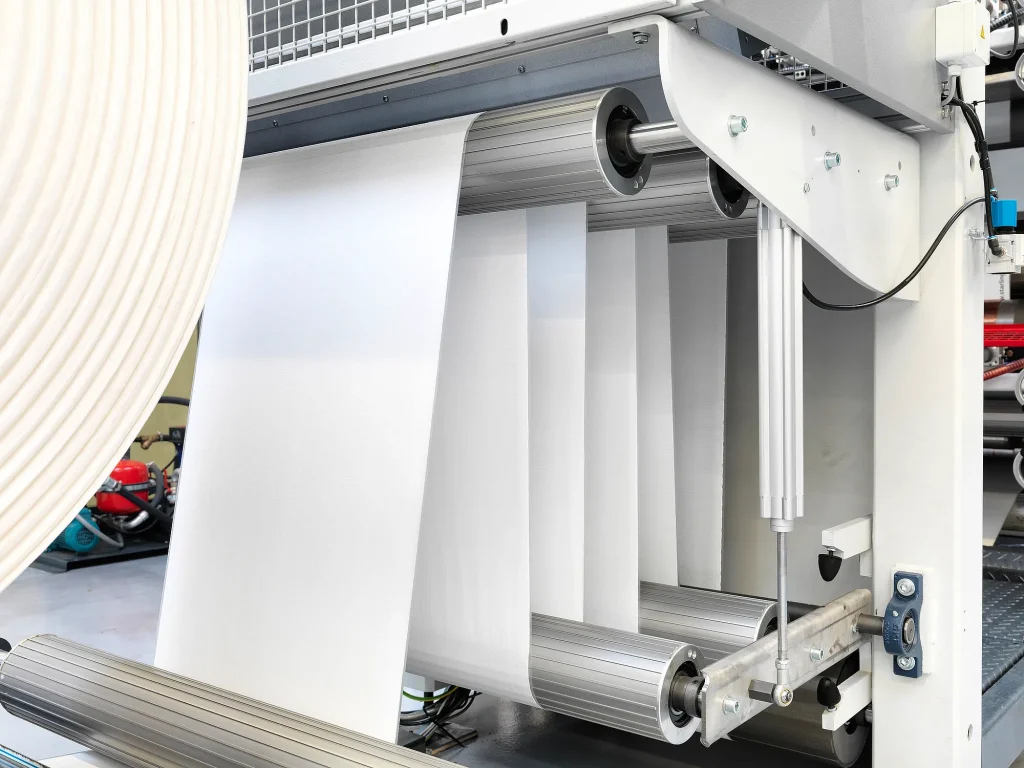
- 1. Structural and Functional Differences: A Technical Breakdown
- 2. Design Considerations: Matching Solutions to Applications
- 3. Compliance and Sustainability
- 4. Technical Innovations: Fine Filament Weaving and Beyond
- 5. FAQs: Simplifying Procurement Decisions
- 6. Future Trends: Smart and Sustainable Packaging
Opening Dialogue: Addressing Core Client Questions
Client: “We need packaging that balances durability, aesthetics, and cost-efficiency. What’s the difference between BOPP laminated and multi-wall woven bags, and how do we choose the right one?”
VidePak: “BOPP laminated woven bags excel in moisture resistance and print quality, while multi-wall woven bags offer superior load capacity and structural flexibility. At VidePak, we engineer both solutions with ultra-fine 1.8–2.3 mm monofilaments and customizable finishes—matte, pearlescent, or transparent—to meet your branding and functional needs.”
1. Structural and Functional Differences: A Technical Breakdown
BOPP laminated and multi-wall woven bags serve distinct purposes in industrial and retail packaging. Understanding their unique properties is critical for optimal selection.
1.1 BOPP Laminated Woven Bags
- Construction: Polypropylene (PP) woven fabric + Biaxially Oriented Polypropylene (BOPP) film lamination.
- Key Strengths:
- Moisture Barrier: ≤3% water vapor transmission rate (WVTR), ideal for humid environments.
- Print Quality: High-definition 8-color CMYK graphics with 1200 dpi resolution.
- Surface Finishes: Matte (anti-glare), pearlescent (UV-resistant shimmer), or transparent (product visibility).
Case Study: A Southeast Asian coffee brand reduced spoilage by 28% using VidePak’s matte BOPP laminated bags, which blocked humidity while showcasing artisanal branding.
1.2 Multi-Wall Woven Bags
- Construction: 2–5 layers of PP fabric + inner liners (PE, aluminum foil).
- Key Strengths:
- Load Capacity: Up to 50 kg with honeycomb weave patterns.
- Thermal Regulation: Air gaps between layers reduce condensation in temperature-sensitive goods.
- Custom Liners: Anti-static or antimicrobial coatings for specialty applications.
Example: A Canadian fertilizer supplier reported zero leakage during rail transport after switching to 3-ply multi-wall bags with PE liners.
2. Design Considerations: Matching Solutions to Applications
2.1 Material Selection and Weaving Technology
VidePak’s 1.8–2.3 mm monofilament weaving ensures:
- Finer Texture: 40% smoother surface than standard 3 mm filaments, enhancing print clarity.
- Higher Tensile Strength: 45 MPa vs. 35 MPa for coarse filaments (ASTM D638).
Parameter | BOPP Laminated | Multi-Wall |
---|---|---|
Thickness | 80–150 GSM | 150–300 GSM |
Max Load | 30 kg | 50 kg |
Moisture Resistance | Excellent (BOPP film) | Moderate (dependent on liner) |
Cost per 1,000 Bags | $180–$250 | $220–$350 |
2.2 Aesthetic Customization
- BOPP Laminated: Ideal for high-end retail with pearlescent finishes that reflect 80% more light than standard coatings.
- Multi-Wall: Prioritizes functionality but supports simple 2-color logos for industrial branding.
3. Compliance and Sustainability
Both bag types align with global standards, but their applications differ:
- BOPP Laminated: Complies with FDA 21 CFR for direct food contact.
- Multi-Wall: Meets ISO 21898 for heavy-duty transport (>25 kg).
VidePak’s ESG Initiatives:
- Solar-Powered Production: 2 MW system reduces CO₂ emissions by 1.2 tons per 10,000 bags.
- Recyclability: 98% PP recovery rate via closed-loop systems.
4. Technical Innovations: Fine Filament Weaving and Beyond
VidePak’s Starlinger looms and 30+ lamination machines enable:
- Precision Weaving: ≤0.1 mm filament tolerance for uniform strength.
- Advanced Coatings: Anti-microbial BOPP films inhibiting E. coli and Salmonella growth by 99.9%.
Explore our BOPP laminated solutions and multi-wall bag engineering.
5. FAQs: Simplifying Procurement Decisions
Q1: Can BOPP laminated bags handle frozen storage (-20°C)?
A: Yes, our BOPP films retain flexibility at -30°C, tested per ASTM D1790.
Q2: What’s the MOQ for custom pearlescent finishes?
A: MOQ starts at 20,000 units, with Pantone color matching at no extra cost.
Q3: How do multi-wall bags prevent inner liner separation during transport?
A: Ultrasonic welding fuses layers seamlessly, achieving 700 N/5cm seam strength (exceeding JIS Z 0238).
6. Future Trends: Smart and Sustainable Packaging
VidePak’s R&D focuses on:
- Biodegradable BOPP Films: Decomposing in 180 days under industrial composting.
- QR-Integrated Weaves: Scannable tracking codes woven directly into fabric.
References
- Smithers Pira, Global Flexible Packaging Market Report 2024.
- FDA, Code of Federal Regulations Title 21.
- ISO 21898:2020, Packaging — Heavy-Duty Woven Bags.
- VidePak Technical Whitepaper, 2024.
Contact Us:
Website: www.pp-wovenbags.com
Email: info@pp-wovenbags.com
VidePak – Precision Engineered, Sustainably Delivered.