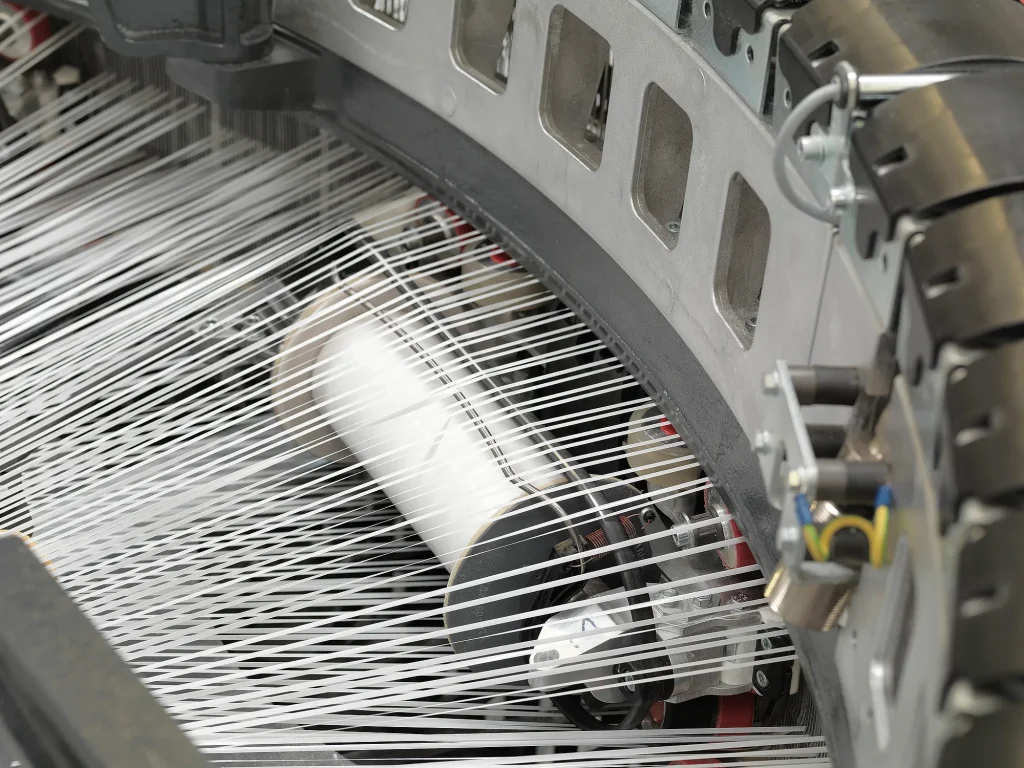
- 1. Technical Challenges in Fertilizer Packaging
- 2. Material Science: PP Fabric Engineering
- 3. Global Compliance: Navigating Regional Standards
- 4. Parameter Selection Guide
- 5. Sustainability Metrics
- 6. FAQs: Addressing Fertilizer Industry Concerns
- 7. VidePak’s Manufacturing Edge
- 8. Future-Proof Packaging: Smart Technologies
In the global fertilizer industry, where moisture absorption can degrade product quality by up to 40% within six months, recyclable polypropylene (PP) woven bags have become indispensable, offering a 35% reduction in humidity-related losses while meeting stringent international sustainability standards. A 2023 study by the International Fertilizer Association revealed that facilities using PP bags with BOPP lamination achieved 98% nutrient preservation over 18-month storage periods. At VidePak, leveraging 30+ years of expertise and 100+ Starlinger circular looms, we engineer PP packaging systems that address the unique challenges of chemical fertilizers—from ammonium nitrate’s hygroscopicity to urea’s volatility. This article dissects technical parameters, regulatory frameworks, and application-specific innovations that define modern fertilizer packaging.
1. Technical Challenges in Fertilizer Packaging
Chemical fertilizers demand packaging solutions that balance containment, durability, and environmental compliance:
Fertilizer Type | Key Challenge | Critical Packaging Property |
---|---|---|
Ammonium Nitrate | Hygroscopicity (absorbs 25% moisture) | WVTR ≤5 g/m²/day via 0.1 mm BOPP lamination |
Urea | Volatility (NH3 emission) | Hermetic seals with ≤0.01% gas permeability |
NPK Compounds | Caking under pressure | Anti-static coatings (≤10^8 Ω/sq surface resistivity) |
Case Study: A Brazilian fertilizer producer reduced caking by 60% using VidePak’s 120 g/m² PP bags with 0.12 mm PE liners and carbon-black anti-static treatments.
2. Material Science: PP Fabric Engineering
VidePak’s PP bags are engineered through three critical processes:
2.1 Weave Density Optimization
- Thread Configuration: 14×14 strands/cm² for fine powders vs. 10×10 for granules
- Yarn Thickness: 1,200D high-tenacity PP resists ≥1,800 N/cm² bursting pressure (ISO 13934-1)
2.2 Advanced Lamination Technologies
Coating Type | Fertilizer Application | Performance Benchmark |
---|---|---|
BOPP Extrusion | Coastal urea storage | Salt spray resistance >1,500 hrs (ASTM B117) |
PE Film Lamination | Ammonium sulfate in humid climates | WVTR ≤3 g/m²/day (TAPPI T464) |
3. Global Compliance: Navigating Regional Standards
Standard | Key Requirement | VidePak Solution |
---|---|---|
EU EN 13432 | Compostability for organic coatings | Bio-PE liners degrading in 180 days |
ASTM D5276-19 | 8-layer pallet stackability | Cross-woven fabric with 150 g/m² density |
JIS Z 0200 | 85% RH moisture resistance | 0.15 mm BOPP lamination + desiccant valve |
AS 2070-1999 | UV resistance for outdoor storage | UV-stabilized PP with 1,200 hrs Xenon arc rating |
4. Parameter Selection Guide
Factor | Bulk Fertilizers | Premium Blends |
---|---|---|
Fabric Weight | 90–100 g/m² | 120–150 g/m² laminated PP |
Liner Thickness | 0.06 mm PE | 0.1 mm EVOH barrier film |
Seam Type | Double-stitched with Kevlar® | Ultrasonic welded (40 N/cm peel) |
Valve Design | Simple pasted valve | Anti-backflow with dust filter |
Example Configuration:
- Compound Fertilizers (20–50 kg): 100 g/m² PP + 0.08 mm BOPP + double-stitched seams
- Liquid Additives: 150 g/m² cross-laminated PP + aluminum foil inner layer
5. Sustainability Metrics
VidePak’s circular economy initiatives ensure:
- 30–50% Post-Industrial Recycled (PIR) PP: Maintains ≥95% tensile strength vs. virgin material
- CO2 Reduction: Solar-powered production cuts emissions by 25% (1.8 kg CO2/bag)
- Closed-Loop Recycling: 98% material recovery rate via take-back programs
6. FAQs: Addressing Fertilizer Industry Concerns
Q1: How do PP bags prevent caking in humid climates?
A1: Our 0.1 mm BOPP lamination reduces WVTR to ≤5 g/m²/day, while anti-static treatments (≤10^8 Ω/sq) prevent particle adhesion.
Q2: Can bags withstand -20°C storage for liquid fertilizers?
A2: Yes. Cold-crack resistant PP blends maintain flexibility at -30°C (ASTM D746).
Q3: Are recycled PP bags compatible with automated filling?
A3: Absolutely. VidePak’s 30% PIR PP achieves identical melt flow index (2.5 g/10 min) to virgin resin.
7. VidePak’s Manufacturing Edge
With 16 extrusion lines and 30+ printing machines, we deliver:
- Annual Capacity: 200 million bags across 80+ countries
- Certifications: ISO 9001, BRCGS, ECOCERT
- Customization: 8-color HD printing with ≤0.2 mm registration accuracy
Explore our BOPP laminated woven bags for moisture-sensitive fertilizers or learn about high-speed valve bag systems for granular blends.
8. Future-Proof Packaging: Smart Technologies
- QR Traceability: Laser-engraved codes store batch data and application guidelines
- IoT Sensors: Monitor bag integrity via embedded temperature/humidity loggers
- Self-Healing Films: Microcapsules repair ≤2 mm punctures upon compression
References
- International Fertilizer Association. (2023). Moisture Management in Bulk Fertilizer Storage.
- ASTM International. (2023). Standard Test Methods for Flexible Packaging.
- VidePak Company Profile. https://www.pp-wovenbags.com/
- Contact: info@pp-wovenbags.com
External Links
- Discover moisture-resistant BOPP laminated woven bags for hygroscopic fertilizers.
- Optimize filling efficiency with VidePak’s valve bag solutions for granular compounds.