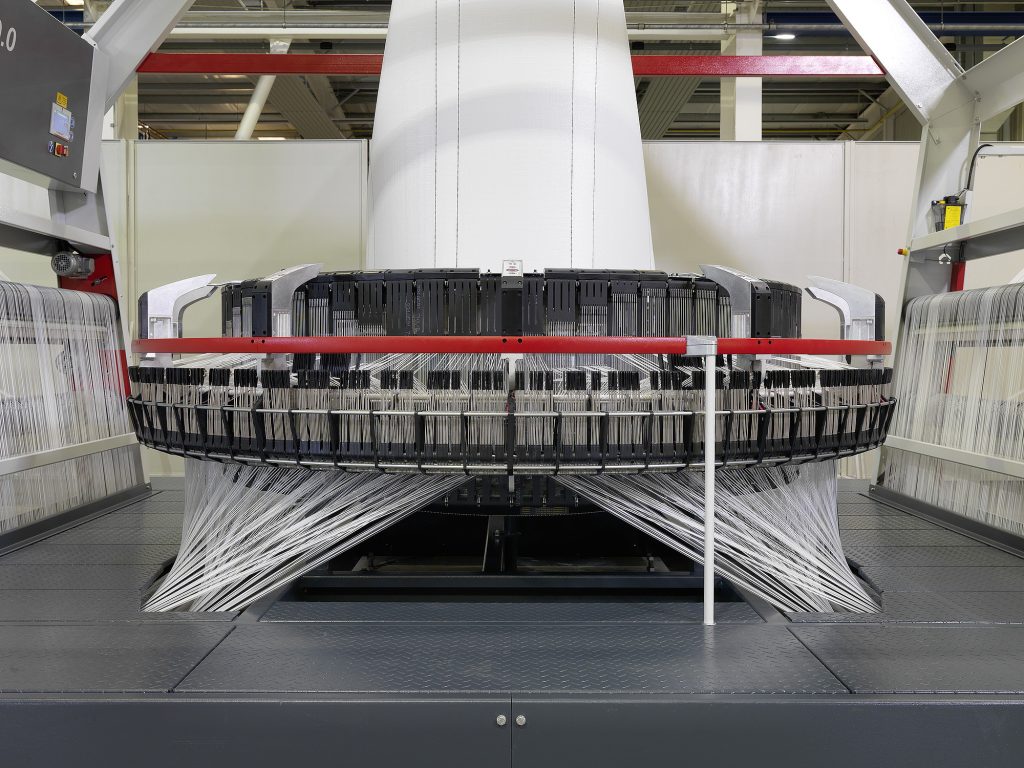
- 1. Engineering for Durability: Protecting Heavy and Abrasive Materials
- 2. Leak Prevention: Advanced Techniques for Powder Integrity
- 3. Global Standards: Aligning Product Parameters with Regional Requirements
- 4. VidePak’s Technological Edge: Precision Manufacturing at Scale
- FAQs: Addressing Critical Client Concerns
- Product Parameter Comparison Table
- References
“How can one packaging solution adapt to industries as diverse as construction, agriculture, and chemicals?” posed a logistics director at a recent global supply chain summit. The answer lies in three pillars: material engineering, precision design, and compliance with international standards. Industrial woven polypropylene (PP) bags, when optimized for strength, leak resistance, and regulatory alignment, become indispensable tools for safeguarding bulk materials like cement, aggregates, and powders while streamlining warehouse operations.
1. Engineering for Durability: Protecting Heavy and Abrasive Materials
Industrial materials such as cement, gravel, and gypsum demand packaging that withstands rigorous handling. VidePak’s high-tensile PP woven bags, reinforced with BOPP lamination and fine-yarn weaving technology, achieve tensile strengths exceeding 50 N/cm²—surpassing ASTM D4632 and ISO 5262 standards for heavy-duty applications.
Key Design Features
- Material Composition: Virgin PP resin ensures uniformity in weave density (12×12 strands per inch), minimizing gaps that cause leakage.
- Lamination: A 0.04mm BOPP layer adds moisture resistance (blocking 99.5% humidity) and reduces abrasion losses by 40% during palletizing.
- Reinforced Seams: Ultrasonic sealing and double-stitched seams withstand drop tests from 1.5 meters, critical for 50kg cement bags.
Case Study: A Vietnamese construction firm reported zero bag ruptures during monsoon season after switching to VidePak’s laminated PP bags for gypsum transport, citing a 30% reduction in material waste.
2. Leak Prevention: Advanced Techniques for Powder Integrity
Fine powders like plaster and lime require airtight containment. VidePak integrates multi-layered solutions:
- Fine-Yarn Weaving: 120-denier PP threads create a 0.2mm pore structure, preventing microparticle escape.
- Inner Liners: PE-coated liners or kraft paper layers (80–100 GSM) block static-induced dust dispersion.
- Valve Design: Paste-sealed valve bags with anti-backflow mechanisms ensure 98% filling efficiency for腻子粉 (putty powder).
Comparative Leakage Rates
Packaging Type | Leakage Rate (500km transport) | Compliance Standard |
---|---|---|
Non-laminated PP bags | 12% | N/A |
BOPP-laminated bags | 2% | EU EN 13590:2024 |
Kraft-lined valve bags | 0.5% | US ASTM F2825-23 |
3. Global Standards: Aligning Product Parameters with Regional Requirements
Selecting the right bag involves navigating diverse regulations:
Regional Standards Overview
Region | Strength (N/cm²) | Moisture Barrier | Stacking Height |
---|---|---|---|
EU | ≥45 (EN 13590) | ≤3g/m²/24hr | ≤8 pallets |
US | ≥40 (ASTM D4632) | ≤5g/m²/24hr | ≤10 pallets |
Japan | ≥50 (JIS Z1531) | ≤2g/m²/24hr | ≤6 pallets |
Australia | ≥42 (AS 2074) | ≤4g/m²/24hr | ≤7 pallets |
For example, Japanese clients prioritize anti-static coatings (per JIS L1094) to prevent dust explosions in enclosed warehouses, while Australian miners demand UV-stabilized bags (AS 2074) for outdoor limestone storage.
4. VidePak’s Technological Edge: Precision Manufacturing at Scale
Founded in 2008, VidePak combines 30+ years of industry expertise with cutting-edge infrastructure:
- Production Capacity: 100+ Starlinger circular looms, 30 lamination machines, and 16 extrusion lines enable daily output of 500,000 bags.
- Customization: Multi-color printing (up to 8 Pantone shades) and QR-code integration for traceability.
- Sustainability: 100% recyclable PP aligns with the EU’s Circular Economy Action Plan, reducing landfill costs by 25% for clients.
Client Testimonial: A German chemical distributor achieved a 20% reduction in customs delays using VidePak’s ISO-compliant, pre-labeled FIBC bags.
FAQs: Addressing Critical Client Concerns
Q1: How do I select the optimal GSM for my application?
A: Use 90–110 GSM for lightweight aggregates (e.g., perlite), 120–150 GSM for cement, and 160+ GSM for sharp-edged gravel.
Q2: Can bags withstand prolonged outdoor storage?
A: Yes. VidePak’s UV-resistant BOPP lamination ensures 18-month durability under direct sunlight, compliant with AS 2074.
Q3: Are your bags compatible with automated palletizers?
A: Absolutely. Our block-bottom valve bags feature anti-slip coatings and standardized dimensions (e.g., 90×55 cm) for robotic handling at 1,000 bags/hour.
Product Parameter Comparison Table
Parameter | Cement Bags | Gypsum Bags | Aggregate Bags |
---|---|---|---|
Material | BOPP-laminated PP | Kraft-lined PP | Heavy-duty PP |
GSM | 130 | 110 | 150 |
Max Load | 50 kg | 40 kg | 60 kg |
Moisture Barrier | 0.5g/m²/24hr | 0.3g/m²/24hr | 1.0g/m²/24hr |
Compliance | EN 13590, ASTM | JIS Z1531 | AS 2074 |
References
- European Committee for Standardization. (2024). EN 13590: Packaging for Construction Materials.
- ASTM International. (2023). ASTM D4632: Standard Test Method for Grab Breaking Load of Woven Fabrics.
- VidePak Technical Manual. (2025). BOPP-Laminated Woven Bags: Performance Metrics.
Explore Our Solutions Further:
- BOPP-Laminated Woven Bags: Advanced Moisture Protection
- Kraft Paper Composite Bags for Powder Integrity
By harmonizing material innovation, regulatory compliance, and operational scalability, VidePak empowers industries to transcend traditional packaging limitations. Contact our team to engineer a solution tailored to your most demanding logistics environments.