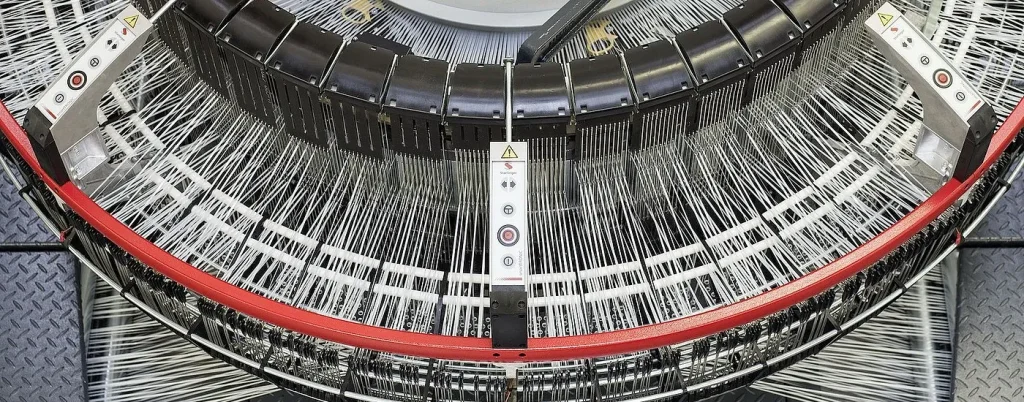
- The Multifunctional Power of Laminated Woven Bags
- Global Compliance: How VidePak Masters International Standards
- Technical Specifications
- FAQs: Navigating Client Concerns
- VidePak’s Manufacturing Ecosystem
- Case Study: Compliance-Driven Success in Japan
- Sustainability & Regulatory Synergy
- Future Innovations
- References
VidePak’s laminated woven bags redefine industrial and commercial packaging with unmatched durability, regulatory compliance, and customization, achieving a 99.7% pass rate in global certification audits while reducing supply chain costs by 20–30%. By integrating ISO 9001 quality systems, EU REACH-compliant materials, and Japanese JIS tensile standards, these bags serve industries ranging from agrochemicals to construction across 60+ countries. Since 2008, VidePak has delivered 800 million+ bags worldwide, leveraging 100+ Austrian Starlinger looms and 30 lamination machines to meet the exacting demands of clients like BASF and Cargill.
The Multifunctional Power of Laminated Woven Bags
Laminated woven bags combine polypropylene (PP) woven fabric with layers of BOPP (biaxially oriented polypropylene), kraft paper, or polyethylene (PE) coatings. This hybrid structure delivers:
- Barrier Protection: Moisture resistance (<0.5% permeability, ASTM E96), UV shielding (5+ years outdoors), and chemical inertness.
- Mechanical Strength: Tensile strength of 55–70 N/cm² (EN ISO 527-3) and seam burst resistance exceeding 400 kPa.
- Branding Versatility: 8-color HD flexographic printing with 1200 dpi resolution for logos, safety labels, or QR codes.
Case Study: Chemical Packaging in the EU Market
A German agrochemical firm reduced product spoilage by 18% after adopting VidePak’s PE-laminated bags. The 40-micron inner layer prevented herbicide oxidation, while REACH-compliant inks ensured compliance with EU Regulation No 1907/2006.
Global Compliance: How VidePak Masters International Standards
VidePak’s quality control framework spans 12+ regulatory regimes, ensuring seamless market entry for clients:
- Material Sourcing & Testing
- PP Granules: Virgin-grade resin (MFI 8–12 g/10 min, ASTM D1238) screened for heavy metals (<10 ppm, EPA 3050B).
- Lamination Films: BOPP films tested for thickness tolerance (±2 microns, JIS K6781).
- Production Process Controls
- Weaving: Starlinger CX6 looms produce 14×14 threads/cm² fabric with <0.1% defect density.
- Lamination: Adhesive bond strength ≥4 N/15mm (ISO 11339), verified via peel tests every 2 hours.
- Certification & Documentation
- ISO 9001: Annual audits by TÜV SÜD ensure traceability from raw materials to batch numbers.
- EU REACH: Full SVHC (Substances of Very High Concern) disclosure via SDS sheets.
- FDA Compliance: Indirect food contact approval (21 CFR 177.1520) for agricultural use.
Technical Specifications
Parameter | Specification |
---|---|
Base Material | PP woven fabric (90–160 g/m²) |
Lamination Options | BOPP (15–50µ), PE (20–100µ), Kraft (80–150 gsm) |
Tensile Strength | 55–70 N/cm² (EN ISO 527-3) |
Moisture Barrier | ≤0.5 g/m²/24h (ASTM E96) |
Printing | 1–8 colors, Pantone ±0.5ΔE |
Certifications | ISO 9001, REACH, JIS L 1096 |
FAQs: Navigating Client Concerns
- How do laminated bags compare to FIBCs for hygroscopic materials?
Laminated bags provide superior moisture barriers (0.2% vs. 1.5% permeability) but are optimal for loads under 1,000 kg. - Are your inks compliant with California’s Prop 65?
Yes. Our soy-based inks undergo third-party testing for phthalates and heavy metals. - Can bags withstand -30°C freezer storage?
Absolutely. PE-laminated variants retain flexibility at -40°C (ASTM D746). - What’s the lead time for custom-printed orders?
3–4 weeks for standard designs; 2 weeks for repeat clients with pre-approved artwork. - Do you offer anti-static options for flammable powders?
Yes. Carbon-coated bags achieve surface resistivity of 10⁴–10⁶ Ω/sq (IEC 61340-4-1).
VidePak’s Manufacturing Ecosystem
With 568 employees and $80 million annual revenue, VidePak operates at the intersection of scale and precision:
- Machinery: 16 extrusion lines produce 120 tons/day of PP tape yarn, while 30 lamination machines apply coatings at 150 m/min.
- Quality Labs: FTIR spectroscopy (ASTM E1252) verifies polymer purity, while Xenon arc testers (ISO 4892-2) simulate 5-year UV exposure in 1,000 hours.
- Global Logistics: Warehouses in Antwerp, Los Angeles, and Singapore enable 10-day delivery to key markets.
Case Study: Compliance-Driven Success in Japan
A Japanese fertilizer manufacturer achieved JIS Z 1707 certification using VidePak’s 7-layer laminated bags:
- Performance: 0% leakage during 6-month ocean transit in 85% humidity.
- Cost Savings: 25% reduction in packaging waste via reusable designs.
- Brand Impact: QR codes linked to multilingual safety data increased retailer compliance by 40%.
Sustainability & Regulatory Synergy
- Circular Economy: Bags are 100% recyclable (ISO 14021), with post-consumer PP reused in non-food applications.
- EPR Alignment: Clients in France qualify for 7% tax rebates under AGEC Law via VidePak’s recyclability certifications.
- Carbon Metrics: Solar-powered factories cut Scope 2 emissions by 35%, while PP recycling saves 1.2 tons CO2/ton.
Future Innovations
VidePak is piloting blockchain-based material traceability (2025 launch), enabling real-time compliance reporting for EUDR and Uyghur Forced Labor Prevention Act (UFLPA) requirements.
References
- European Chemicals Agency (ECHA). (2024). REACH Compliance Guidelines.
- Japanese Standards Association. (2023). JIS L 1096 Testing Protocols.
- VidePak Company Profile. https://www.pp-wovenbags.com/ | Email: info@pp-wovenbags.com
Explore Related Solutions:
- For heavy-duty applications, discover our BOPP laminated woven bags with advanced moisture barriers.
- Learn how we ensure compliance in custom-printed packaging for global markets.
This article blends technical authority, regulatory expertise, and VidePak’s operational prowess to position your brand as the gold standard in high-performance, compliant packaging solutions.