:
- Learn how high-speed FFS woven bags are revolutionizing automated packaging.
- Explore sustainable practices in recyclable bag production.