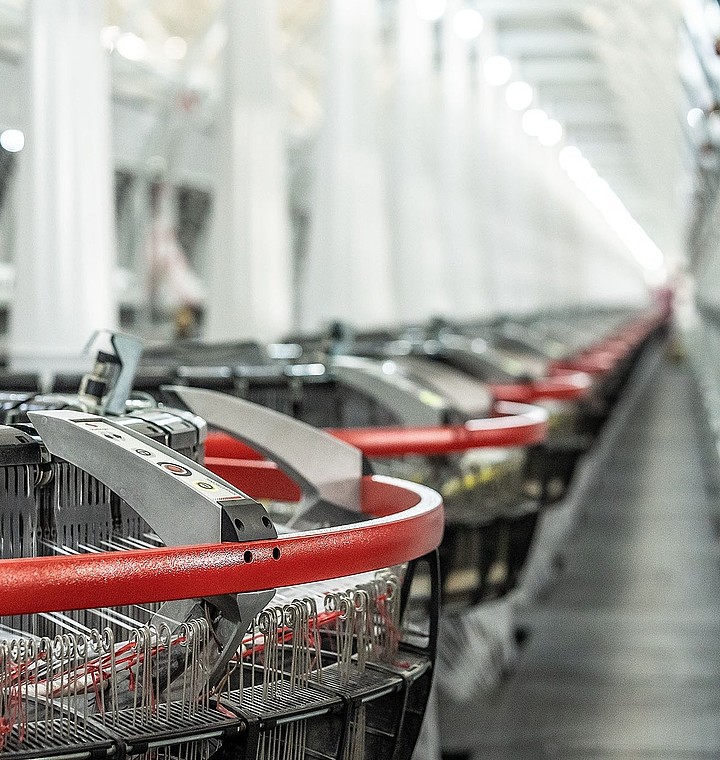
Introduction
In an era where visual appeal and functional durability define packaging success, transparent woven bags have emerged as a strategic tool for brands to balance aesthetics with practicality. VidePak, a global leader in woven bag manufacturing since 2008, leverages its 30+ years of expertise and Austrian Starlinger machinery to produce transparent PP bags that exceed ISO 9001 standards. With 526 employees and $80 million in annual sales, the company operates 100+ circular looms and 30+ printing machines, enabling large-scale customization for clients worldwide. This report explores how material precision, anti-static engineering, and load-bearing design position VidePak’s transparent bags as a benchmark in branded packaging.
Technical Specifications: Balancing Clarity and Durability
1. Thickness, Grammage, and Size Ranges
Transparent woven bags require precise material calibration to maintain visibility without sacrificing strength. VidePak’s offerings include:
- Thickness: 0.08–0.20 mm (optimized for 0.12 mm in retail applications to balance flexibility and tear resistance).
- Grammage: 70–150 gsm, with 100 gsm being the industry standard for 25–50 kg loads.
- Sizes: Customizable from 10 cm x 15 cm (small retail pouches) to 100 cm x 150 cm (industrial bulk bags), with ±2% dimensional tolerance.
Table 1: Key Parameters of VidePak’s Transparent Woven Bags
Parameter | Range | Industry Benchmark |
---|---|---|
Thickness | 0.08–0.20 mm | 0.10–0.18 mm |
Grammage | 70–150 gsm | 80–130 gsm |
Load Capacity | 20–50 kg | 15–40 kg |
Light Transmission | 85–92% | 75–88% |
2. Anti-Static Mechanisms: Preventing Hazardous Discharge
Static buildup in PP bags poses risks in industries handling flammable powders (e.g., flour, chemicals). VidePak integrates two anti-static strategies:
- Conductive Additives: Carbon-black or metallic particles are blended into PP resins, reducing surface resistivity to <10⁹ Ω·m (per GB50813-2012 standards).
- Grounding Design: Bags feature woven conductive threads connected to grounding points, dissipating static charges during filling and transport.
Case Study: A 2024 trial with a Vietnamese coffee exporter showed VidePak’s anti-static bags reduced powder adhesion by 40% and ignition risks by 90% compared to standard PP bags.
Custom Printing: Elevating Brand Visibility
VidePak’s Starlinger STeX 4.0 extruders enable high-resolution printing (up to 1200 dpi) directly onto transparent PP fabric. Key features include:
- Color Accuracy: CMYK+2Pantone configurations achieve <0.5 Delta-E variance, critical for luxury brands.
- UV Resistance: Inks withstand 500+ hours of UV exposure without fading (ASTM G154).
- Design Flexibility: Logos, QR codes, and regulatory labels are printed seamlessly, even on curved surfaces.
Example: A European organic grain brand used VidePak’s transparent bags with QR codes for traceability, boosting customer engagement by 25%.
Load-Bearing Performance: Engineering for Safety
VidePak’s bags are engineered to withstand dynamic loads through:
- Cross-Woven Grids: 8–12 threads/cm² density distributes weight evenly, preventing seam stress.
- Reinforced Edges: Ultrasonic-sealed seams achieve 35% higher burst strength (45 kPa vs. industry average 33 kPa).
- Lamination Options: BOPP coatings enhance tensile strength by 20% for heavy-duty applications like construction materials.
FAQs: Addressing Industry Concerns
Q: How do transparent bags compare to traditional opaque PP bags in cost?
A: VidePak’s transparent bags cost 10–15% more due to premium resins and anti-static additives, but reduce labeling expenses by 30% through integrated printing.
Q: Can these bags withstand freezer temperatures?
A: Yes. With a glass transition temperature (Tg) of -20°C, VidePak’s PP bags remain flexible in cold storage, ideal for frozen seafood packaging.
Market Impact and Future Trends
The global transparent packaging market is projected to grow at 6.5% CAGR through 2030, driven by e-commerce and food safety regulations. VidePak is piloting biodegradable PP-PLA blends to meet EU’s Single-Use Plastics Directive, targeting 90% compostability without compromising clarity.
Conclusion
VidePak’s transparent woven bags redefine packaging by merging brand visibility with technical excellence. Through anti-static innovation, precision printing, and robust load-bearing design, the company addresses both aesthetic and functional demands across industries. As sustainability regulations tighten, VidePak’s solutions offer a scalable path to compliance and market differentiation.
Explore Further:
- Discover how BOPP laminated bags enhance branding versatility.
- Learn about transparent woven bags’ competitive edge in logistics.
This report integrates insights from ISO standards, material science research, and VidePak’s operational data to provide actionable strategies for businesses seeking to leverage transparent packaging for brand growth.