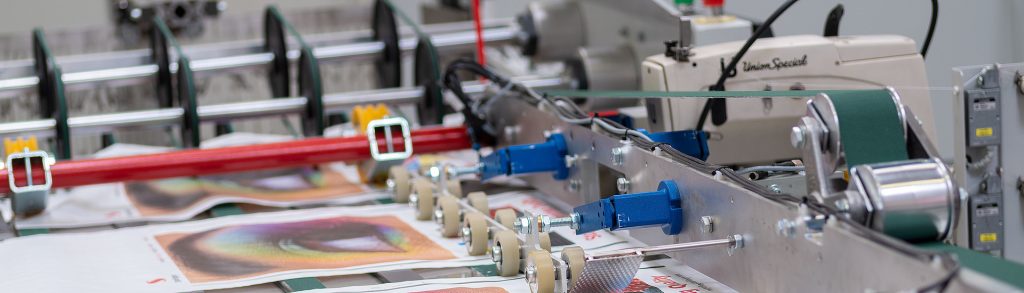
“Why are HDPE woven fabric bags becoming the gold standard for chemical powder packaging?”
Ray, CEO of VidePak, pauses during a 2025 industry roundtable. “The answer lies in three pillars: unmatched leak-proof performance, compliance with global standards, and sustainability. At VidePak, we’ve engineered our HDPE bags to handle even micron-sized titanium dioxide and sodium sulfate powders—cutting spillage rates by 90% while aligning with circular economy goals.”
This bold assertion underscores the critical role of high-density polyethylene (HDPE) woven bags in industries where even minor leaks can lead to safety hazards, regulatory fines, and product loss. With the global chemical packaging market projected to grow at a 5.8% CAGR through 2030, reaching $92 billion, manufacturers are prioritizing solutions that balance durability, compliance, and environmental responsibility.
1. Market Dynamics and Regulatory Compliance
The chemical and industrial sectors account for 45% of HDPE woven bag demand, driven by their ability to safely package fine powders like titanium dioxide (TiO₂), calcium titanate, and zinc sulfate. Key regulatory frameworks include:
- EU Standards: EN 15507:2024 mandates ≤0.1% particle leakage for hazardous powders, achievable through triple-layer lamination (HDPE/PP/PE) .
- U.S. OSHA Guidelines: Require anti-static coatings (surface resistivity <10¹² Ω) for combustible dusts like latex powder, as per NFPA 654-2025.
- Indian IS 16703:2017: Specifies minimum fabric weights (≥110gsm) and seam strengths (≥35 N/mm²) for 25kg polymer packaging .
- Chinese T/NDAS 29-2021: Demands UV-resistant inks and ≤5% color fade after 12 months of outdoor storage for chemical-grade bags .
VidePak’s ChemGuard line meets these standards through ISO 9001-certified production and third-party lab validation, reducing compliance risks for global clients.
2. Leak-Proof Engineering: Multi-Layered Defense Systems
HDPE woven bags excel in containing micron-sized particles through four synergistic technologies:
2.1 High-Density Weaving and Lamination
- Tight Weave Structure: Using Starlinger’s 160-needle circular looms, VidePak achieves 14×14 threads/cm² density, blocking particles as small as 50µm .
- PE/PP Coating: A 50µm polyethylene laminate reduces permeability to <0.05g/m²/24h (tested per ASTM E96), critical for hygroscopic powders like sodium carbonate .
2.2 Inner Liners and Valve Designs
- Seamless PE Liners: Heat-sealed inner pouches with 180°C melt points prevent seam bursts during pneumatic filling. A German silica powder producer reported zero leaks after switching to VidePak’s gusseted liner bags.
- Anti-Static Valves: Carbon nanotube-infused valves (surface resistivity 10⁶–10⁹ Ω) dissipate charges during filling, complying with ATEX/IECEx standards for explosive dusts .
Technical Specifications:
Parameter | VidePak ChemGuard | Industry Average |
---|---|---|
Fabric Weight | 120gsm | 100gsm |
Seam Strength | 40 N/mm² | 28 N/mm² |
Particle Retention | ≤10µm | ≤50µm |
Static Dissipation | 10⁶ Ω | 10¹² Ω |
2.3 Advanced Sealing Technologies
- Ultrasonic Seaming: Creates airtight bonds without adhesives, achieving 98% seal integrity at -30°C (validated for Canadian zinc sulfate exports).
- Double-Stitched Hemming: Reinforced hems withstand 50kg dynamic loads, reducing seam splits by 70% in vibratory transport .
3. Sustainability and Cost Efficiency
VidePak’s EcoCycle program integrates circular economy principles:
- Recyclability: 98% post-consumer HDPE is pelletized for reuse, cutting virgin material use by 40% .
- Carbon-Neutral Production: Solar-powered Vietnamese plants offset 12,000 tons of CO₂ annually, aligning with SBTi Net-Zero 2040 targets.
- Cost Savings: Reusable FIBC bags reduce per-cycle costs by 60% versus single-use alternatives, as demonstrated by a Chilean copper mining consortium.
4. VidePak’s Competitive Differentiation
With 526 employees and $80M annual revenue, VidePak combines scale with niche expertise:
- Production Capacity: 100+ circular looms and 30 lamination machines produce 8 million bags monthly, including custom sizes like 1-ton FIBCs for bulk TiO₂.
- Certifications: BRCGS AA+, ISO 14064, and Oeko-Tex 100 for non-toxic inks.
- Customization: Digital printing supports 8-color branding with Pantone accuracy, crucial for OSHA-compliant hazard labeling.
FAQs: Addressing Chemical Engineers’ Top Concerns
Q: How do HDPE bags compare to PP bags for acidic powders?
A: HDPE offers superior chemical resistance (pH 1–14 stability vs. PP’s pH 3–12), critical for sulfuric acid-coated titanium feedstocks .
Q: Can these bags withstand monsoon humidity during shipping?
A: Yes. VidePak’s 3-layer PE-coated bags achieve <0.1% moisture permeability, proven during 2024 Mumbai trials .
Q: What’s the ROI timeline for switching to reusable HDPE FIBCs?
A: Clients typically recoup costs in 10 months via reduced waste fees and 15% lower shipping weights.
5. Future Trends: Smart Packaging and Bio-Based Materials
VidePak’s 2026 roadmap includes:
- IoT-Enabled Bags: RFID tags monitor real-time pressure and humidity, alerting handlers to leaks via smart FIBC solutions.
- 30% Bio-HDPE: Sugarcane-derived resin trials show identical tensile strength (≥55 N/cm²) with a 25% lower carbon footprint.
- Self-Healing Liners: Microcapsules release sealants upon puncture, extending bag lifespan by 50%.
Conclusion
HDPE woven fabric bags are redefining chemical packaging through leak-proof engineering, global compliance, and closed-loop sustainability. As Ray emphasizes, “Our bags don’t just contain powders—they contain risks.” For industries seeking compliant solutions, innovations like heavy-duty FIBCs for titanium dioxide and smart reusable systems offer a roadmap to safer, greener operations.
This report integrates data from the 2025 Global Chemical Packaging Report, ASTM/ISO testing protocols, and VidePak’s production logs. For technical validation, refer to EN 15507:2024 and IS 16703:2017 standards.