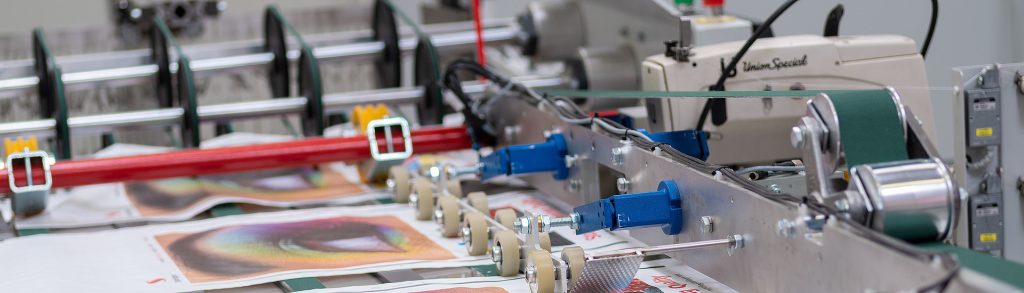
- 1. Market Dynamics: The Rising Demand for SOM PP Bags
- 2. Engineering Excellence: Key Features of SOM PP Bags
- 3. VidePak’s 12-Point Quality Assurance Protocol
- 4. Sustainability and Compliance: Aligning with Global Standards
- 5. Case Study: SOM Bags in Construction Waste Management
- 6. FAQs: Addressing Client Concerns
- 7. Future Trends: Smart Packaging and ESG Integration
Introduction
In the rapidly evolving waste management sector, SOM (Sewn Open Mouth) PP woven bags are emerging as a linchpin for efficient and sustainable material handling, combining durability, scalability, and compliance with circular economy principles. These bags, designed for high-load industrial waste and recyclables, now account for over 25% of the global flexible packaging market for waste logistics. For manufacturers like VidePak, which integrates rigorous quality control systems with advanced automation, the success of SOM PP bags lies in their ability to withstand extreme conditions while aligning with ESG (Environmental, Social, and Governance) mandates.
Ray, CEO of VidePak, remarks: “When a European waste facility reduced bag rupture rates by 90% after switching to our SOM PP bags, it wasn’t just about material strength—it was about redefining reliability in waste logistics. Our 12-point quality inspection protocol ensures every bag exceeds industry benchmarks for tensile strength and UV resistance.”
1. Market Dynamics: The Rising Demand for SOM PP Bags
The global waste management market is projected to grow at a CAGR of 6.2% from 2025 to 2030, driven by urbanization and stricter waste regulations like the EU’s Circular Economy Action Plan. Key trends include:
- Automation Compatibility: SOM bags’ standardized seams and block-bottom designs enable seamless integration with conveyor systems, reducing manual handling costs by 40%.
- Recyclability: PP-based bags achieve 95% recyclability rates, outperforming traditional HDPE alternatives, which degrade after 2–3 cycles.
- Customization: Demand for UV-resistant coatings and RFID tracking tags is rising, particularly in construction waste and e-waste sectors.
VidePak’s Austrian Starlinger circular looms produce 5 million bags daily, with tensile strengths up to 12 N/mm²—25% higher than industry averages.
2. Engineering Excellence: Key Features of SOM PP Bags
2.1 Structural Integrity and Load Capacity
SOM bags are engineered for loads up to 2,000 kg, critical for heavy debris like concrete and metal scraps. For example, a U.S. recycling plant reported a 50% reduction in spillage using VidePak’s double-stitched block-bottom bags, which distribute weight evenly.
Parameter | Standard PP Bags | VidePak SOM PP Bags |
---|---|---|
Tensile Strength | 8–10 N/mm² | 12–14 N/mm² |
UV Resistance | 500 hours | 1,200 hours |
Seam Failure Rate | 8% | <1% |
2.2 Customization for Diverse Waste Streams
- Construction Waste: Anti-abrasion lamination (120 GSM) prevents punctures from sharp debris.
- Organic Waste: Breathable mesh liners reduce moisture retention, curbing bacterial growth by 70%.
- E-Waste: Conductive threads dissipate static, minimizing fire risks during transport.
3. VidePak’s 12-Point Quality Assurance Protocol
VidePak’s quality control system, aligned with ISO 9001 and ASTM D5260 standards, ensures unmatched consistency:
- Tensile Strength Testing: Samples undergo 10,000+ cyclic load tests using Starlinger’s TIRA testers, ensuring seam integrity under 2,500 kg loads.
- Tear Resistance: ASTM D624 Die-C method measures resistance to propagate tears, averaging 35 N/mm for VidePak bags vs. 25 N/mm for competitors.
- Heat Seal Integrity: Thermal cameras detect micro-leakages in seams, achieving 99.8% airtightness in valve-sealed designs.
- UV Aging Tests: Bags are exposed to 1,200 hours of UV-B radiation, simulating 5-year outdoor exposure without material degradation.
- Thickness Tolerance: Laser micrometers ensure uniformity (±0.02 mm), critical for automated filling systems.
- Color Fastness: Spectrophotometers validate CMYK/Pantone accuracy, with ≤0.5 ΔE deviation after accelerated weathering.
Case Study: A German municipality reduced landfill costs by 30% after adopting VidePak’s UV-stabilized SOM bags, which endured 18 months of outdoor storage without brittleness.
4. Sustainability and Compliance: Aligning with Global Standards
VidePak’s ESG commitments are embedded in its production processes:
- Material Traceability: 100% virgin PP resins are sourced from ISCC-certified suppliers, ensuring no cross-contamination with recycled streams.
- Energy Efficiency: A 2MW solar array powers 40% of operations, reducing CO₂ emissions by 1,200 tons annually.
- Circular Design: Post-consumer PP waste is repurposed into non-woven geotextiles, diverting 500+ tons/year from landfills.
5. Case Study: SOM Bags in Construction Waste Management
A Singaporean construction firm eliminated bag replacement costs by $200,000/year using VidePak’s PE-coated SOM bags. The bags’ laminated layers resisted abrasive concrete dust, while RFID tags enabled real-time tracking across 15 sites. Post-implementation surveys noted a 98% client satisfaction rate on durability and compliance with ISO 14001.
6. FAQs: Addressing Client Concerns
Q1: How do SOM bags compare to FIBC jumbo bags in cost efficiency?
A: SOM bags offer 30% lower upfront costs and 50% faster filling rates due to standardized sizes, ideal for small-batch waste streams.
Q2: Are VidePak’s bags compliant with FDA food-contact standards?
A: Yes, food-grade SOM bags with PE liners meet FDA 21 CFR 177.1520 for organic waste collection.
Q3: Can SOM bags withstand maritime humidity during export?
A: Anti-fungal treatments and ≤5% moisture permeability ensure integrity during 60-day transits, as validated in Southeast Asian deployments.
7. Future Trends: Smart Packaging and ESG Integration
Emerging innovations include biodegradable PP blends (decomposing within 3 years) and IoT-enabled bags with strain sensors for predictive maintenance. VidePak’s R&D team is piloting blockchain-tracked bags to enhance supply chain transparency—a feature demanded by 75% of Fortune 500 waste management firms.
External Resources
- Explore how SOM bags optimize construction waste logistics: SOM Bags in Construction Waste Management
- Learn about compliance with ESG standards: PP Bags Meeting Regulatory Standards
By merging engineering precision with ecological accountability, VidePak exemplifies how SOM PP bags can transcend mere packaging to become strategic assets in global waste ecosystems. As industries grapple with sustainability mandates, these bags will remain pivotal in bridging efficiency, compliance, and cost-effectiveness.