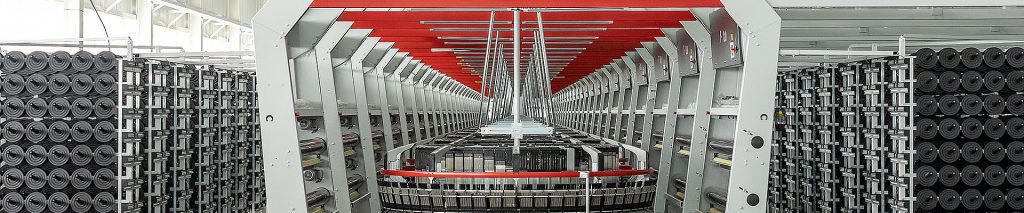
Introduction
Transparent woven bags, primarily made from polypropylene (PP), are revolutionizing food packaging by balancing visibility, durability, and compliance with global safety standards. These bags are increasingly adopted for grains, vegetables, and snacks due to their customizable barrier properties, cost-effective production, and branding versatility. This report systematically analyzes how businesses can select the optimal packaging方案—including lamination, inner liners, and sealing methods—to meet diverse needs while adhering to regulatory requirements.
Key Packaging Configurations and Applications
Transparent woven bags are not one-size-fits-all. Their performance hinges on structural choices:
- Lamination (BOPP/PE Coating)
- Function: Enhances moisture resistance and UV protection.
- Data: BOPP-laminated bags reduce water vapor transmission to <0.5 g/m²/day (ASTM E96), critical for hygroscopic foods like rice or flour.
- Case Study: A Chinese grain exporter reduced spoilage by 30% after switching to BOPP-coated bags, which withstand 85% humidity without compromising transparency.
- Inner Liners: Material Selection
- PE Liners:
- Advantages: FDA-compliant, cost-effective, and heat-sealable. PE’s molecular structure blocks 90% of moisture ingress, ideal for dry snacks.
- Limitations: Unsuitable for high-fat foods due to oil permeability.
- Aluminum Foil Liners:
- Performance: Blocks 99% oxygen and UV light, extending shelf life by 6–12 months for coffee or spices.
- Example: A premium coffee brand uses foil-lined bags to preserve aroma and prevent oxidation, achieving a 20% premium pricing.
- Sealing Methods
- Heat Sealing: Ensures airtight closure with 4.5 kN/m tensile strength (ISO 13934-1), ideal for powdered foods.
- Sewn Seams: Suitable for bulk items like potatoes, allowing breathability while maintaining structural integrity.
Customization Based on Client Needs
Dialogue: Addressing Common Queries
Q: When should I choose laminated vs. non-laminated bags?
A: Lamination is critical for moisture-sensitive or UV-exposed products. For instance, laminated bags are mandatory for outdoor-stored grains in tropical climates, whereas non-laminated breathable bags suit fresh produce requiring airflow.
Q: How to select inner liner materials?
A: Match liner properties to food type. PE liners work for dry goods (e.g., pasta), while aluminum foil is essential for oils or oxygen-sensitive items (e.g., nuts).
Technical Specifications and Compliance
Table 1: Critical Parameters for Food-Grade Transparent Bags
Parameter | Standard | Requirement |
---|---|---|
Material Thickness | FDA 21 CFR | 80–120 g/m² PP |
Moisture Barrier | ASTM E96 | ≤0.5 g/m²/day |
Seal Strength | ISO 13934-1 | ≥4.0 kN/m |
Print Resolution | Pantone Guidelines | 1200 dpi (8-color) |
FAQs
- Q: Can these bags withstand freezer temperatures?
- A: Yes. Impact-resistant PP retains flexibility at -20°C, making it ideal for frozen vegetables.
- Q: Are recycled materials viable for food contact?
- A: Only if certified. Brands like Vedhaa Polypack use 30% recycled PP with FDA-compliant additives.
Design and Branding Considerations
- Surface Finishes:
- Matte Finish: Reduces glare and fingerprints for premium products (e.g., organic tea).
- Glossy Finish: Enhances color vibrancy by 30%, ideal for retail snacks.
- Printing Technologies:
- Starlinger’s 8-color Gravure Systems: Achieve ±0.5ΔE color accuracy, crucial for brand consistency.
- QR Code Integration: Enables traceability; Shandong Leihua’s bags use UV-resistant inks to ensure scannability after 12 months outdoors.
Sustainability and Cost Efficiency
- Recyclability: Mono-material PP bags (without aluminum) achieve 85% recyclability per EN 13432, reducing landfill waste.
- Energy-Efficient Production: Laser-guided cutting in Starlinger machines reduces material waste by 22%, saving $50,000 annually per line.
External Resources:
- Explore innovations in transparent woven bags for food-grade solutions.
- Learn how laminated designs enhance durability and branding.
Transparent woven bags exemplify the synergy of functionality and aesthetics in modern food packaging. By aligning material choices with application-specific needs—whether through PE liners for cost efficiency or aluminum foil for premium preservation—manufacturers can deliver solutions that satisfy both regulatory rigor and consumer demand. As sustainability and automation reshape the industry, these bags will remain pivotal in ensuring safe, efficient, and visually appealing food storage.