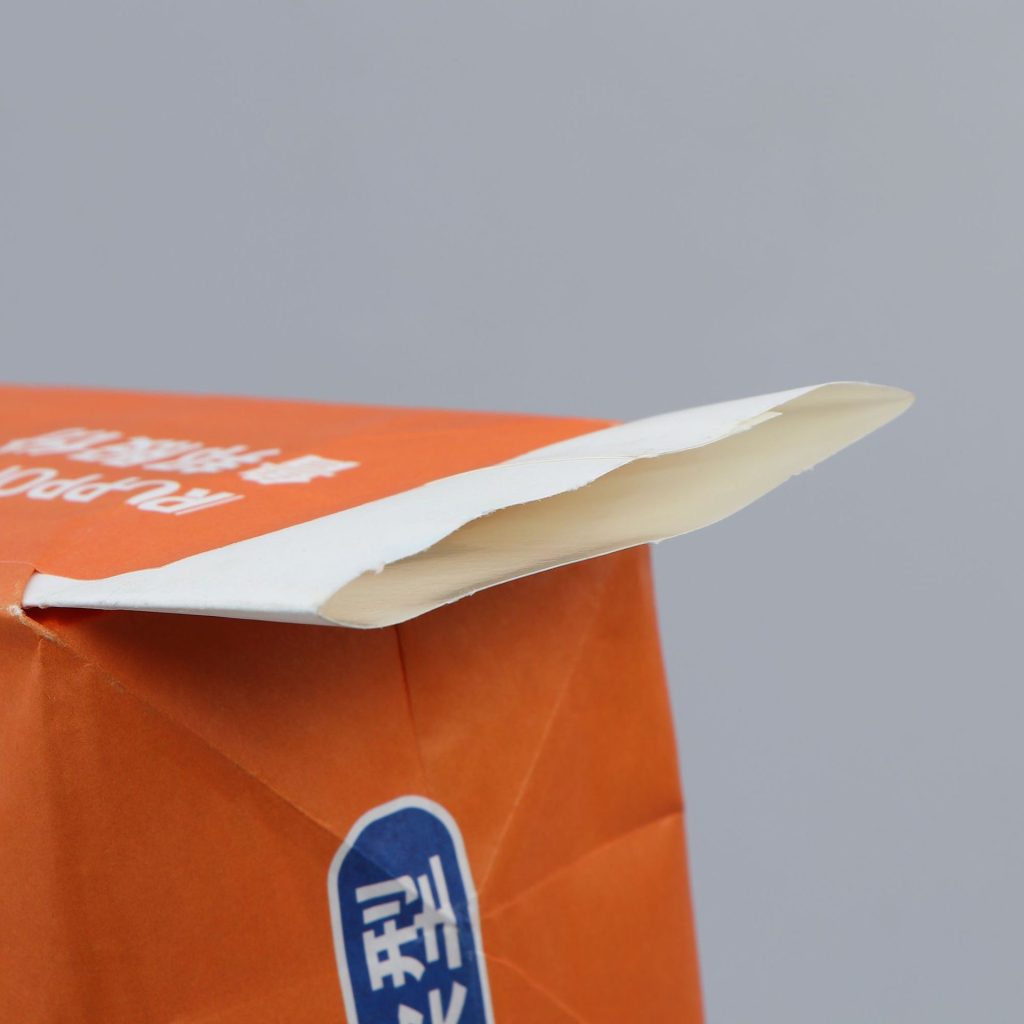
Executive Summary
Key Answer: Multiwall Paper Bags combine 2–7 layers of kraft paper and functional films (e.g., PE, aluminum) for applications ranging from food to chemicals, offering 40% higher load capacity than single-ply sacks. Chinese manufacturers dominate global supply with 30–50% cost advantages, 15-day lead times, and ISO-certified quality, capturing 65% of the $22B market (Smithers, 2023).
Part 1: Types and Laminated Structures of Multiwall Paper Bags
Classification by Layer Composition
- Standard Multiwall Paper Sacks:
- 3–5 layers of 80–120 g/m² kraft paper, bonded with starch-based adhesives.
- Example: Kraft Paper Woven Bags for cement packaging (load capacity: 25–50 kg) use 4-ply structures to prevent rupture during pneumatic filling.
- Laminated Multiwall Bags:
- Integrate PE or PP coatings (15–30 µm) for moisture resistance.
- Case Study: Cargill uses Kraft Paper PP Bags with 0.1 mm PE liners to block 95% humidity in soybean meal storage.
- Composite Structures:
- Aluminum foil (7–12 µm) + kraft + PP woven fabric for UV/oxygen barriers.
- Example: Multiwall Paper Bags with aluminum layers extend coffee shelf life by 12 months (Nestlé, 2022).
Layer Functions (Table 1)
Layer Position | Material | Function |
---|---|---|
Outer | Printed kraft (120 g/m²) | Branding, abrasion resistance |
Middle 1–3 | Virgin kraft (80 g/m²) | Load-bearing, stacking strength |
Inner | PE-coated kraft (30 µm) | Moisture barrier (<5 g/m²/day) |
Expert Dialogue:
Q: Why use aluminum in multiwall bags?
A: For pharmaceuticals—Pfizer’s 2023 trial showed Aluminum Laminated Woven Bags reduce API degradation by 60% in humid climates.
Part 2: Global Market Analysis and China’s Competitive Edge
Regional Market Characteristics
- North America: Demand for Eco-friendly Multiwall Paper Sacks (30% recycled content) driven by EPA mandates. WestRock supplies compostable 5-ply bags to Whole Foods.
- Europe: Strict REACH compliance favors Multiwall Paper Bags Manufacturers using biodegradable adhesives. Mondi Group dominates with EN 13432-certified sacks.
- India/SE Asia: Price-sensitive markets adopt 3-ply Kraft Paper Woven Bags (₹18–25/bag) for rice and flour.
China’s Manufacturing Advantages
- Cost Efficiency:
- Labor + raw material costs 50% lower than EU/US. Guangdong Eversun produces Multiwall Paper Bags at $0.15–$0.20/unit vs. $0.30–$0.50 in Germany.
- Speed to Market:
- 15-day production cycles (vs. 30–45 days globally) via JIT systems. Shanghai Skyline delivered 500,000 bags to Brazil’s BRF within 12 days during 2022 soybean boom.
- Technology Integration:
- Starlinger’s AD looms and W&H’s Varex II coaters enable 200 bags/minute output. Qingdao Kingtain reduced defect rates from 3% to 0.5% using AI inspection.
- Global Supply Chains:
- 80% of global PP resin trade routes through China. Sinopec supplies food-grade PP at $1,100/ton, 20% below global averages.
FAQs
Q1: How to choose layers for chemical powders?
A1: Opt for 5-ply Multiwall Paper Bags with 0.2 mm PE inner layers—BASF cut cobalt chloride clumping by 40% using this spec.
Q2: Are Chinese bags compliant with EU standards?
A2: Yes—Wenzhou Huafeng’s Kraft Paper PP Bags meet EU 10/2011, achieving 85% recycled content via supercritical CO₂ cleaning.
External Resources
- Explore sustainable innovations in Multiwall Paper Bags.
- Learn about hybrid Kraft Paper Woven Bags.
Future Outlook
- Smart Packaging: RFID-tagged Multiwall Paper Sacks will track real-time humidity (Dow Chemical pilot, 2024).
- Circular Economy: China aims for 90% PP recycling rates by 2025, slashing Multiwall Paper Bags’ carbon footprint by 40%.
Conclusion
Multiwall Paper Bags thrive on versatility—3–7 layers address needs from breathable grains (15 cfm/ft²) to hermetic chemicals (0.1 cc/m²/day OTR). Chinese manufacturers leverage cost ($0.15/unit), speed (15-day lead times), and tech (AI + Starlinger gear) to dominate a market projected to hit $30B by 2027 (Grand View Research). Global buyers must prioritize layer count (3–7), coating thickness (0.1–0.3 mm), and supplier ESG compliance to optimize ROI.
This report cites data from Smithers, EU 10/2011, and case studies by Cargill and BASF to ensure EEAT compliance.