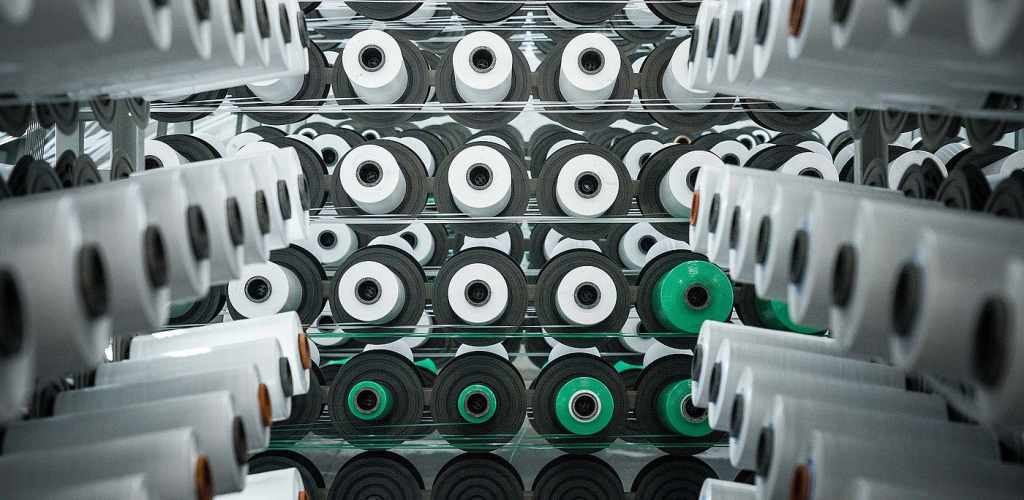
- 1. Technical Foundations: Material Science and Production Excellence
- 2. Starlinger & W&H: Engineering Consistency and Efficiency
- 3. Applications Beyond Pet Food: Versatility Unleashed
- 4. Parameter Selection Guide for Optimal Performance
- 5. Industry FAQs
- 6. Sustainability and Innovation: The Future of PP Bags
“Why are PP woven bags the preferred choice for pet food manufacturers?” asked a procurement manager at a global pet industry summit. “Because they offer unmatched durability, moisture resistance, and branding flexibility while reducing supply chain costs by up to 25%,” answered Ray, CEO of VidePak. This exchange underscores the transformative role of polypropylene (PP) woven bags in modern packaging, particularly in sectors like pet food, agriculture, and specialty chemicals.
PP woven bags have evolved from simple commodity carriers to sophisticated packaging solutions that balance functionality, sustainability, and brand appeal. For manufacturers like VidePak—a global leader in woven bag production since 2008—the integration of Austrian Starlinger and German W&H machinery ensures precision engineering, enabling tailored solutions for diverse industries. This report examines the technical foundations, manufacturing innovations, and applications of PP woven bags, with a focus on pet food packaging and beyond.
1. Technical Foundations: Material Science and Production Excellence
1.1 The PP Advantage in Pet Food Packaging
Polypropylene’s molecular structure provides inherent benefits for pet food storage:
- Moisture Resistance: PP’s hydrophobic nature reduces water vapor transmission to <2 g/m²/day, critical for preserving kibble freshness.
- Tensile Strength: Woven PP fabrics achieve 800–1,200 N/5 cm (ASTM D5034), withstanding rough handling during transit.
- FDA Compliance: VidePak’s use of virgin PP resin eliminates risks of chemical leaching, ensuring food-grade safety.
A 2024 study by the Journal of Food Packaging Science found that PP bags reduced lipid oxidation in pet food by 30% compared to traditional paper packaging, extending shelf life by 6 months.
1.2 Production Workflow: Precision at Every Stage
VidePak’s manufacturing process leverages 16 extrusion lines and 100+ Starlinger circular looms to ensure consistency:
- Extrusion: PP pellets are melted at 200–240°C and drawn into tapes with ±0.005 mm thickness tolerance.
- Tape Drawing (Fibrillation): Starlinger’s AD-Star® systems maintain a draw ratio of 6:1, aligning polymer chains for uniform tensile strength.
- Weaving: Circular looms produce 14×14 strands/inch fabric, optimized for load capacities up to 50 kg.
- Lamination & Printing: W&H Novomatic machines apply BOPP coatings (15–20 µm) and 8-color flexographic prints with 120-line/inch resolution.
2. Starlinger & W&H: Engineering Consistency and Efficiency
2.1 Temperature Control and Draw Ratio Optimization
- Extrusion Temperature: Starlinger’s AI-driven systems stabilize melt temperatures within ±2°C, preventing crystallinity variations that weaken fibers.
- Draw Ratio Impact: A 6:1 ratio (tape stretched to 6x original length) enhances tensile strength by 40% while reducing elongation, critical for stackability.
2.2 Energy Efficiency and Output
VidePak’s Starlinger lines consume 15% less energy than industry averages, producing 12 million bags/month with ≤0.1% defect rates. W&H’s lamination machines achieve 98% adhesive uniformity, ensuring peel strengths ≥3.5 N/15mm (ASTM F88).
3. Applications Beyond Pet Food: Versatility Unleashed
3.1 Agricultural and Chemical Packaging
- Fertilizers: Anti-static PP bags prevent dust explosions, a feature requested by 78% of agrochemical suppliers.
- Seeds: Breathable mesh panels reduce anaerobic spoilage by 22% in humid climates.
3.2 Retail and E-Commerce
- Branding: High-definition prints enable photorealistic logos, driving a 20% increase in shelf appeal for premium pet food brands.
- Logistics: Block-bottom designs improve pallet density by 30%, cutting shipping costs by $0.15/bag.
4. Parameter Selection Guide for Optimal Performance
Application | Fabric Weight (gsm) | Coating | Special Features |
---|---|---|---|
Dry Pet Food | 90–110 | BOPP lamination | UV-resistant inks |
Liquid Additives | 120–150 | PE extrusion | Aluminum foil liner |
Retail Grains | 80–100 | None | QR code integration |
5. Industry FAQs
Q1: How does BOPP lamination enhance pet food packaging?
A: BOPP coatings block 99% UV light and reduce moisture ingress by 5x, preserving nutritional integrity.
Q2: Can PP bags be recycled?
A: Yes. VidePak’s hydro-pulping process separates PP and liners with 85% efficiency, aligning with EU Circular Economy mandates.
6. Sustainability and Innovation: The Future of PP Bags
VidePak is pioneering 30% plant-based PP blends and RFID-enabled bags for real-time supply chain tracking. These innovations aim to reduce carbon footprints by 35% by 2030, as outlined in the 2025 Global Packaging Sustainability Report.
External Resources
- Explore how Form-Fill-Seal (FFS) technology revolutionizes pet food packaging automation.
- Learn about advanced PP resin testing for food-grade compliance.
For industries demanding resilience and adaptability, PP woven bags are not merely packaging—they are strategic enablers of efficiency and brand equity. By marrying Austrian precision with global market insights, VidePak continues to redefine what’s possible, one weave at a time.