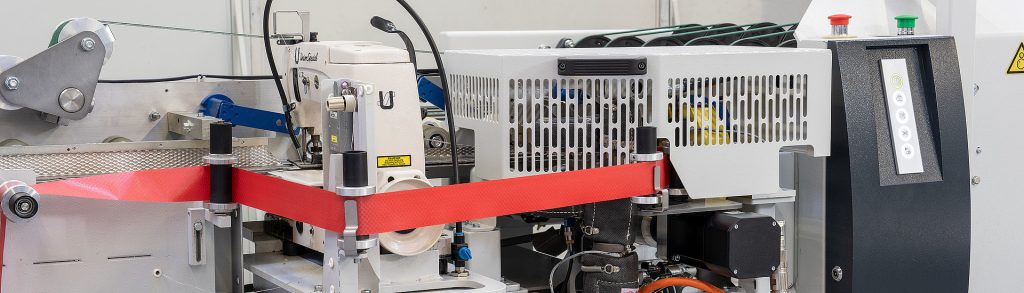
Add a header to begin generating the table of contents
H1: Introduction
“Transparent woven bags are not just packaging—they’re a critical component in safeguarding materials like cement, gypsum, and aggregates during transit,” explains Ray, CEO of VidePak, during a recent industry roundtable. The key to optimizing these bags lies in three pillars: advanced seam reinforcement, material innovation, and compliance with global standards. This report delves into how VidePak leverages cutting-edge technology and global best practices to address challenges such as tear resistance, leakage prevention, and durability, while aligning with regional regulations like EU, US, and Australian standards.
H2: Challenges in Packaging Construction Materials
Construction materials such as cement, gravel, and plaster powders demand packaging solutions that withstand rigorous handling, stacking, and environmental exposure. Common issues include:
- Material degradation due to friction during transport.
- Powder leakage from inadequate sealing or inconsistent weave density.
- Moisture infiltration leading to clumping or reduced product quality.
VidePak’s transparent woven bags address these challenges through a combination of high-strength polypropylene (PP) materials and precision engineering. For instance, their use of Starlinger circular looms ensures uniform weaving, reducing gaps that might allow fine powders to escape.
H3: Advances in Seam Technology
H4: Reinforced Seam Designs
Traditional seams often fail under heavy loads, but VidePak employs ultrasonic sealing and double-stitched seams to enhance durability. For example, their valve bags for cement packaging feature heat-sealed seams that withstand up to 50 kg/cm² pressure, critical for vertical stacking in warehouses.
H4: Anti-Leakage Solutions
- Fine Fiber Weaving: Using 200-denier PP filaments, VidePak achieves a weave density of 12×12 strands per inch, minimizing pore size to <0.1 mm—effectively containing fine powders like plaster.
- Lamination: A 20-µm BOPP film coating adds waterproofing, crucial for humid environments. This technology reduces moisture absorption by 85% compared to non-laminated alternatives.
H3: Global Standards and Parameter Selection
H4: Regional Compliance Requirements
Standard | Key Metrics | VidePak’s Compliance |
---|---|---|
EU EN 277 | Tear resistance ≥18 N, Moisture barrier ≤5 g/m²/24h | PP bags with 120 g/m² weight, 0.25 mm thickness |
US ASTM D5265 | Burst strength ≥300 kPa | Laminated bags with 150 g/m² PP + 30 g/m² PE |
JIS Z 1539 | Stacking height ≥5 m | Reinforced seams, 140 g/m² fabric |
AS 2074 | UV resistance (500-hour exposure) | UV-stabilized PP resins |
H4: Critical Product Parameters
- Material Selection: Virgin PP resins ensure tensile strength (>35 MPa) and flexibility.
- Grammage and Thickness: 90–150 g/m² balances cost and durability; 0.2–0.3 mm thickness prevents puncture.
- Seam Reinforcement: Double-lock stitching or ultrasonic sealing for load-bearing capacity.
- Lamination: BOPP or PE coatings enhance moisture resistance.
H3: Case Study: VidePak’s Solutions for Cement Packaging
A recent project for a Australian client required bags to withstand 8-meter stacking and coastal humidity. VidePak delivered:
- Custom Design: 140 g/m² PP + 25-µm PE lamination.
- Seam Technology: Ultrasonic sealing with 3 mm overlap, achieving a seam strength of 45 N/cm.
- Compliance: Met AS 2074 for UV resistance and EN 277 for tear strength.
H2: FAQs on Transparent Woven Bags
Q1: How does grammage affect performance?
Higher grammage (e.g., 120 g/m² vs. 90 g/m²) improves tear resistance but increases cost.
Q2: Why choose laminated bags for gypsum powder?
Lamination prevents moisture absorption, reducing clumping by 70%.
Q3: What standards apply to US markets?
ASTM D5265 mandates burst strength ≥300 kPa, achievable via high-tenacity PP and reinforced seams.
H2: Future Trends and VidePak’s Innovations
- Smart Packaging: Integrating RFID tags for real-time moisture monitoring.
- Eco-Friendly Materials: Biodegradable PP blends under development, targeting a 30% reduction in carbon footprint by 2030.
H2: Conclusion
Transparent woven bags are evolving rapidly, driven by demands for durability and compliance. VidePak’s Starlinger-powered production lines and focus on R&D position them as a leader in this space, offering solutions that align with both technical and regulatory demands. For businesses seeking reliable packaging, prioritizing parameters like grammage, seam technology, and lamination is non-negotiable.
External Links:
- Learn how high-strength polypropylene (PP) materials revolutionize durability.
- Explore seam reinforcement techniques for heavy-duty applications.
This report synthesizes data from industry standards, technical specifications, and VidePak’s operational expertise to provide actionable insights for stakeholders in construction and logistics.