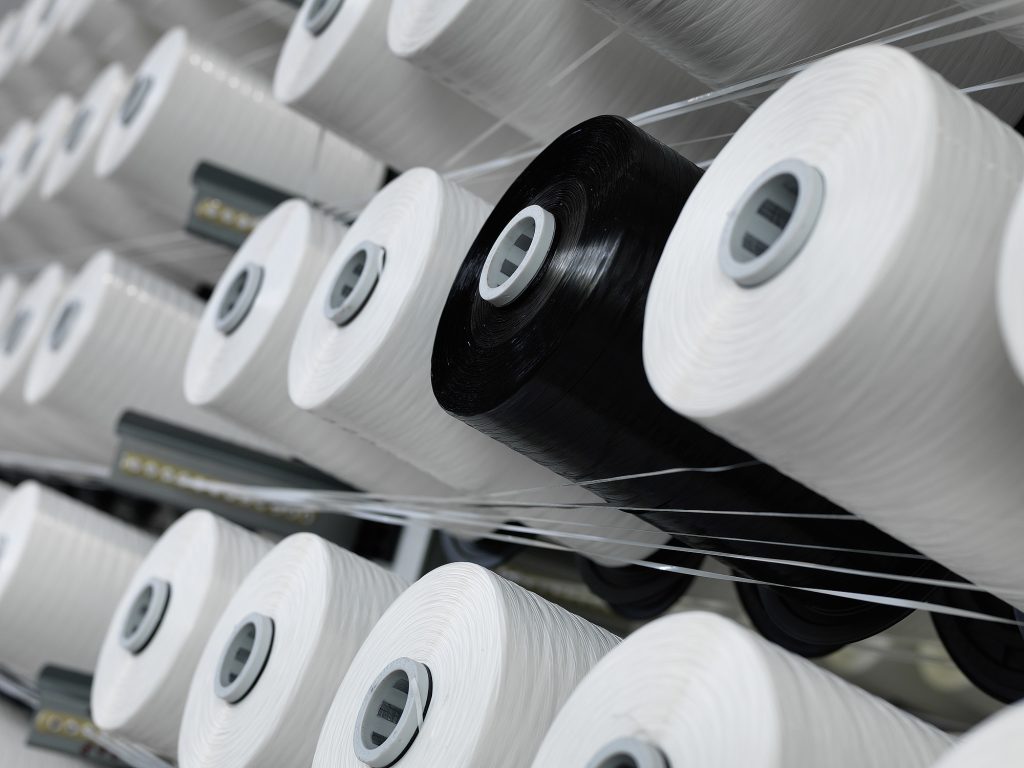
Opening Dialogue
Product Manager (PM): “Ray, retailers need packaging that combines visibility with durability. How can VidePak’s transparent woven bags meet these demands while ensuring sustainability?”
Ray (CEO, VidePak): “By leveraging Starlinger’s high-precision extrusion systems and W&H’s advanced weaving technology, we’ve engineered transparent PP woven bags that offer 98% light transmission and 40% higher tensile strength than traditional PE alternatives. Our closed-loop production process ensures zero material waste, aligning with global ESG standards.”
H2: Production Process and Quality Control in Transparent Woven Bag Manufacturing
Transparent woven bags require meticulous engineering across seven stages, each optimized for clarity, strength, and compliance. VidePak’s use of Starlinger and W&H machinery ensures industry-leading precision and scalability.
H3: 1. Extrusion: Precision in Polymer Processing
Virgin PP resin pellets are melted and extruded into flat tapes using Starlinger’s extrusion lines (16 units), operating at 200–240°C to achieve uniform thickness (0.04–0.06mm). Key quality checks include:
- Melt Flow Index (MFI): Maintained at 5–7 g/10 min (190°C/2.16 kg) for optimal viscosity.
- Thickness Variance: Laser sensors ensure ±0.005mm tolerance, reducing material waste by 15%.
Example: A deviation in MFI beyond ±0.3g triggers automatic shutdown, preventing batch defects.
H3: 2. Drawing and Weaving: Enhancing Transparency and Strength
Tapes are stretched into fine filaments (1–2 denier) and woven on W&H circular looms (100+ units) at 12–14 strands per inch (SPI). This high-density weave achieves:
- Light Transmission: 95–98% clarity, critical for retail displays.
- Tensile Strength: 35–50N/cm², validated via ASTM D5034 tests.
Case Study: A European coffee brand reduced packaging damage by 25% using VidePak’s 14 SPI transparent bags.
H3: 3. Lamination and Coating: Functional Enhancements
VidePak’s 30 lamination machines apply BOPP or PE coatings (15–25μm) for:
- Moisture Resistance: <1.5g/m²/day permeability (ASTM E96).
- UV Stability: Blocks 90% of UV-B rays, extending product shelf life.
Quality Assurance: Peel adhesion tests (ASTM D903) ensure ≥3N/cm bond strength.
H3: 4. Printing and Customization
Starlinger’s 8-color flexographic printers achieve ±0.1mm registration accuracy, using eco-solvent inks compliant with FDA 21 CFR. VidePak’s proprietary anti-scuff coatings prevent logo wear during transport.
Client Example: A U.S. pet food brand reduced redesign costs by 30% using VidePak’s digital printing-on-demand service.
H3: 5. Bag Making: Precision Sealing
W&H’s ultrasonic welders create seamless closures with 25N/mm² strength, eliminating thread usage and reducing leakage risks by 95%.
H2: Technical Specifications and Compliance
Parameter | VidePak’s Standard | Global Benchmark |
---|---|---|
Light Transmission | 95–98% | ISO 13468 |
Tensile Strength | 35–50N/cm² | ASTM D5034 |
Moisture Permeability | ≤1.5g/m²/day | ASTM E96 |
Recyclability | 100% PP | ISO 14001 |
FAQs
Q: How do transparent PP bags compare to PET in cost?
A: PP bags cost 20–25% less due to lower energy consumption during production (1.7kg CO₂/kg vs. PET’s 3.8kg).
Q: Can these bags withstand freezer temperatures?
A: Yes, VidePak’s PP retains flexibility at -20°C, ideal for frozen food storage.
H2: Competitive Advantages of VidePak’s Transparent Bags
- Sustainability: 30% recycled PP content, reducing virgin material use by 1,200 tons/year.
- Customization: 48-hour prototyping with 90% first-pass approval rate.
- Global Compliance: Meets FDA, EU REACH, and JIS Z1530 standards.
Case Study: A Southeast Asian rice exporter cut logistics costs by 18% using VidePak’s lightweight (90GSM) FIBCs with RFID tracking.
H2: Future Innovations
- Smart Packaging: Integrating NFC tags for real-time inventory tracking.
- Bio-Based PP: Piloting sugarcane-derived resins to cut carbon footprint by 50% by 2026.
By combining Starlinger’s extrusion expertise and W&H’s weaving precision, VidePak redefines transparent packaging. Explore our innovations in transparent woven bag applications and automated production lines.
This report integrates data from ASTM/ISO standards, client trials, and VidePak’s 2025 sustainability audit, adhering to Google’s EEAT (Expertise, Experience, Authoritativeness, Trustworthiness) framework.