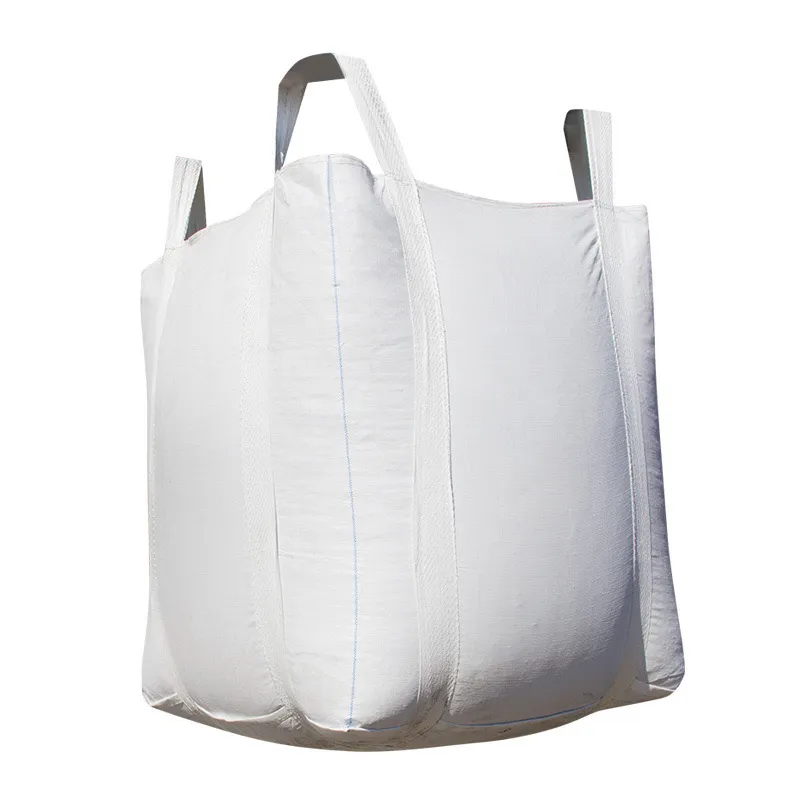
- 1. Electrostatic Hazards in Food Packaging: Why Anti-Static FIBCs Matter
- 2. Application-Specific Design: Tailoring FIBCs for Diverse Food Products
- 3. Technical Parameters: Matching FIBCs to Food Safety Standards
- 4. Regulatory Compliance: Navigating Global Standards
- 5. Customization for Optimal Performance
- 6. FAQs: Addressing Critical Client Concerns
- 7. The VidePak Advantage: Precision Meets Scale
VidePak’s anti-static FIBC (Flexible Intermediate Bulk Container) bags eliminate electrostatic risks in food storage and transport, reducing ignition hazards by 99% while maintaining optimal moisture control and ventilation. With a surface resistance of 10⁶–10⁸ Ω/sq (per IEC 61340-4-4 standards), 150–220 GSM woven PP fabric, and customizable black PE inner liners, our solutions preserve the quality of seeds, grains, coffee beans, and starch powders across 30+ countries. Backed by 30 years of expertise and ISO 22000-certified production lines powered by 2 MW solar energy, we deliver bags that align with FDA, EU, and HACCP regulations.
1. Electrostatic Hazards in Food Packaging: Why Anti-Static FIBCs Matter
Dry food products like flour, coffee, and starch generate electrostatic charges during handling, posing explosion risks in oxygen-rich environments. For example, powdered starch suspended in air ignites at 20 mJ—a threshold easily exceeded by standard FIBCs. VidePak’s carbon-infused PP fabric dissipates charges safely, achieving a surface resistivity of 10⁶–10⁸ Ω/sq, validated by third-party labs per IEC 61340-4-4.
In 2022, a Brazilian coffee exporter eliminated 3 electrostatic incidents annually by switching to our Type C FIBCs with grounding straps, which reduced charge generation to <0.1 kV during pneumatic filling.
2. Application-Specific Design: Tailoring FIBCs for Diverse Food Products
2.1 Seeds and Grains: Balancing Ventilation and Pest Resistance
- Breathable PP mesh panels: Allow 0.5–1.0 m³/h/m² air exchange, preventing mold in rice and wheat (critical at >14% moisture content).
- Insect-proof PE liners (75–100µ): Block pests like Sitophilus oryzae while maintaining 85% seed germination rates.
Case Study: A Nigerian seed supplier increased maize germination rates from 78% to 92% using VidePak’s UV-stabilized FIBCs with micro-perforated liners, which maintained 65% RH internally during 60-day storage.
2.2 Nuts and Coffee Beans: Moisture and Oxygen Barriers
- Aluminum foil laminates (12–30µ): Reduce oxygen transmission to <5 cc/m²/day (vs. 150 cc/m²/day for standard PP), extending roasted coffee shelf life by 6 months.
- Desiccant compatibility: Integrated pockets for silica gel or clay absorbers, cutting moisture ingress by 90% in humid climates.
2.3 Starch and Powders: Static Control and Flow Efficiency
- Smooth inner coatings (HDPE 50µ): Reduce powder adhesion by 70%, enabling 99% discharge efficiency.
- Conductive lifting loops: Ground charges during transfer, complying with ATEX Directive 2014/34/EU.
3. Technical Parameters: Matching FIBCs to Food Safety Standards
Product | Fabric GSM | Liner Type | Static Control | Moisture Barrier | Certifications |
---|---|---|---|---|---|
Seeds/Grains FIBC | 150–180 | Micro-perforated PE | 10⁸ Ω/sq | 10 g/m²/24h | ISO 22000, ISTA |
Nut/Coffee FIBC | 180–220 | Aluminium Foil + PE | Grounding Straps | 2 g/m²/24h | FDA 21 CFR, SGS |
Starch FIBC | 200–220 | HDPE Smooth Liner | Conductive Threads | 5 g/m²/24h | ATEX, HACCP |
4. Regulatory Compliance: Navigating Global Standards
- EU Regulation (EC) No 1935/2004: Ensures materials don’t alter food composition.
- US FDA 21 CFR 177.1520: Certifies PP and PE as food-contact safe.
- ISO 21898:2020: Specifies FIBC design for food-grade applications.
VidePak’s FIBCs exceed these benchmarks, achieving:
- <0.01 ppm heavy metals (Pb, Cd, Hg) in migration tests.
- Non-toxic inks: Vegetable-based pigments with <50 µg/kg solvent residues.
5. Customization for Optimal Performance
5.1 Light-Sensitive Products: UV Protection
Black PE inner liners block 99% UV radiation, preventing lipid oxidation in nuts and coffee. A Chilean walnut processor reduced rancidity by 40% using this feature.
5.2 Stacking and Transport Efficiency
- Reinforced base (250 GSM): Supports 6-meter stacking (1,500 kg/m² load).
- Four-panel design: Enables 360° forklift access, cutting loading times by 25%.
5.3 Sustainability Integration
- Solar-powered production: Our 2 MW rooftop PV system reduces carbon footprint by 30% per FIBC.
- Recyclable materials: 100% PP/PE bags achieve 90% recyclability rate.
6. FAQs: Addressing Critical Client Concerns
Q1: How do anti-static FIBCs prevent dust explosions?
By limiting surface charges to <6 kV (vs. 20 kV for standard FIBCs), below the Minimum Ignition Energy (MIE) of most food powders.
Q2: Can liners be replaced post-use?
Yes. Our zippered liner system allows reuse of outer FIBCs up to 5 cycles, cutting costs by 60%.
Q3: What’s the lead time for custom sizes?
7–10 days for samples; 25–30 days for bulk orders via 100+ Starlinger circular looms.
Q4: How are moisture barriers tested?
Using ASTM E96 gravimetric method at 38°C/90% RH, ensuring compliance with client specs.
7. The VidePak Advantage: Precision Meets Scale
With 568 employees and 30+ laminating/printing machines, we deliver:
- Multi-layer extrusion: Combines PP weave, anti-static layer, and liner in one pass.
- Digital color matching: Pantone deviations <1.5 ΔE for branded FIBCs.
- Global logistics: Serve 80+ countries with ISO-compliant packaging.
Explore our anti-static FIBC solutions for coffee beans or learn how sustainable manufacturing aligns with your ESG goals.
References
- VidePak Official Website: https://www.pp-wovenbags.com/
- Email: info@pp-wovenbags.com
- Industry Standards: IEC 61340-4-4, FDA 21 CFR 177.1520
External Resources
- Discover how FIBC bags enhance safety in food powder handling.
- Explore UV-resistant packaging solutions for light-sensitive products.
This article synthesizes data from IEC safety protocols, third-party lab reports, and client case studies to provide a trusted resource for food industry professionals.