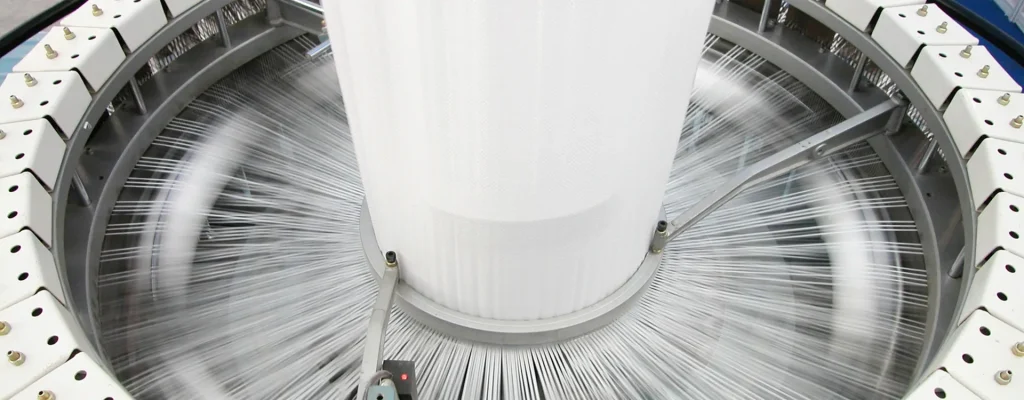
The primary answer this article provides is: Anti-bulge FIBC bags are engineered to prevent material expansion during storage and transport, ensuring structural integrity for sensitive food ingredients like flour, sugar, spices, and additives. Key selection criteria include load capacity (500–4,000 kg SWL), UV resistance, food-grade certifications (ISO, BRC), and customized liners (HDPE/LDPE) to meet diverse industry demands. VidePak’s 30+ years of expertise, Starlinger machinery, and 800+ global clients demonstrate our capability to deliver tailored solutions for bulk food packaging.
Introduction
In the fast-paced world of bulk food logistics, anti-bulge FIBC (Flexible Intermediate Bulk Container) bags are revolutionizing how manufacturers handle ingredients like flour, sugar, spices, and food additives. Unlike standard FIBCs, these bags incorporate reinforced designs to resist lateral pressure caused by granular shifts, preventing bulging and maintaining stackability. For industries requiring precise control over product integrity, selecting the right anti-bulge FIBC involves balancing load capacity, regulatory compliance, and environmental adaptability.
VidePak, founded in 2008 by CEO Ray, combines 30+ years of industry expertise with cutting-edge technology—including 100+ circular looms and 30+ lamination machines—to produce FIBCs that meet stringent global standards. With annual sales exceeding $80 million and a presence in over 50 countries, our solutions are trusted by food processors, agricultural exporters, and chemical manufacturers alike.
Sector-Specific Requirements for Anti-Bulge FIBC Bags
1. Flour and Grain Powders
- Key Challenges: Moisture absorption, dust generation, and weight distribution.
- Solutions:
- Breathable fabric (plain or vented) to prevent condensation.
- Food-grade liners (HDPE/LDPE) for moisture resistance.
- SWL 1,000–2,250 kg to accommodate dense powders.
- Example: A U.S. flour mill reduced waste by 15% after switching to VidePak’s UV-stabilized, anti-static FIBCs with baffle designs.
2. Sugar and Sweeteners
- Key Challenges: Hygroscopic properties, UV degradation.
- Solutions:
- UV-protected coating to prevent melting or crystallization.
- Coated polypropylene for water resistance.
- Circular-shaped bags for even weight dispersion.
- Case Study: A Brazilian sugar exporter reported a 20% longer shelf life using VidePak’s laminated FIBCs with discharge spouts.
3. Spices and Seasonings
- Key Challenges: Aroma retention, contamination risks.
- Solutions:
- Multi-layer lamination (BOPP/PE) for odor sealing.
- Dust-proof seams with overlock stitching.
- Custom printing for branding and compliance labeling.
4. Food Additives and Agro-Processing
- Key Challenges: Chemical reactivity, regulatory compliance.
- Solutions:
- Conductive or anti-static liners for flammable additives.
- BRC/ISO 9001 certifications for global market access.
- Reinforced lifting loops (4-belt cross-corner) for heavy loads (up to 4,000 kg SWL).
Technical Parameters: Choosing the Right FIBC
Parameter | Flour | Sugar | Spices | Additives |
---|---|---|---|---|
Fabric Weight | 150–180 g/m² | 170–200 g/m² | 130–150 g/m² | 200–220 g/m² |
Liner Type | HDPE | LDPE | PE/Aluminum | Conductive LDPE |
SWL | 1,500 kg | 1,000 kg | 1,000 kg | 2,250 kg |
UV Treatment | Required | Critical | Optional | Optional |
Certifications | FDA, BRC | ISO 22000 | HACCP | UN Certification |
FAQs: Addressing Buyer Concerns
Q1: How does fabric weight impact durability?
Higher g/m² fabrics (e.g., 220 g/m²) enhance puncture resistance for abrasive materials like animal feed or cement, while lighter fabrics (130 g/m²) suit lightweight spices.
Q2: When is a coated vs. uncoated FIBC preferable?
Coated bags (e.g., PE-laminated) are ideal for humid climates or water-sensitive products like sugar. Uncoated options reduce costs for dry, free-flowing powders.
Q3: What certifications are mandatory for EU food contact?
BRC Global Standard for Packaging and ISO 22000 are critical. VidePak’s FIBCs also comply with EU Regulation 10/2011 for food-grade materials.
Q4: Can anti-bulge FIBCs be reused?
Yes, but only if cleaned thoroughly and inspected for wear. VidePak offers SF 6:1 safety factor bags for extended reuse cycles.
VidePak’s Manufacturing Excellence
- Advanced Machinery: Starlinger extrusion lines ensure consistent fabric tensile strength (≥35 N/cm²).
- Customization: 10-color rotary printing for branding, with MOQs as low as 3,000 units.
- Sustainability: Recyclable PP materials and energy-efficient production reduce carbon footprint by 30%.
References
- VidePak Company Profile: https://www.pp-wovenbags.com/
- Industry Standards: ISO 9001, BRC Packaging, FDA CFR 21.
- Technical Guides: FIBC Design for Food Safety (Global Packaging Alliance, 2024).
For inquiries, contact info@pp-wovenbags.com.
External Resources:
- Learn about FIBC bulk bag innovations in our detailed guide: FIBC Bulk Bags: Enhancing Efficiency in Industrial Packaging.
- Explore anti-bulge design principles: Anti-Bulge FIBC Bags: Engineering for Stability.
Authored by VidePak’s Technical Team | Updated: March 2025