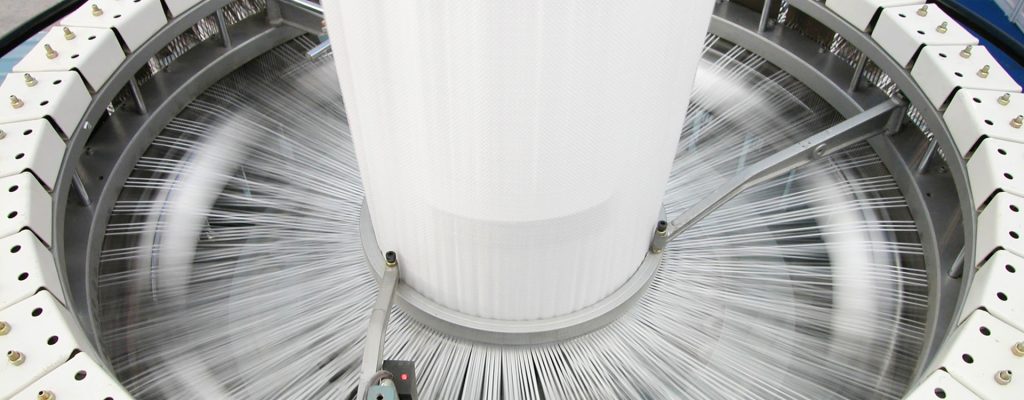
Tubular Woven Bags (TWBs) with Form-Fill-Seal (FFS) systems have revolutionized the retail and grocery packaging industries by improving packaging speed, efficiency, and quality. These bags are now used in a wide variety of sectors, from food and agricultural products to pet food packaging. In this article, we’ll explore how this innovative packaging solution has transformed the market, with a focus on technological advancements, material innovations, and cost-control benefits. We’ll also take a look at the future of these systems, including automation trends.
What Are Tubular Woven Bags (TWBs) with FFS Systems?
Tubular Woven Bags are made from polypropylene (PP) fibers woven into a tubular shape. These bags are strong, lightweight, and ideal for packing bulk goods like grains, fertilizers, and pet food. When combined with a Form-Fill-Seal (FFS) system, they become even more efficient. The FFS system automates the entire process of forming the bag, filling it with product, and sealing it, resulting in faster production times, higher precision, and less human error.
How FFS Technology Works and Its Benefits
FFS technology is a game-changer for packaging. It automates the entire process from start to finish, improving speed and accuracy. For example, the system can form up to 300 bags per minute, making it ideal for industries with high-volume packaging needs, such as retail and grocery stores.
One of the key benefits of FFS systems is precision. Traditional packaging methods involve manual labor, which can result in inconsistent bag sizes or incorrect weight measurements. With the FFS system, manufacturers can ensure each bag is the correct size and weight, reducing packaging errors and ensuring the quality of each product.
Example: A large-scale grocery chain that switched to TWBs with FFS systems was able to increase its production speed by 50%. This was a significant boost for their business, enabling them to meet growing demand while maintaining consistent quality across their packaging.
Material Innovations in Tubular Woven Bags
The material used in TWBs is another area where innovation has made a significant impact. Initially, these bags were made from simple polypropylene fibers, but today, they are often enhanced with additional materials that improve performance.
- Multi-layer Laminates: Many TWBs are now produced with multi-layer laminates, combining polypropylene with polyethylene (PE) or BOPP (Biaxially Oriented Polypropylene) films. This adds an extra layer of protection against moisture, making the bags more durable and suitable for sensitive products like food or fertilizers.
- Eco-friendly Materials: With increasing pressure to adopt sustainable practices, some manufacturers are now using biodegradable materials or recycled polypropylene in their TWBs. These innovations help reduce environmental impact while maintaining the strength and functionality of the bags.
Example: A pet food company recently transitioned to multi-layer laminated TWBs for its packaging. This not only extended the shelf life of the products by 15%, but also reduced the risk of contamination, ensuring a higher quality product for consumers.
Cost Control and Efficiency with FFS Systems
One of the biggest advantages of TWBs with FFS systems is the significant cost savings they offer. The automation of the entire packaging process reduces the need for manual labor, which can be expensive and time-consuming.
- Reduced Labor Costs: With FFS systems, human labor is minimized, as the machines do all the work. This leads to lower operational costs and faster production times.
- Less Material Waste: The FFS system allows for precise control over the amount of material used in each bag. This reduces excess waste and ensures that manufacturers are getting the most out of their raw materials.
Example: A large retailer switched to using FFS systems with tubular woven bags and saw a 25% reduction in labor costs. Additionally, the precise material control helped them reduce waste by 10%, making the entire process more cost-effective.
Future Trends: Automation and Smart Packaging
Looking ahead, the future of TWBs with FFS systems is closely tied to advancements in automation and smart packaging. As technology improves, we can expect even greater efficiency and sustainability in packaging solutions.
- Automation: In the future, we may see even more automation in the packaging process. With the rise of AI and machine learning, FFS systems will become smarter, adapting to production needs in real-time and reducing the chance of errors.
- Smart Packaging: Another trend is the integration of smart features, such as sensors and RFID tags, into the packaging. This will allow manufacturers to track products throughout the supply chain, ensuring better inventory management and reducing losses due to spoilage or theft.
- Sustainability: As consumers become more eco-conscious, the demand for sustainable packaging will continue to rise. Future innovations may include fully biodegradable TWBs or bags made from 100% recycled materials, helping companies meet environmental standards.
Example: A major grocery chain is already piloting smart packaging with embedded sensors that track product freshness. This technology helps them ensure the products remain fresh until they reach consumers, providing a better customer experience and reducing waste.
Key Features and Specifications of TWBs with FFS Systems
Feature | Specification | Benefit |
---|---|---|
Material | Polypropylene, BOPP, PE laminates, biodegradable options | Durability, moisture resistance, and sustainability. |
Sealing Technology | Ultrasonic sealing, heat sealing | Ensures leak-proof and secure packaging. |
Customization | Size, shape, and printing options | Flexibility for branding and diverse applications. |
Speed | Up to 300 bags per minute | Increased production speed and reduced costs. |
Automation Level | Fully automated systems | Reduces labor costs and material waste. |
FAQs
Q1: How do TWBs with FFS systems differ from traditional packaging methods?
Traditional methods often rely on manual labor, which can be slow and prone to errors. TWBs with FFS systems automate the packaging process, improving speed, accuracy, and consistency.
Q2: Are TWBs with FFS systems more sustainable?
Yes, many TWBs are made with recyclable or biodegradable materials, and the efficiency of FFS systems reduces material waste, contributing to a more sustainable packaging solution.
Q3: What industries benefit most from TWBs with FFS systems?
TWBs with FFS systems are ideal for high-volume industries like grocery, retail, agriculture, and pet food packaging, where speed, consistency, and cost-effectiveness are critical.
Conclusion
Tubular Woven Bags with Form-Fill-Seal (FFS) systems have transformed the packaging industry by making it faster, more efficient, and more cost-effective. With technological advancements, improved materials, and the rise of automation, these systems are set to play an even larger role in the future of retail and grocery packaging. As sustainability becomes more important, the industry will continue to innovate, offering even more eco-friendly and efficient packaging solutions.
For more information on the benefits of FFS woven bags and the future of sustainable woven packaging, check out these additional resources.