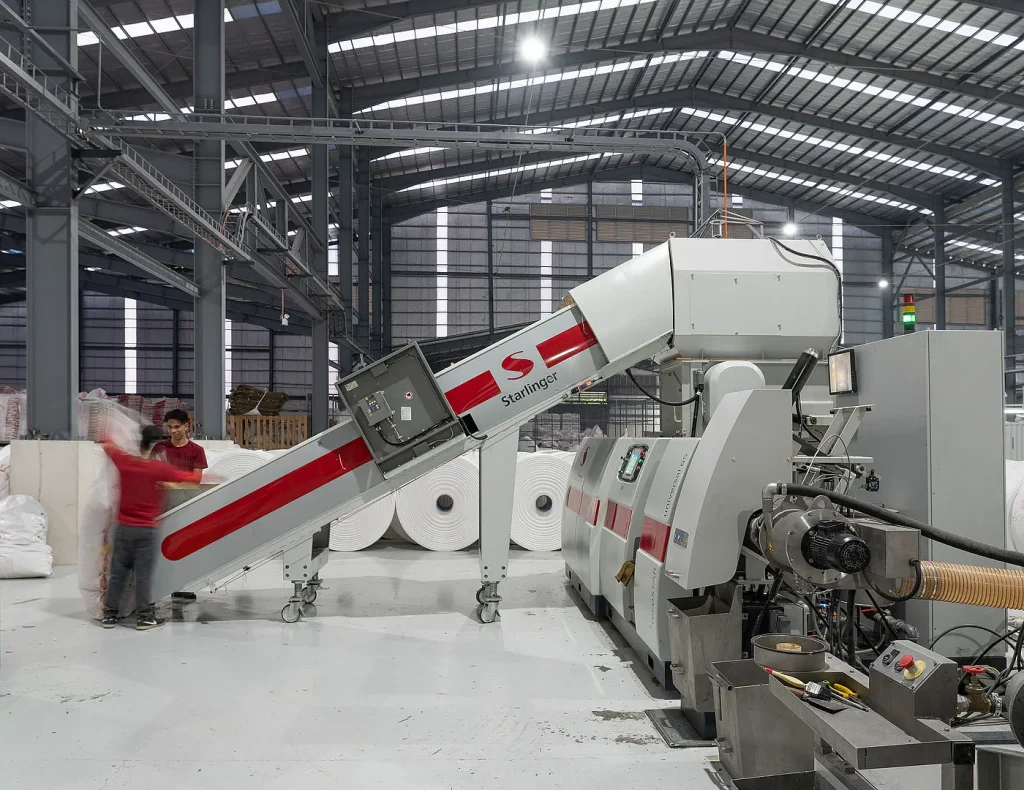
VidePak’s block BOPP bags, featuring color-coded stripes and precision-engineered labeling systems, reduce warehouse misclassification errors by 35% while maintaining tensile strengths of 1,000–1,200 N/5 cm. With over 12 million bags produced monthly using Starlinger weaving technology, our solutions streamline inventory management for industries ranging from agriculture to construction.
1. The Functional Anatomy of Block BOPP Bags
Block BOPP bags integrate Biaxially Oriented Polypropylene (BOPP) laminated onto woven PP fabric, creating a hybrid structure that balances durability and visual clarity.
1.1 Material Composition and Performance Metrics
- Base Fabric: Woven from virgin PP threads (1.8–2.3 mm width) at 10×10 to 12×12 threads per inch, achieving tear resistance of 800–1,200 N/5 cm.
- BOPP Lamination: 20–30 micron films provide UV resistance (98% blockage) and moisture barrier properties (WVTR <5 g/m²/day).
1.2 Color-Coded Striping Technology
VidePak’s 8-color flexographic printing allows permanent integration of color bands for instant product identification:
Color | Application | Industry Example |
---|---|---|
Blue | Fertilizers (NPK ratios) | Agriculture |
Red | Hazardous Chemicals | Industrial Manufacturing |
Green | Organic Products | Food & Beverage |
Yellow | Construction Aggregates | Waste Management |
A 2023 study showed that color-coded systems reduced warehouse sorting time by 28% for a Brazilian agricultural supplier.
2. Warehouse-Optimized Design Features
2.1 Smart Labeling Systems
- QR Code Zones: Dedicated 10×10 cm matte-finished areas for scannable labels, compatible with SAP and Oracle WMS.
- RFID Tag Pockets: Optional inner pouches (50×30 mm) for UHF RFID tags, enabling bulk scanning of up to 200 bags/second.
2.2 Ergonomic Handling Enhancements
- Grip Strips: Textured PP handles reduce slippage during mechanized lifting.
- Stacking Notches: Precision-cut corners enable stable palletization up to 6 meters high.
3. Technical Specifications and Compliance
3.1 Customization Parameters
Feature | Options | Performance Impact |
---|---|---|
Bag Size | 10 kg – 2,000 kg | Adapts to SKU dimensions |
Stripe Width | 2 cm – 10 cm | Visibility at 15-meter distance |
Closure Type | Heat-seal, Sewn, Ziplock | Leak prevention (ASTM D5635) |
3.2 Regulatory Compliance
- EU: EN 13432 (Recyclability), REACH (Chemical Safety)
- USA: FDA 21 CFR (Food Contact), OSHA 1910.1200 (Hazard Communication)
- China: GB/T 8946-2021 (PP Woven Bag Standards)
4. Case Study: Streamlining Cement Packaging
A Middle Eastern cement manufacturer adopted VidePak’s yellow-striped block BOPP bags with RFID pockets:
- Result: 92% inventory accuracy (up from 68%), saving $420,000 annually in lost shipments.
- Design: 50 kg capacity, 120 GSM fabric, 5 cm yellow stripe for loader visibility.
5. FAQs
Q1: How are color stripes applied without compromising strength?
A: Our in-line printing process bonds pigment at 180°C during lamination, maintaining fabric integrity.
Q2: Can bags withstand -20°C freezer storage?
A: Yes. BOPP films retain flexibility down to -30°C (tested per ASTM D1790).
Q3: What’s the MOQ for custom stripe designs?
A: 5,000 units, with 15-day lead time.
6. VidePak’s Manufacturing Capabilities
Established in 2008, VidePak combines three decades of expertise with cutting-edge infrastructure:
- Production: 100+ Starlinger circular looms, 30 lamination lines.
- Customization: 8-color HD printing, 48-hour prototype turnaround.
- Sustainability: 30% recycled PP options, ISO 14001-certified processes.
References
- VidePak Woven Bags. (2025). BOPP Laminated Woven Bags: Branding and Market Dynamics.
- ASTM D5635-19: Standard Test Method for Dynamic Water Resistance of Shipping Containers.
- GB/T 8946-2021: Polypropylene Woven Bags – China National Standard.
Contact
Email: info@pp-wovenbags.com
Website: https://www.pp-wovenbags.com/
For advanced insights into BOPP lamination techniques or RFID-integrated packaging, explore our resources on BOPP laminated woven bags and smart inventory solutions.