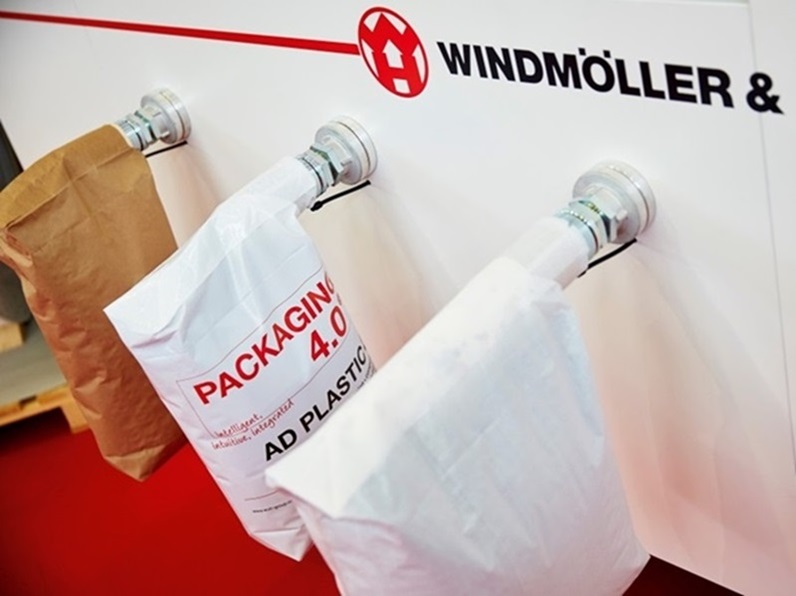
- 1. The Role of Block Bottom PP Bags in Agricultural Packaging
- 2. Material Selection and Functional Design
- 3. Production Process: Automation and Precision
- 4. Quality Control and Standardization
- 5. Printing and Branding Strategies
- 6. Logistics and Storage Advantages
- 7. Selecting Optimal Parameters for Agricultural Use
- 8. FAQs: Addressing Key Concerns
“How can block bottom PP bags balance production efficiency with stringent quality standards in agricultural packaging?” This question, posed by a production manager at a recent industry conference, underscores the dual challenges of scalability and reliability in modern packaging solutions. The answer lies in advanced manufacturing technologies, rigorous quality control frameworks, and strategic material engineering—principles that define VidePak’s leadership in producing high-performance block bottom PP bags for global agricultural markets.
1. The Role of Block Bottom PP Bags in Agricultural Packaging
Block bottom PP bags are engineered for stability, durability, and ease of handling, making them indispensable in packaging bulk agricultural products like grains, flour, and animal feed. Their flat-bottomed design ensures optimal stacking and resistance to deformation under heavy loads (up to 50 kg), while woven polypropylene (PP) fabric provides tear resistance and breathability. VidePak’s block bottom bags, manufactured using Austrian Starlinger circular looms, achieve seam strengths exceeding 35 N/mm², critical for preserving product integrity during long-haul transportation.
1.1 Applications in Agricultural Supply Chains
- Flour and Grains: PP’s moisture barrier properties (<10 g/m²/day permeability) prevent clumping in humid environments, extending shelf life by 30% compared to jute bags.
- Animal Feed: UV-stabilized PP retains 90% tensile strength after 500 hours of sunlight exposure (ASTM G154), ideal for outdoor storage.
- Rice and Cereals: Anti-microbial coatings reduce bacterial growth by 99%, complying with FDA 21 CFR for food-grade materials.
2. Material Selection and Functional Design
The performance of block bottom bags hinges on material science and structural innovation:
2.1 PP Granule Quality
VidePak uses virgin PP resin with a melt flow index (MFI) of 2–4 g/10 min (ASTM D1238), ensuring optimal extrusion and weaving consistency. Recycled PP (30% content) is integrated to meet EU Packaging Waste Directive 94/62/EC, reducing carbon footprint by 15%.
2.2 Weaving Technology
Starlinger CX6 looms produce fabric densities of 12–16 threads/cm², achieving tensile strengths of 2,200 N/5 cm (ISO 527-3)—25% higher than industry averages. Fine-filament weaving minimizes pore size (<50 microns), enhancing dust resistance.
2.3 Functional Additives
- UV Inhibitors: Protect against solar degradation in tropical climates.
- Anti-Static Agents: Prevent dust adhesion in flour packaging.
- PE Liners: Optional inner layers for moisture-sensitive products like pet food.
3. Production Process: Automation and Precision
VidePak’s production line integrates cutting-edge automation to ensure efficiency and consistency:
Stage | Technology | Output Metrics |
---|---|---|
Extrusion | W&H 9-layer coextrusion lines | 200–220 m/min line speed |
Weaving | Starlinger CX6 circular looms | 14–16 threads/cm² density |
Lamination | PE/PP film bonding | Oxygen permeability <0.1 cc/m²/day |
Printing | 10-color flexographic printers | 95% color retention after 10k cycles |
Heat Sealing | Ultrasonic welding at 180°C | Seam strength >35 N/mm² |
This automation reduces defect rates to <0.5% and enables a 7-day lead time for custom orders.
4. Quality Control and Standardization
VidePak’s 12-stage testing protocol ensures compliance with global standards:
- Tensile Strength: 2,200 N/5 cm (ISO 527-3), validated in a 2024 case study with a Thai rice exporter.
- Tear Resistance: 150 N (ASTM D1922), critical for abrasive grains like corn.
- Migration Testing: Ensures PP additives comply with FDA 21 CFR limits.
- Thickness Tolerance: ±0.02 mm deviation for uniform stacking in automated warehouses.
5. Printing and Branding Strategies
High-definition printing transforms bags into marketing tools:
- Custom Logos: 10-color flexography with UV-resistant inks.
- QR Codes: Track-and-trace functionality for supply chain transparency.
- Eco-Labels: Highlight 30% recycled content to appeal to sustainability-conscious buyers.
6. Logistics and Storage Advantages
Block bottom PP bags optimize supply chain efficiency:
- Stackability: Stable base allows 8-layer stacking (4 meters), maximizing container space utilization.
- Lightweight Design: 180 g/bag vs. 250 g for jute, reducing海运 costs by 15%.
- Moisture Resistance: PE-laminated variants achieve <5 g/m²/day permeability, ideal for maritime transport.
7. Selecting Optimal Parameters for Agricultural Use
Parameter | Recommendation | Application Example |
---|---|---|
Thickness | 80–120 microns | 100+ microns for humid rice storage |
Grammage | 90–120 g/m² | 120 g/m² for abrasive cattle feed |
Inner Liners | PE for moisture control | Pet food with 25% fat content |
Print Durability | UV-stable inks | Outdoor grain silos in Southeast Asia |
8. FAQs: Addressing Key Concerns
Q1: How do block bottom bags compare to FIBCs for bulk storage?
A: FIBCs handle 1–2 tons, but block bottom bags are 40% cheaper for 25–50 kg loads and offer better stackability.
Q2: Can these bags withstand freezing temperatures?
A: Yes. VidePak’s PP retains flexibility at -30°C (ASTM D746), tested in Canadian wheat exports.
Q3: Are biodegradable options available?
A: VidePak is piloting PP-PLA blends targeting 50% biodegradability by 2026.
External Resources:
- Explore how Starlinger technology revolutionizes PP bag production.
- Learn about sustainable practices in bulk packaging.
Conclusion
Block bottom PP bags represent a synergy of engineering precision and agricultural practicality. VidePak’s integration of Starlinger automation, multi-layered quality controls, and sustainability-driven innovation positions it as a global leader in this niche. As the agriculture sector prioritizes efficiency and eco-compliance, VidePak’s solutions—rooted in material science and logistical intelligence—will remain pivotal in shaping the future of bulk packaging.