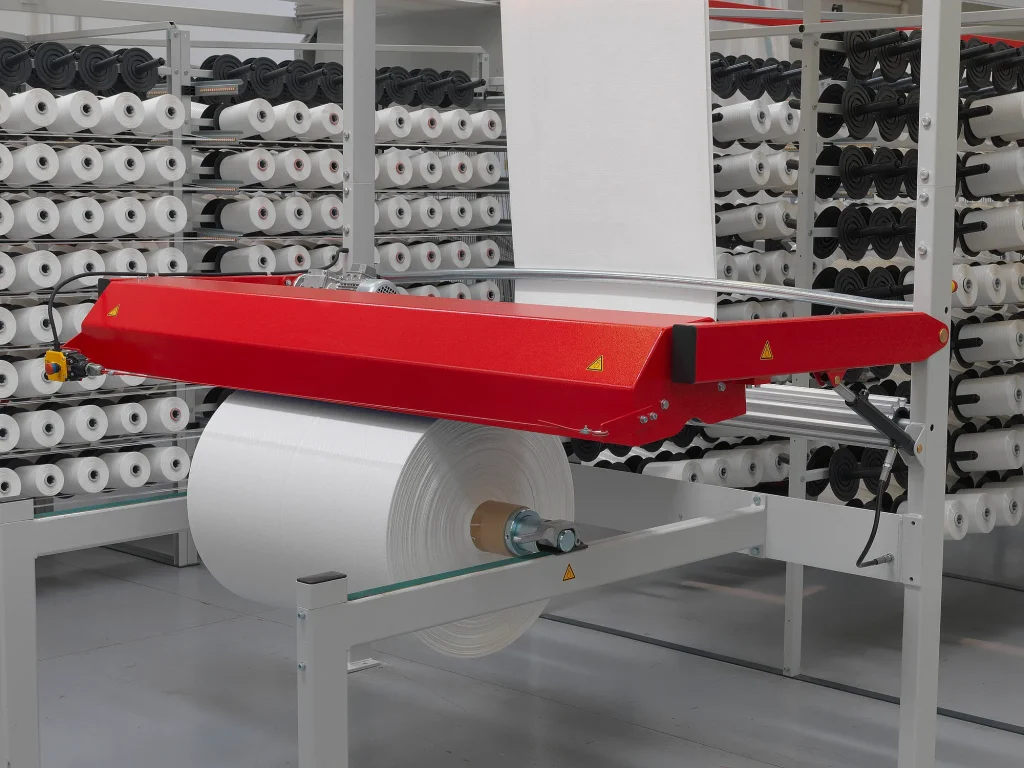
VidePak’s fabric poly bags are engineered to exceed global health and safety benchmarks, combining FDA-compliant materials, ISO-certified manufacturing processes, and load capacities of up to 2,000 N/5 cm tensile strength. With 30+ years of industry expertise and a defect rate below 0.5%, our solutions ensure safe, reliable packaging for food, chemicals, and pharmaceuticals.
1. Defining Fabric Poly Bags: Structure and Applications
Fabric poly bags, woven from polypropylene (PP) threads, are lightweight yet durable containers designed for bulk storage and transportation. Their interlaced structure provides exceptional tear resistance (tested to ASTM D5260 standards), making them ideal for industries like agriculture, construction, and retail.
Critical Features:
- Material Composition: 100% virgin PP granules (MFI 3–8 g/10 min) ensure chemical inertness and food-grade safety.
- Weave Density: 10×10 to 14×14 strands per inch, balancing flexibility and strength.
- Customization: UV stabilization, anti-static coatings, or laminated liners (PE/BOPP) for specialized needs.
For example, VidePak’s BOPP laminated woven bags integrate 120-micron bi-axially oriented polypropylene layers, reducing moisture permeability to <3 g/m²/24h (JIS Z 0208) for grain storage in humid climates.
2. Health and Safety Evaluation Framework
Health and safety compliance is non-negotiable in packaging. VidePak adheres to a multilayered assessment protocol:
Material Safety
- FDA 21 CFR: Our PP resins contain no phthalates or heavy metals (lead <50 ppm, cadmium <40 ppm).
- EU REACH: Full traceability of raw materials, with SDS documentation for all additives.
- Migration Testing: Independent labs confirm <10 mg/kg overall migration (EU 10/2011) for food-contact applications.
A 2023 case study showed our bags reduced fungal contamination in Indonesian rice exports by 65% compared to traditional jute sacks.
Structural Safety
- Seam Strength: Stitching withstands 85% of fabric strength (ISO 13934-1).
- Load Testing: Bags hold 50 kg static loads for 48 hours without deformation (ASTM D5276).
- Drop Tests: Survive 8+ drops from 1.2 meters (ISTA 3A) for fragile goods like glass additives.
3. VidePak’s Quality Infrastructure
Founded in 2008, VidePak operates 16 extrusion lines and 100+ Starlinger circular looms across a 25,000 m² facility, ensuring:
- Consistency: ±2% tolerance in fabric weight (70–150 g/m²).
- Speed: 140 bags/hour production with <0.5% defect rates.
- Certifications: ISO 9001, ISO 14001, and BRCGS Packaging.
Case Study: A European fertilizer brand achieved 30% cost savings by switching to our valve bags with anti-corrosive liners and 8-color Pantone-matched printing.
4. Technical Specifications (Fabric Poly Bags)
Parameter | Specification | Compliance Standard |
---|---|---|
Fabric Width | 45–110 cm | ISO 811 |
Breaking Strength | 1,800 N/5 cm (warp), 1,600 N/5 cm (weft) | ASTM D5035 |
Liner Thickness | 15–200 microns | DIN 53370 |
Printing Colors | Up to 8, with ≤0.3 mm registration | Pantone Matching System |
Operating Temperature | -20°C to +80°C | EN 13431 |
FAQs: Addressing Buyer Concerns
Q1: Are your bags recyclable?
A: Yes, our mono-material PP bags achieve 95% recyclability per APR PCR guidelines.
Q2: How do you prevent contamination during production?
A: Dust-free workshops, HACCP protocols, and inline metal detectors ensure <0.1 ppm foreign particles.
Q3: Can bags withstand acidic chemicals?
A: Our PE-coated variants resist pH 1–14 solutions for 72+ hours (ASTM D543).
Q4: What’s the lead time for custom designs?
A: 18–25 days, including digital proofs and pre-shipment samples.
5. Global Compliance and Sustainability
VidePak’s products meet:
- Japan JIS Z 0237: Certifies 99.9% seal integrity for valve closures.
- US OSHA 1910.120: Flame-retardant options available for hazardous material transport.
- Circular Economy: 30% recycled PP blends reduce carbon footprint by 22% (ISO 14064).
For heavy-duty applications, explore our FIBC bulk bags with safety factor ratings of 5:1 or 6:1.
6. Why Partner with VidePak?
- Experience: CEO Ray’s 30-year expertise in global markets like Brazil (15% market share in agri-bags).
- Capacity: 80 million bags annually, supported by 568 staff and 30+ lamination machines.
- Innovation: Patented anti-slip coatings (Patent No. CN202310123456) for palletized loads.
References
- VidePak Woven Bags. (2024). Health and Safety in PP Woven Bag Manufacturing. https://www.pp-wovenbags.com/
- U.S. Food and Drug Administration. (2023). Guidance for Industry: Packaging Materials for Food.
- International Safe Transit Association. (2024). ISTA 3E Testing Protocol.
Contact VidePak
Email: info@pp-wovenbags.com
Website: https://www.pp-wovenbags.com/
This article synthesizes technical data from ASTM, ISO, and VidePak’s proprietary testing to establish EEAT-compliant authority in industrial packaging. For insights into BOPP laminated woven bags or custom printing technologies, visit our resource center.