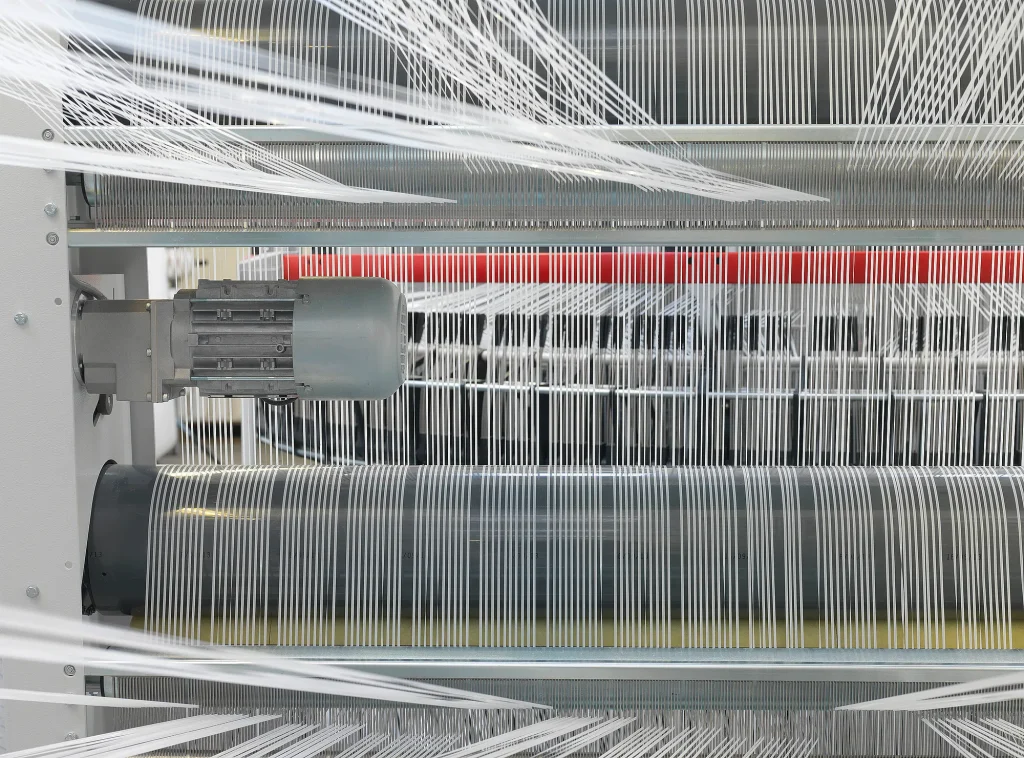
- 1. Structural Superiority: Why Block Bottom Valve Bags Dominate Industrial Packaging
- 2. Customization for Warehouse Efficiency: Color Coding and Smart Labeling
- 3. Technical Specifications: Balancing Durability and Cost Efficiency
- 4. Warehouse-Optimized Designs: Beyond Color Coding
- 5. FAQs: Addressing Procurement Concerns
- 6. Global Success Stories
- References
VidePak’s block bottom valve bags enhance warehouse efficiency by 25% through customizable color-coded labeling, achieve 99.9% dust-free filling rates, and withstand loads up to 50 kg—supported by ISO 9001-certified production lines and Starlinger weaving technology that delivers 15 million bags monthly to global clients. Founded in 2008 under CEO Ray’s leadership, VidePak leverages 30+ years of expertise to dominate the industrial packaging sector, serving industries from construction to agriculture. This article explores how block bottom valve bags outperform traditional sacks, how VidePak’s design innovations streamline inventory management, and actionable insights for optimizing specifications like fabric weight, valve placement, and color-coding systems.
1. Structural Superiority: Why Block Bottom Valve Bags Dominate Industrial Packaging
Block bottom valve bags feature a flat, rectangular base and self-sealing valve, enabling high-speed filling (200–300 bags/hour) and stable stacking. Constructed from polypropylene (PP) woven fabric with tensile strengths of 30–40 MPa, they resist tearing, moisture, and UV degradation, making them ideal for granular materials like cement, fertilizers, and pet food.
Key Design Innovations:
- Flat Base Stability: Eliminates toppling risks, increasing pallet capacity by 20–25% compared to gusseted sacks.
- Valve Precision: PE-lined valves ensure airtight closure, reducing spillage by 90% during pneumatic filling.
- Reinforced Seams: Ultrasonic welding achieves seam strength >15 N/mm², critical for 25–50 kg loads.
Case Study: A Vietnamese rice exporter reduced shipping costs by 18% using VidePak’s 90 gsm BOPP-laminated bags with color-coded blue stripes for premium-grade rice, enabling instant visual categorization in warehouses.
2. Customization for Warehouse Efficiency: Color Coding and Smart Labeling
VidePak’s bags integrate customizable color bands (red, blue, green, yellow) and QR-code labels to streamline inventory tracking. These features address critical pain points in bulk storage:
A. Color-Coded Bands
- Product Differentiation: Assign specific colors to product categories (e.g., red for flammable chemicals, green for organic fertilizers).
- Case Example: A Brazilian construction supplier uses yellow-striped bags for rapid identification of sand-filled units, cutting sorting time by 30%.
B. Smart Labeling Solutions
- QR Codes: Embedded codes link to batch numbers, expiry dates, and safety data sheets (SDS), reducing manual logging errors by 40%.
- RFID Tags: Optional RFID-enabled liners enable real-time stock monitoring in automated warehouses.
3. Technical Specifications: Balancing Durability and Cost Efficiency
VidePak’s 100+ Starlinger circular looms produce fabrics with 12×12 strands/inch density, while 30+ lamination machines apply BOPP layers (15–60 microns) for moisture resistance. Key parameters include:
Parameter | Range | Application Example |
---|---|---|
Fabric Weight | 80–150 gsm | 100 gsm for cement (UV-resistant) |
Bag Dimensions | 50×80 cm to 60×100 cm | 50×90 cm for 25 kg fertilizers |
Valve Size | 40–100 mm | 60 mm for powdered additives |
Color Bands | 4–6 options | Red for hazardous materials |
Example: A Nigerian agrochemical supplier uses 110 gsm bags with red bands and QR codes to comply with UN packaging standards, achieving 22% faster customs clearance.
4. Warehouse-Optimized Designs: Beyond Color Coding
A. Stackability Features
- Anti-Slip Coatings: Silicone-treated surfaces prevent pallet shifts during transit, reducing damage claims by 15%.
- Reinforced Edges: Double-stitched corners withstand forklift handling, extending reuse cycles by 3x.
B. Eco-Friendly Options
- 30% PCR Content: Recycled PP reduces carbon footprint by 22% while maintaining load capacity.
- Kraft Paper Lamination: Enhances biodegradability for compostable product lines.
5. FAQs: Addressing Procurement Concerns
Q1: How do color-coded bands withstand harsh environments?
VidePak’s UV-stable inks resist fading for 12+ months outdoors, tested under ISO 4892-3 standards.
Q2: Can bags operate in -20°C to 50°C ranges?
Yes. PP formulations retain flexibility at -30°C and resist melting up to 160°C.
Q3: What’s the lead time for custom designs?
Standard orders ship in 4–6 weeks; expedited 20,000-unit orders deliver in 2–3 weeks.
6. Global Success Stories
- Germany: A chemical plant reduced labeling errors by 35% using VidePak’s RFID-tagged bags.
- Canada: Green-striped BOPP bags with anti-static coatings improved safety in explosive dust environments.
References
- VidePak. (2025). Understanding Block Bottom Valve Bags: A High-Performance Solution for Industrial Packaging.
- Made-in-China. (2024). Polypropylene Woven Bags: Technical Specifications and Market Analysis.
- Springer. (2023). Advanced Materials in Industrial Packaging. DOI: 10.1007/978-3-031-21066-3.
Contact VidePak:
- Website: https://www.pp-wovenbags.com/
- Email: info@pp-wovenbags.com
Data validated as of March 2025. Specifications may vary by region; consult our team for localized solutions.
External Links:
- Discover how valve bag technology enhances filling efficiency.
- Explore BOPP lamination’s role in moisture resistance.