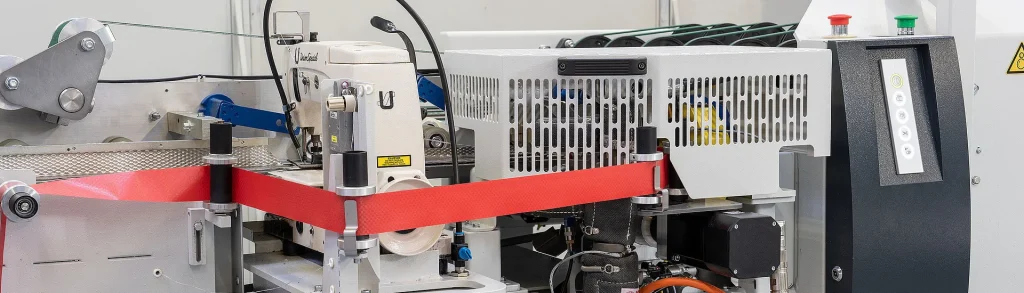
In today’s fast-paced industrial environment, the demand for high-quality packaging solutions, such as PP Woven Fabric Bags, has skyrocketed. These bags, often referred to as PP Woven sacks, are essential for transporting various goods efficiently. However, manufacturers must address significant quality issues to ensure customer satisfaction and operational efficiency. One of the most severe problems faced by the industry is the phenomenon of bag bursting, commonly known as “炸包.” This article will explore the underlying reasons for bag bursting, analyzing factors related to raw materials and finished product testing. It will also highlight how VidePak mitigates this issue through rigorous quality control processes.
The Threat of Bag Bursting
Bag bursting is a critical quality issue that can lead to significant financial losses for manufacturers and customers alike. When a PP Woven Sack bursts during handling or transportation, it compromises the integrity of the product contained within, leading to potential contamination, waste, and dissatisfied customers. Understanding why this occurs is essential to implementing effective preventive measures.
Factors Contributing to Bag Bursting
- Raw Material Quality
The quality of raw materials is a fundamental factor influencing the performance of PP Bags. The primary material used in the production of Polypropylene Bags is polypropylene resin, which is responsible for the bags’ strength, flexibility, and durability. Several issues related to raw materials can lead to bag bursting:
- Impurities: Contaminants in the resin, such as dirt or foreign particles, can weaken the structural integrity of the bag, making it more prone to bursting.
- Inadequate Material Specifications: Using low-quality or improperly graded polypropylene can result in bags that do not meet required standards for tensile strength and puncture resistance.
- Improper Mixing and Processing: Inconsistent processing techniques can lead to variations in the physical properties of the material, resulting in weak points within the fabric.
- Finished Product Testing
Comprehensive testing of PP Woven Sacks is crucial to ensure they meet safety and performance standards. The following tests are typically conducted: Test Type Purpose Acceptable Standards Thickness Measurement Ensures the bag meets the required thickness for durability. Varies by product specification Tensile Strength Test Assesses the bag’s resistance to being pulled apart. Minimum of 25-35 MPa UV Resistance Test Evaluates the bag’s ability to withstand ultraviolet rays, which can degrade materials. Minimum of 500 hours of exposure Drop Test Simulates real-life handling conditions to evaluate puncture resistance. Must withstand a drop of 1.5 meters Visual Inspection Checks for any defects, such as uneven weaving or material inconsistencies. No visible defects By implementing rigorous testing protocols, manufacturers can identify potential weaknesses in their products before they reach customers, significantly reducing the likelihood of bag bursting.
VidePak’s Quality Control Measures
At VidePak, we pride ourselves on our comprehensive quality management system that aims to minimize the risk of bag bursting. Our approach encompasses every aspect of the production process, from raw material selection to final product delivery.
- Strict Raw Material Selection
We partner with reputable suppliers to ensure that only the highest quality polypropylene resin is used in our production processes. Each batch of raw material undergoes thorough testing to confirm its purity and compliance with industry standards. - In-House Quality Testing
Our dedicated quality assurance team performs in-house testing on all incoming materials. Each batch is subjected to rigorous assessments, including tensile strength tests and impurity checks. This ensures that only materials that meet our stringent standards are used in production. - Production Process Monitoring
Continuous monitoring of our manufacturing processes helps maintain consistency and quality. Our state-of-the-art equipment, sourced from global leaders such as Starlinger, enables us to produce bags that adhere to the highest quality benchmarks. Automated systems reduce the risk of human error, ensuring that every bag produced is of optimal quality. - Final Product Inspections
Once the bags are produced, they undergo multiple inspections to guarantee their integrity. Our quality control personnel conduct thorough visual inspections and mechanical testing, including drop tests and tensile strength evaluations, to ensure that every batch of bags meets our specifications. - Customer Feedback Loop
We actively solicit feedback from our customers regarding the performance of our bags. Any reports of issues, such as bag bursting, are investigated thoroughly. This feedback loop allows us to identify areas for improvement and continually refine our quality control processes.
Conclusion
The prevention of bag bursting in PP Woven Fabric Bags is a critical concern for manufacturers and customers alike. At VidePak, we are committed to producing high-quality PP Woven Sacks by implementing rigorous quality control measures throughout the production process. By focusing on raw material selection, extensive testing, and continuous process improvement, we strive to deliver packaging solutions that meet the highest industry standards. This commitment not only enhances our reputation but also ensures that our customers receive durable, reliable, and efficient packaging solutions for their diverse needs. To learn more about our comprehensive quality management system and the excellence of our products, explore our PP Woven Fabric Bags offerings.
By investing in quality and sustainability, we continue to lead the industry, providing innovative and efficient packaging solutions that cater to the evolving needs of our clients across various sectors.