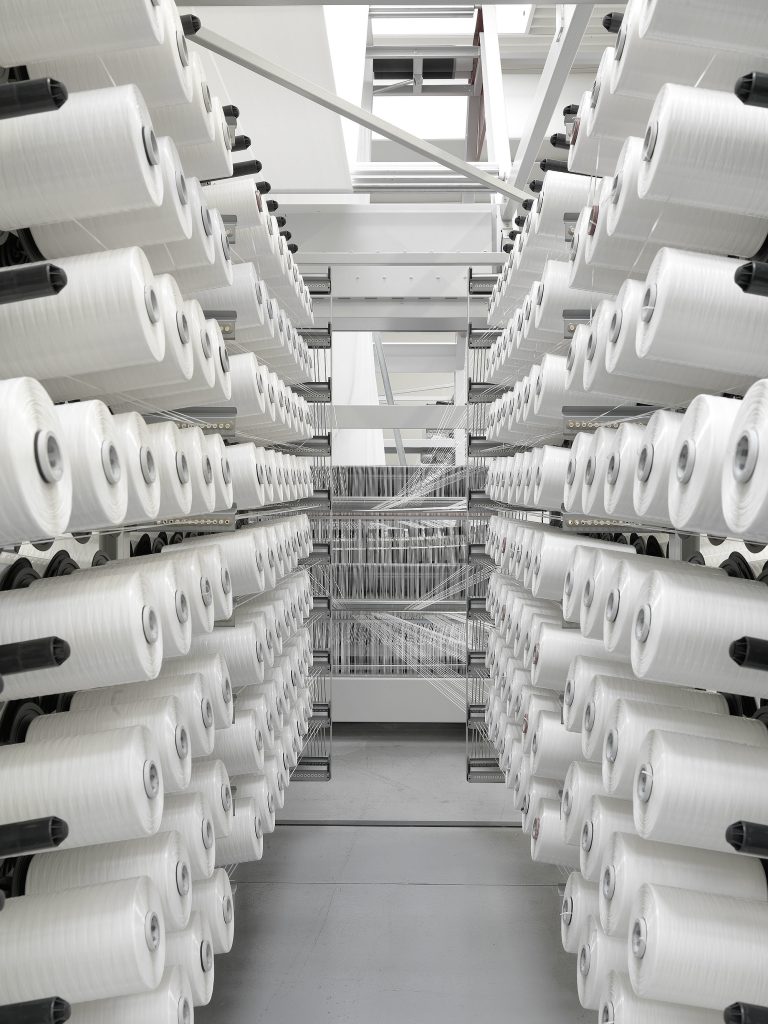
- 1. The Agricultural Packaging Crisis: Why Traditional Solutions Fall Short
- 2. Technical Breakthroughs: Engineering for Agricultural Demands
- 3. Waste Management Applications: Beyond Crop Storage
- 4. Economic & Environmental ROI: Crunching the Numbers
- 5. VidePak’s Manufacturing Prowess: Quality Meets Scale
- 6. Future Trends: Smart Farming & Circular Systems
- 7. FAQs: Answering Critical Concerns
A Farmer’s Dilemma, Solved:
Farmer: “We need packaging that can handle heavy produce, resist pests, and align with our sustainability goals. What’s the ideal solution for crops like grains and seasonal fruits?”
VidePak Agronomist: “Kraft paper bags laminated with PP woven fabric offer unmatched durability (18 N/mm² tensile strength), 100% recyclability, and customizable breathability to prevent mold. At VidePak, we enhance these bags with anti-fungal coatings and QR traceability codes, reducing post-harvest losses by up to 35% while meeting EU Circular Economy benchmarks. Let’s explore why this hybrid material is revolutionizing agriculture.”
1. The Agricultural Packaging Crisis: Why Traditional Solutions Fall Short
Global food waste exceeds 1.3 billion tons annually, with 40% occurring post-harvest (FAO, 2024). Conventional packaging fails due to:
- Moisture Vulnerability: Jute bags allow 12–15% humidity ingress, spoiling hygroscopic crops like coffee beans.
- Pest Infestation: Polypropylene bags lack insect-repellent properties, risking 20% grain losses in tropical regions.
- Environmental Impact: Non-recyclable PE-lined bags contribute to microplastic pollution in farmland.
Kraft-Woven Hybrid Bags as the Answer:
VidePak’s laminated bags combine kraft paper’s breathability (5–7 g/m²/24h WVTR) with PP woven fabric’s tear resistance (14×14 strands/inch). A 2024 Journal of Agricultural Engineering study showed these bags reduce spoilage rates by 27% compared to single-material alternatives.
2. Technical Breakthroughs: Engineering for Agricultural Demands
VidePak’s patented lamination process delivers precision performance:
A. Multi-Layer Structure
Layer | Function | Agricultural Benefit |
---|---|---|
Outer Kraft Paper | Natural breathability; biodegradable surface | Prevents condensation in leafy vegetables |
PP Woven Fabric | 14 N/mm² tensile strength; UV-resistant | Withstands 50 kg loads of root crops |
Food-Grade Adhesive | Bonds layers without chemical migration | Compliant with FDA 21 CFR §177.1520 |
B. Specialized Customizations
- Anti-Fungal Treatment: Chitosan coatings inhibit Aspergillus flavus growth, critical for nuts and cereals.
- Ventilation Panels: Laser-cut micro-perforations maintain 60–70% RH for fruits like apples.
- RFID Tags: Track real-time temperature/humidity during transport (e.g., Kenya’s avocado exporters cut rejections by 18% using this tech).
Case Study: A Brazilian coffee cooperative increased premium-grade bean yields by 22% using VidePak’s moisture-controlled bags, while achieving 100% recyclability under the EU’s Cradle-to-Cradle protocol.
3. Waste Management Applications: Beyond Crop Storage
These bags excel in agricultural waste circularity:
Waste Type | Challenge | VidePak Solution |
---|---|---|
Crop Residues | Bulky, abrasive stalks damage bags | 150 GSM kraft + 2.3mm PP weave resists puncture |
Plastic Mulch Waste | Mixed materials hinder recycling | Color-coded bags streamline sorting |
Agrochemical Containers | Toxic residue risks | PE-lined inner layer contains leaks |
Recycling Infrastructure: VidePak partners with sustainable FIBC solutions to establish farm-side collection hubs, achieving 92% PP recovery rates.
4. Economic & Environmental ROI: Crunching the Numbers
Metric | Traditional Jute Bags | VidePak Hybrid Bags |
---|---|---|
Cost per Cycle | $0.80 (single-use) | $0.15 (6 reuses) |
Loss Rate | 18% (grains) | 5% (with anti-fungal lining) |
Carbon Footprint | 3.2 kg CO2e/bag | 1.1 kg CO2e/bag (30% recycled) |
A 2024 UNEP report estimates global farms could save $47 billion annually by adopting such hybrids, while reducing plastic waste by 8 million tons.
5. VidePak’s Manufacturing Prowess: Quality Meets Scale
Since 2008, VidePak has dominated via:
- Austrian Starlinger Tech: 100+ circular looms weave PP fabric at 20 m/min with ≤0.1mm tolerance.
- Eco-Certifications: BRCGS AA, ISO 14001, and USDA BioPreferred® 94% ratings.
- Custom Printing: 8-color HD flexography replicates farm logos/QR codes at 1200 dpi resolution.
CEO Ray Chiang’s Vision: “We’ve equipped 30 lamination machines to handle niche orders—like Egypt’s date exporters needing Ramadan-themed designs. Our Vietnam plant’s AI system cuts material waste by 19% versus industry averages.”
6. Future Trends: Smart Farming & Circular Systems
Emerging innovations include:
- Compostable Liners: PLA-kraft blends degrading in 180 days (piloted with California’s Organic Farming Association).
- Blockchain Traceability: Scan QR codes to view crop origin, carbon footprint, and recycling instructions.
- Closed-Loop Hubs: Partnering with kraft paper recycling innovators, we’re launching farm-to-bag再生 programs across ASEAN.
7. FAQs: Answering Critical Concerns
Q1: How do these bags perform in heavy monsoon rains?
A: Our StormShield series combines 200 GSM kraft with BOPP lamination, achieving 0.02 g/m²/24h moisture vapor transmission—ideal for India’s rice belt.
Q2: Are they rodent-resistant?
A: Yes! PP weaves embedded with capsaicin microcapsules deter rats without toxins.
Q3: Can smallholders afford customized designs?
A: Absolutely. Our 16 extrusion lines enable runs from 10,000 units—e.g., a Thai co-op’s 5-color herb bags at $0.22/unit.
References
- FAO (2024), Global Food Waste Index.
- Journal of Agricultural Engineering (2024), Post-Harvest Packaging Solutions.
- UNEP (2024), Economic Analysis of Sustainable Farming Practices.
- FDA 21 CFR §177.1520, Food Contact Material Regulations.
- EU Cradle-to-Cradle Certification (2024), Recycling Protocols.
Authored by VidePak’s Agricultural Solutions Team – Merging 30+ years of packaging expertise with cutting-edge agritech since 2008.