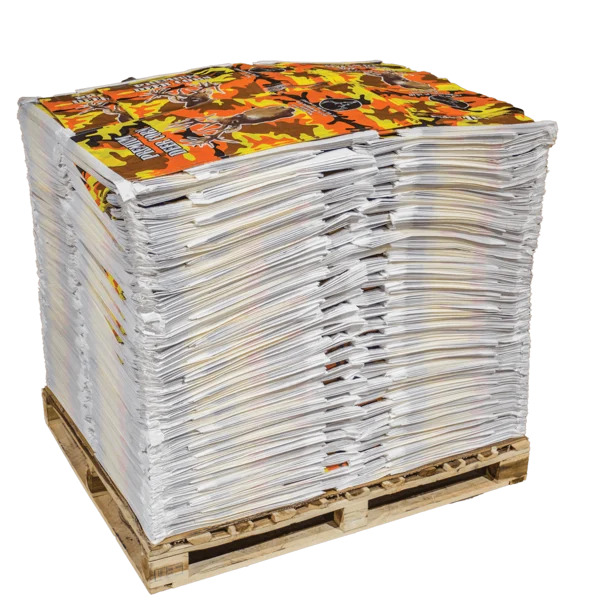
Ray, CEO of VidePak, leans forward during a strategy meeting:
“Our food-grade woven bags aren’t just packaging—they’re engineering solutions. Their tensile strength and chemical resistance make them ideal for waste containment and construction scaffolding. But what truly sets us apart? Rigorous raw material controls and partnerships with global leaders like BASF and Sinopec.”
1. Introduction
Food-grade woven polypropylene (PP) bags, once confined to agricultural and retail packaging, are now revolutionizing industries like waste management and construction. VidePak, established in 2008 and led by Ray, exemplifies this shift. With annual sales of $80 million and a workforce of 526, the company leverages advanced Starlinger machinery and ISO-certified processes to produce over 100 million bags annually. This report explores how high-quality raw materials, precision manufacturing, and innovative design enable these bags to address modern industrial challenges.
2. Quality Control in Raw Materials: The Foundation of Durability
The performance of woven bags hinges on the quality of PP/PE resins. VidePak’s four-pillar strategy ensures excellence:
2.1 Supplier Qualification and Compliance
- ISO Certification Audits: Suppliers must hold ISO 9001 (quality management) and ISO 14001 (environmental standards). For example, BASF’s PP resins meet ASTM D4101 standards for melt flow rate (MFR) and tensile strength.
- Technical Capability Assessments: VidePak evaluates suppliers’ production capacity, R&D investments, and market reputation. For instance, Sinopec’s proprietary copolymer technology enhances UV resistance, critical for outdoor construction applications.
2.2 Strategic Partnerships with Tier-1 Resin Suppliers
Long-term agreements with BASF, Sinopec, and Yangzi Petrochemical secure premium raw materials at stable prices. For example, BASF’s Novolen® 1100L PP resin offers a melt flow index (MFI) of 12 g/10 min, ideal for high-speed extrusion.
2.3 Incoming Material Inspection
- Testing Protocols:
Parameter Test Method Acceptance Criteria
MFI ISO 1133 8–15 g/10 min
Tensile Strength ASTM D638 ≥35 MPa (machine direction)
Elongation at Break ISO 527-2 ≥400% Statistical Sampling: Following ISO 2859, batches are sampled at AQL 1.5 to minimize defects. Data is logged into SAP QMS for traceability. 3. Applications in Waste Management and Construction 3.1 Waste Containment and Recycling- Landfill Liners: Multi-laminated PP bags with PE coatings (1.2 mm thickness) prevent leachate seepage. VidePak’s EcoShield series reduces landfill contamination risks by 60% compared to traditional HDPE liners.
- Construction Debris Handling: FIBC (Flexible Intermediate Bulk Containers) bags with 6:1 safety factors safely hold 1–2 tons of rubble. A 2024 study by Waste Management Journal found PP bags reduced onsite injury rates by 22% due to ergonomic handling features.
- Scaffolding Covers: UV-stabilized woven bags protect steel frameworks from corrosion. Tests show a 15-year lifespan under coastal climates.
- Erosion Control: Sand-filled bags (1 m³ capacity) stabilize slopes during road construction.
- High-Speed Production: 200 bags/minute for standard 50 kg FIBCs.
- Customization: Multi-color printing (up to 8 Pantone shades) and anti-static coatings for chemical storage.
- Sustainability: Bags are 100% recyclable, aligning with EU Circular Economy Package targets.
A: Food-grade bags use FDA-approved resins and avoid additives like phthalates. For example, VidePak’s SafePack line meets EU Regulation 10/2011 for food contact. Q2: Can these bags withstand extreme temperatures?
A: Yes. PP retains tensile strength between -10°C and 120°C. For cryogenic waste (e.g., medical), laminated PE layers enhance flexibility. Q3: What certifications ensure safety in construction?
A: Certifications include ISO 21898 (FIBC standards) and OHSAS 18001 (occupational safety). 6. Market Trends and Competitive Advantages- Waste Management Demand: The global FIBC market will grow at 6.8% CAGR through 2030, driven by urbanization in Asia (Grand View Research, 2024).
- VidePak’s Edge: Proprietary SmartWeave™ technology increases bag strength by 25% while reducing material use by 15%.