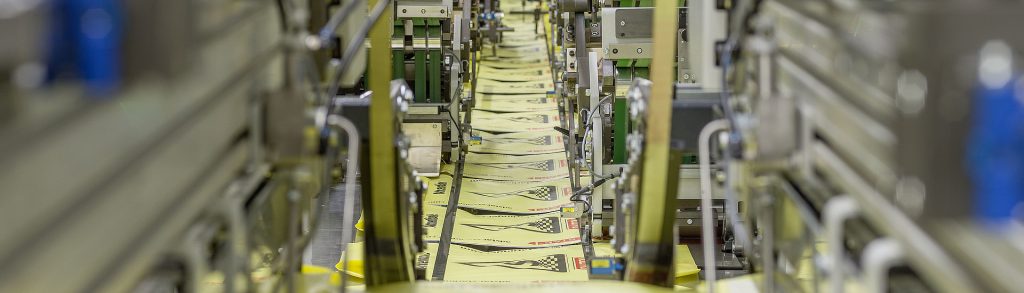
When considering packaging solutions, woven bags, especially Block Bottom Valve Bags, are among the most versatile and widely used options across different industries. These bags are designed for various purposes, ranging from the packaging of agricultural products to chemicals, fertilizers, and other bulk materials. As a company that specializes in manufacturing high-quality woven bags, including Valve PP Bags, understanding the different valve types and the materials used for their production is crucial.
This article will explore the characteristics of Block Bottom Valve Bags, the various valve types used, and the key materials such as PP, HDPE, PE, and Aluminum foil that make these bags an ideal choice for specific packaging needs.
Block Bottom Valve Bags and Their Types
Block Bottom Valve Bags, also known as Block Bottom Valve sacks, are commonly used for packaging dry bulk products like flour, chemicals, feed, and fertilizer. Their design allows for easy filling and efficient stacking, which is essential for optimizing storage and transportation. These bags have a distinct block bottom that provides stability, making them easy to transport without risk of tipping over.
Valve Types in Block Bottom Valve Bags
When discussing Valve Woven Bags, it is essential to understand the different types of valves that can be integrated into these bags. The valve is the opening mechanism that facilitates quick filling and sealing. Here are the main types:
- Standard Valve: This is the most common valve type, where the filling process is straightforward, and the bag is sealed by folding the valve over after filling.
- Spout Valve: Often used for products that need to be packed under controlled conditions, such as powders or granules. The spout is placed inside the filling system, and the valve is sealed around it.
- Taped Valve: This valve type features an adhesive tape that seals the valve after the product is filled. It is commonly used for products that are sensitive to contamination and require a tamper-proof seal.
- Pasted Valve: Similar to the taped valve but with the addition of a paste that secures the bag. This option is often used for heavier materials or those with a higher level of moisture.
These valve types offer a high level of customization, making Block Bottom Valve Bags versatile for multiple industries, including agriculture, chemicals, and food packaging.
Material Choices for Woven Bags: Analyzing Key Options
The material used for manufacturing woven bags is a critical factor in determining the strength, durability, and functionality of the final product. Among the most common materials used are Polypropylene (PP), High-Density Polyethylene (HDPE), Polyethylene (PE), and Aluminum foil. Each material offers unique properties that make it suitable for different applications.
1. Polypropylene (PP)
Polypropylene is one of the most widely used materials in the production of Valve Woven Bags, including Valve PP Bags. It is a thermoplastic polymer known for its strength, flexibility, and resistance to chemical and environmental factors.
- Advantages:
- Durability: PP bags are resistant to tearing, punctures, and abrasions.
- Lightweight: Despite their strength, PP bags are lightweight, which makes them an ideal choice for bulk packaging.
- Cost-Effective: Polypropylene is a relatively inexpensive material, making it a preferred choice for industries that require large quantities of bags.
- Moisture Resistance: PP bags are water-resistant, which is essential for protecting products like grains, fertilizers, and chemicals.
- Applications: Valve PP Bags are commonly used in the food industry, chemicals, and construction materials, making them a versatile choice.
2. High-Density Polyethylene (HDPE)
HDPE is another popular material for woven bags, particularly when additional strength and resistance to chemical reactions are required. It is a polymer with a high strength-to-density ratio.
- Advantages:
- Stronger than PP: HDPE offers superior strength, making it an ideal choice for bags that will hold heavy or bulky products.
- Chemical Resistance: HDPE bags are resistant to a wide range of chemicals, making them perfect for packaging hazardous or industrial materials.
- UV Resistance: HDPE bags are resistant to ultraviolet light, ensuring that products stored outdoors will remain protected from degradation.
- Applications: These bags are commonly used in the packaging of agricultural products, industrial chemicals, and waste materials.
3. Polyethylene (PE)
Polyethylene is one of the most commonly used plastic materials globally. In its various forms, PE can be used in different packaging applications, from single-use bags to durable woven sacks.
- Advantages:
- Waterproof: PE offers excellent water resistance, which makes it a top choice for protecting products from moisture during transport.
- Flexibility: PE woven bags can be manufactured in various thicknesses, providing the flexibility needed for different packaging needs.
- Sealing Properties: PE is easy to heat seal, which is an essential feature for ensuring the integrity of the packaging.
- Applications: PE Woven Bags are often used for packaging agricultural goods, such as seeds, grains, and fertilizers, as well as for general-purpose bulk packaging.
4. Aluminum Foil
Aluminum Foil is typically laminated onto woven fabrics to create bags with enhanced moisture and gas barrier properties. This combination is especially useful when packaging sensitive products that require protection from light, air, and moisture.
- Advantages:
- Barrier Protection: Aluminum foil offers excellent protection against light, oxygen, and moisture, making it ideal for packaging food products, chemicals, and pharmaceuticals.
- Durability: The foil layer provides an additional layer of strength, ensuring the bag holds up under pressure and external stress.
- Aesthetic Appeal: The shiny, metallic finish can provide a premium look for retail packaging, which is important for branding purposes.
- Applications: Aluminum foil composite bags are often used for packaging high-value or sensitive products, such as food, pharmaceuticals, and chemicals.
Table: Comparison of Woven Bag Materials
Material | Advantages | Applications |
---|---|---|
Polypropylene (PP) | Durable, lightweight, moisture-resistant, cost-effective | Food, chemicals, agriculture, construction |
High-Density Polyethylene (HDPE) | Strong, chemically resistant, UV resistant | Agriculture, chemicals, heavy-duty packaging |
Polyethylene (PE) | Waterproof, flexible, easy to seal | Grains, fertilizers, general-purpose packaging |
Aluminum Foil | Moisture, oxygen, and light barrier, durable, aesthetic appeal | Food, pharmaceuticals, chemicals |
Conclusion
When choosing the right woven bag, especially Block Bottom Valve Bags, it is essential to consider the material based on the specific requirements of the product being packaged. PP, HDPE, PE, and Aluminum foil all offer unique advantages and play a vital role in the packaging industry. Whether you need a lightweight and cost-effective solution like Valve PP Bags or a high-performance bag for hazardous materials, selecting the right material will ensure the safety, durability, and efficiency of your packaging solution.
For more insights into Block Bottom Valve Bags, visit this detailed guide. Additionally, explore the versatility of Valve PP Bags in packaging applications by checking out this informative article.