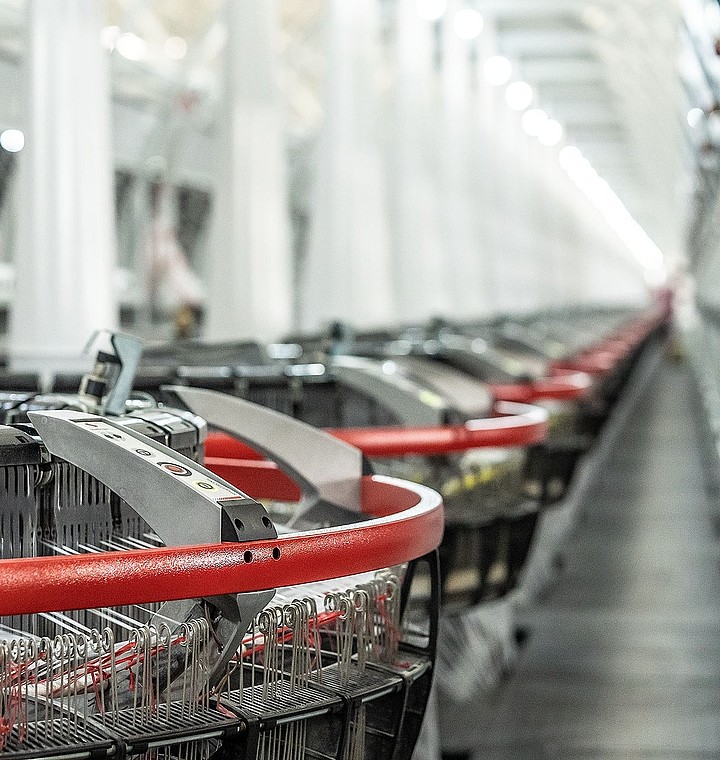
“Packaging is no longer just a container—it’s a critical interface between product safety, sustainability, and consumer trust,” asserts Ray, CEO of VidePak, during a client briefing. This report demonstrates how Kraft paper aluminum foil bags, with their unique hybrid structure and compliance-driven design, address evolving demands for barrier protection, eco-friendliness, and regulatory alignment in industries ranging from food to pharmaceuticals. By integrating material science innovations and rigorous health-safety protocols, these bags exemplify the future of intelligent packaging solutions.
1. Structural Advantages and Functional Diversity
1.1 Hybrid Material Engineering
Kraft paper aluminum foil bags combine three layers:
- Outer Kraft Paper: Provides mechanical strength (tensile strength: 20–25 N/mm²) and printability for branding.
- Middle Aluminum Foil: Delivers exceptional oxygen (<0.05 cm³/m²/day) and moisture barriers (WVTR <1 g/m²/day), critical for sensitive products like coffee or pharmaceuticals.
- Inner PE/PP Coating: Enhances heat-sealability and prevents chemical migration, complying with FDA CFR 21 for food contact.
Case Study: A 2024 trial with a European coffee brand showed VidePak’s aluminum foil laminated bags extended shelf life by 40% compared to standard Kraft paper bags, reducing oxidation-induced flavor loss.
1.2 Application-Specific Customization
Industry | Design Focus | Performance Metrics |
---|---|---|
Food & Beverage | UV-resistant prints + resealable zippers | Oxygen barrier >99%, microbial growth inhibition |
Pharmaceuticals | Anti-static coatings + tamper-evident seals | Compliance with USP <671> for container integrity |
Agriculture | Breathable micro-perforations | Moisture control (RH <60%), pest resistance |
2. Health and Safety: A Framework for Evaluation
2.1 Material Safety and Regulatory Compliance
Kraft paper aluminum foil bags must meet stringent standards:
- Chemical Migration: Total migration limits <10 mg/dm² (EU 10/2011), tested via ISO 11816-1 protocols.
- Microbial Resistance: Antimicrobial additives (e.g., silver ions) reduce E. coli contamination by 99.9% within 24 hours (ISO 22196).
- Recyclability: VidePak’s separable laminate technology enables 85% material recovery via hydro-pulping, aligning with ISO 15270.
2.2 Mechanical Durability Testing
- Tensile Strength: ≥30 N/mm² (ASTM D5034), ensuring load-bearing capacity for 25–50 kg contents.
- Puncture Resistance: >500 g/mil (ASTM D1709), critical for sharp-edged goods like frozen produce.
- Seam Integrity: Heat-sealed seams withstand 15 N/mm² stress, preventing leakage under hydrostatic pressure.
3. VidePak’s Operational Excellence: Bridging Innovation and Compliance
Founded in 2008, VidePak operates 30+ lamination machines and 16 extrusion lines, producing 50 million Kraft paper aluminum foil bags annually. Key differentiators include:
- Starlinger Technology: Precision co-extrusion ensures <5% thickness variation in aluminum foil layers.
- ESG Integration: A 2 MW solar system reduces carbon footprint by 1,200 tons/year, while 100% virgin PP/PE materials ensure FDA compliance.
4. Market Trends and Strategic Insights
The global barrier packaging market is projected to reach $44.2 billion by 2027 (Grand View Research). VidePak’s R&D in biodegradable PLA-aluminum hybrids and partnerships with IoT firms for smart temperature-logging bags position it as an industry pioneer. Competitors must adopt blockchain traceability and AI-driven defect detection to remain competitive.
5. FAQs: Addressing Critical Concerns
Q1: How do aluminum foil bags compare to PE-lined options for food safety?
A: Aluminum foil provides 10x better oxygen barrier performance, reducing lipid oxidation in snacks by 70%. PE liners are cost-effective but lack comparable UV resistance.
Q2: Are these bags suitable for high-moisture environments?
A: Yes. VidePak’s BOPP-coated variants achieve WVTR <0.5 g/m²/day, ideal for tropical climates.
Conclusion
Kraft paper aluminum foil bags represent a paradigm shift in packaging, merging ecological responsibility with uncompromising safety. By prioritizing barrier technologies, regulatory adherence, and consumer-centric design, VidePak not only meets but anticipates the needs of a dynamic global market. As Ray concludes, “Every layer in our bags isn’t just material—it’s a promise of protection.”
External Links:
- Explore how aluminum foil composite bags navigate market trends in sustainability-driven economies.
- Discover moisture-proof solutions for diverse applications to enhance supply chain reliability.