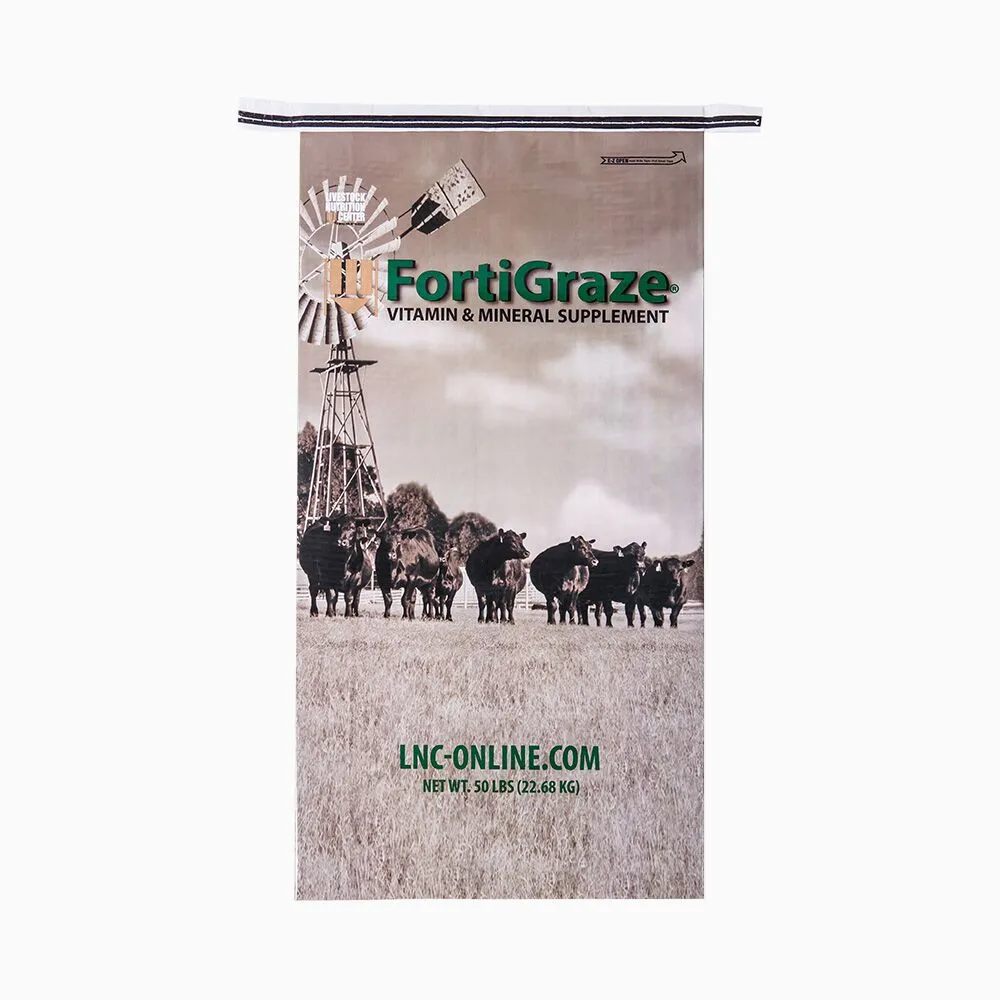
- The Process of Manufacturing Laminated Woven Bags
- Breathable Design: Ideal for Agricultural Products
- Barrier Design: Protection from External Elements
- Anti-Static Design: Critical for Safety in Hazardous Environments
- Antimicrobial Properties: Ensuring Safety in Food and Medical Packaging
- Applications Across Industries
- Conclusion
Laminated woven bags, commonly referred to as BOPP woven bags, have become a cornerstone of the packaging industry due to their durability, flexibility, and versatility. In particular, laminated woven sacks are used across various sectors for their unique ability to combine strength with protective characteristics, ensuring that the contents remain safe, secure, and undamaged throughout the supply chain. With advanced manufacturing techniques like multi-wall woven bags and multi-layered co-extrusion blown film processes, these bags offer significant benefits that can be customized for specific needs.
The adoption of Laminated Woven Bags has been growing in diverse applications, from agricultural products and food packaging to industrial uses. Their popularity can be attributed to several innovative features, including the ability to create barriers for moisture, oxygen, and other external factors that could compromise the integrity of the goods inside. Additionally, as markets evolve to become more eco-conscious, Laminated PP bags have also become increasingly sought after due to their sustainability credentials. For an in-depth exploration of Laminated Woven Bags, check out this article about Laminated Woven Bags and for BOPP Woven Bags, see BOPP Woven Bags.
The Process of Manufacturing Laminated Woven Bags
The production of Laminated Woven Bags involves advanced techniques, particularly the multi-layered co-extrusion blown film process, which allows for the creation of bags with several layers of film. This process not only enhances the strength of the material but also provides various customization options, including the ability to add specific barrier properties for different applications. Below is a table illustrating the essential parameters of laminated woven bags:
Feature | Specification |
---|---|
Material | BOPP (Biaxially Oriented Polypropylene), PP, PET |
Layers | Multi-layered co-extrusion, typically 2-4 layers for added protection |
Printing | High-quality multi-color printing, customizable graphics, and branding |
Size | Custom sizes ranging from small retail packaging to large industrial bags |
Strength | High tensile strength and tear resistance due to woven fabric and lamination |
Barrier Properties | Moisture, oxygen, UV, and gas barrier options available depending on the product |
Custom Features | Anti-static, breathable, antimicrobial coatings, or special coatings for food and medical applications |
Sustainability | Recyclable, eco-friendly materials with minimal environmental impact |
These versatile packaging solutions are perfect for industries that require specific functionalities such as moisture control, barrier protection, or anti-static properties. Understanding the different layers and materials involved in their manufacture allows for better decision-making regarding the most suitable options for various industries.
Breathable Design: Ideal for Agricultural Products
When packaging agricultural products such as grains, rice, or other fresh produce, it is crucial to design Laminated Woven Bags with the ability to breathe. Breathable bags facilitate the escape of moisture and heat, which helps prevent the build-up of condensation within the bag, a key cause of mold and product spoilage. By incorporating a breathable design, these bags allow air to circulate, ensuring that moisture is expelled and temperatures inside the bag are regulated.
This design feature is particularly beneficial in regions where agricultural products are stored for extended periods before being transported or sold. For example, BOPP woven bags with perforated or breathable films can assist in maintaining the quality of stored grain, ensuring that it stays dry and free from spoilage due to excess humidity.
Barrier Design: Protection from External Elements
One of the major advantages of Laminated Woven Bags is their ability to be customized to provide barrier protection. In many cases, these bags are designed with special layers to provide resistance to gases, moisture, and even odors. This is especially useful in industries such as food, pharmaceuticals, or chemicals, where the contents must remain unaffected by external elements.
The multi-layer construction allows the addition of an oxygen barrier or a moisture barrier, which prevents degradation of the contents inside the bag. For example, food manufacturers often rely on Laminated Woven Bags to pack snacks, grains, or dried products, ensuring that the contents stay fresh for extended periods without the risk of exposure to contaminants. The same technology is often used to package pharmaceuticals to preserve the potency and quality of sensitive products.
Anti-Static Design: Critical for Safety in Hazardous Environments
Anti-static designs are another innovative feature offered by Laminated PP bags, which are especially useful in industries where static electricity poses a significant risk. In environments dealing with flammable dust or chemicals, static discharge can lead to explosions or fires. This makes anti-static protection a necessity in packaging, particularly in industries like electronics, chemicals, and pharmaceuticals.
By incorporating anti-static materials into the design of multi-wall woven bags, manufacturers can minimize the risk of dangerous sparks caused by electrostatic discharge. Such bags are typically made using conductive or dissipative yarns that safely channel static charge away from the contents of the bag. This ensures that sensitive products, like electronic components or fine powders, remain safe from the risk of static buildup and the potential for catastrophic events.
Antimicrobial Properties: Ensuring Safety in Food and Medical Packaging
For industries dealing with food or pharmaceuticals, the need for hygiene and safety is paramount. Laminated Woven Bags can be treated with antimicrobial coatings or made from antimicrobial fibers to prevent the growth of bacteria and fungi, which could otherwise compromise the integrity of the product inside.
For instance, in the food industry, Laminated Woven Sacks can be coated with antimicrobial agents that help prevent contamination during storage or transportation. Similarly, in medical applications, antibacterial bags are essential for safely packaging sensitive items, such as medical supplies or pharmaceuticals, which need to be kept free from bacteria and other pathogens.
Applications Across Industries
The diverse design options available for Laminated Woven Bags make them suitable for a variety of applications. Below are some examples of their use across different industries:
- Agriculture: Used for packaging grains, rice, and vegetables, breathable woven bags maintain product quality during storage and transport.
- Food Industry: Barrier bags keep products like snacks, grains, and dried foods fresh for extended periods by preventing exposure to moisture and air.
- Electronics and Pharmaceuticals: Anti-static woven sacks ensure the safe transportation and storage of sensitive electronic components and medicines.
- Medical and Hygiene Products: Antimicrobial laminated woven bags are used to safely package medical supplies, pharmaceuticals, and other hygiene products.
Conclusion
Laminated Woven Bags have evolved far beyond simple packaging solutions, offering custom features such as breathable designs, barrier protection, anti-static properties, and antimicrobial coatings. These innovations provide tailored solutions for industries ranging from agriculture and food to electronics and pharmaceuticals. By leveraging advanced production techniques, such as the multi-layered co-extrusion blown film process, these bags are designed to meet the specific needs of businesses while ensuring product safety, quality, and compliance with industry standards. The ability to adapt and customize these bags for different applications highlights their role as essential tools in modern packaging.