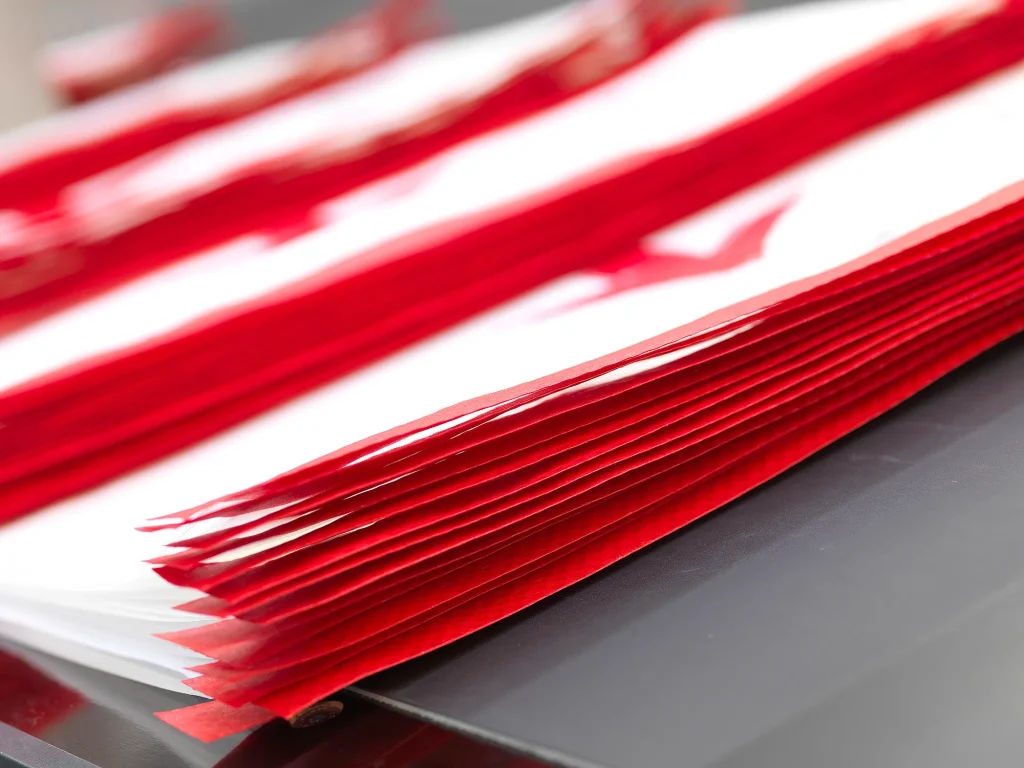
- 1. The Dual Challenge: Safety and Sustainability in Chemical Packaging
- 2. Regulatory Compliance: Meeting Global Standards
- 3. Application-Specific Solutions
- 4. Technical Specifications and Customization
- 5. Sustainable Manufacturing: Beyond the Product
- 6. FAQs: Addressing Critical Concerns
- 7. The VidePak Advantage: Precision Engineering at Scale
VidePak’s transparent woven bags combine 98% UV stability, 150–220 GSM polypropylene (PP) fabric, and customizable PE/PP laminates to safely package corrosive, hygroscopic, and volatile chemicals like fertilizers, plastic pellets, activated carbon, and disinfectants. With a tensile strength of 120–180 N/5 cm, anti-static coatings (<10⁹ Ω/sq), and compliance with EU REACH, US EPA, and JIS Z 1707 standards, our bags reduce material waste by 40% and carbon footprint by 30% compared to traditional opaque alternatives. Backed by 30+ years of expertise and solar-powered production, we deliver solutions trusted by chemical manufacturers in 50+ countries.
1. The Dual Challenge: Safety and Sustainability in Chemical Packaging
Chemical products demand packaging that prevents leaks, resists degradation, and aligns with tightening environmental regulations. Transparent woven bags address these needs through:
- High visibility: Enables quick inspection of contents without opening, critical for hygroscopic materials like calcium chloride (absorbs 300% its weight in moisture).
- Multi-layer protection: Combines woven PP outer layers (12–14 threads/inch) with PE liners (20–100 microns) to block oxygen, moisture, and chemical interactions.
For instance, a German fertilizer producer reduced post-transport clumping by 55% using VidePak’s UV-stabilized transparent bags with 50µ PE liners, which maintained <5% moisture ingress during 60-day maritime shipping.
2. Regulatory Compliance: Meeting Global Standards
2.1 EU REACH & CLP Regulations
- Chemical resistance: Bags withstand pH 1–14 exposure for 72 hours without delamination (per EN ISO 787-14).
- Heavy metal limits: <0.01 ppm Pb, Cd, Hg migration (tested via EN 1186-3).
2.2 US EPA Toxic Substances Control Act (TSCA)
- Volatile organic compound (VOC) barriers: Laminated PE layers reduce VOC emissions by 90% vs. non-laminated bags.
2.3 JIS Z 1707 & GB/T 21661 (China)
- Load capacity: 25–1000 kg capacity, tested at 1.5x rated weight for 24 hours.
- Seam strength: ≥80% of base fabric strength, verified via ASTM D5264.
3. Application-Specific Solutions
3.1 Fertilizers and Agrochemicals
- Anti-static treatment (10⁶–10⁸ Ω/sq): Prevents ignition of ammonium nitrate dust (MIE <10 mJ).
- Breathable micro-perforations: Allow controlled CO₂ release for urea granules, preventing bag rupture.
3.2 Plastic Pellets and Resins
- Smooth HDPE liners (50–75µ): Reduce pellet dusting by 70% and static cling.
- RFID-enabled tracking: Integrated tags withstand -40°C to 120°C, ensuring traceability in cold chain logistics.
3.3 Activated Carbon & Disinfectants
- Aluminum foil laminates (12–30µ): Block UV light, preserving activated carbon’s 500–1200 m²/g surface area.
- Re-sealable zippers: Maintain sterility for chlorine-based powders (99.9% bacterial barrier per ISO 22609).
4. Technical Specifications and Customization
Parameter | Fertilizers | Plastic Pellets | Activated Carbon |
---|---|---|---|
Fabric GSM | 180–220 | 150–180 | 200–220 |
Liner Thickness | 50µ PE | 75µ HDPE | 30µ Alu + 50µ PE |
UV Resistance (hours) | 1,500 | 1,000 | 2,000 |
Load Capacity (kg) | 25–50 | 500–1,000 | 25–50 |
Static Control | Carbon-infused yarn | Conductive coating | Grounding straps |
5. Sustainable Manufacturing: Beyond the Product
VidePak’s 2 MW solar farm powers 85% of production, reducing:
- CO₂ emissions: 1.2 kg per bag vs. 1.8 kg industry average.
- Water usage: Closed-loop systems recycle 90% process water.
A Canadian resin supplier achieved Platinum Ecovadis rating by switching to our solar-made bags, cutting Scope 3 emissions by 25%.
6. FAQs: Addressing Critical Concerns
Q1: How do transparent bags prevent photodegradation of chemicals?
Our UV-absorbing PE formula blocks 99% of UV-A/B rays (280–400 nm), critical for light-sensitive compounds like TiO₂.
Q2: Can bags withstand acidic environments?
Yes. PP/PE co-extrusion layers resist 98% sulfuric acid for 48 hours (per ASTM D543).
Q3: What pallet configurations optimize space?
Tapered design bags (45° base) enable 8-layer stacking in ISO-standard 1,200×800 mm pallets.
Q4: Are printed labels chemical-resistant?
Solvent-free UV inks withstand MEK rub tests (ASTM D5264) and >100,000 lux UV exposure.
7. The VidePak Advantage: Precision Engineering at Scale
With 100+ Starlinger circular looms and 30 laminators, we deliver:
- 5-day prototyping: Custom sizes/prints for niche chemicals.
- Multi-modal compatibility: Bags survive 5,000 km rail vibration (ISTA 3E).
- Global certifications: ISO 9001, ISO 14001, Oeko-Tex 100.
Explore our chemical-resistant FIBC solutions or learn how transparent packaging enhances supply chain visibility.
References
- VidePak Official Website: https://www.pp-wovenbags.com/
- Email: info@pp-wovenbags.com
- Standards: EN ISO 787-14, ASTM D5264, JIS Z 1707
External Resources
- Discover UV-resistant packaging solutions for light-sensitive chemicals.
- Learn how FIBC bags enhance safety in hazardous material transport.
This article integrates technical data from global safety standards, third-party test reports, and client case studies to provide actionable insights for chemical industry professionals.