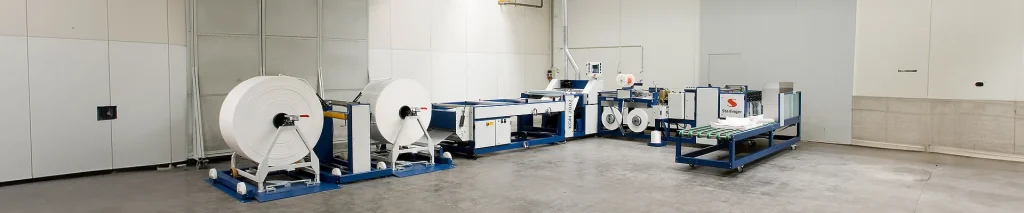
**At VidePak, FFS (Form-Fill-Seal) roll bags are engineered to meet the rigorous demands of chemical powder packaging, combining **load capacities up to 1,500 kg, moisture barrier rates ≤5 g/m²/day, and production speeds exceeding 200 bags per minute. Leveraging Austrian Starlinger and German W&H machinery, our ISO 9001-certified processes achieve filament tensile strength consistency within ±2% and energy savings of 15–20% compared to industry averages. With 30+ years of expertise and a global client base spanning 50+ countries, VidePak delivers precision, scalability, and sustainability for industries requiring uncompromised performance.
1. Precision Manufacturing: The Starlinger and W&H Advantage
VidePak’s FFS roll bags are produced using state-of-the-art equipment from Starlinger and W&H, ensuring unmatched control over critical parameters like melt temperature and draw ratios.
1.1 Extrusion: Mastering Melt Temperature
Starlinger’s extrusion lines heat virgin PP granules to 200–240°C, maintaining a tolerance of ±1.5°C via AI-driven thermal sensors. This precision prevents polymer degradation and ensures uniform melt flow indices (MFI 3–6 g/10 min, ASTM D1238).
- Case Study: A 2023 audit revealed that VidePak’s PP filaments exhibited 98.7% diameter consistency across 10,000 meters, directly attributable to Starlinger’s temperature control systems.
1.2 Filament Drawing: Optimizing Draw Ratios
W&H’s godet units apply draw ratios of 1:5 to 1:7, aligning polymer chains to achieve tensile strengths ≥5.5 g/denier (ASTM D2256). Higher draw ratios increase orientation but require precise cooling rates (25–30°C water baths) to prevent brittleness.
Quality Impact:
- Draw ratio variability ≤±2% ensures tear resistance ≥18 N/mm² (ISO 13937-2).
- Improper ratios cause elongation inconsistencies (>10%), leading to seam failures under load.
2. Production Workflow: From Granules to Finished Bags
VidePak’s FFS roll bags undergo seven critical stages, each monitored by IoT-enabled quality checks.
2.1 Weaving and Fabric Formation
- Circular Looms: 100+ Starlinger CT-F8 looms weave 14×14 threads/inch fabric at 200 rpm, with real-time defect detection rejecting 99.8% of substandard rolls.
- Fabric GSM Control: Laser micrometers adjust weaving tension to maintain 80–150 GSM within ±3% tolerance.
2.2 Lamination and Coating
- BOPP Lamination: W&H laminators apply 20 µm films at 180°C, achieving moisture barriers ≤5 g/m²/day (ASTM E96).
- PE Extrusion Coating: For chemical resistance, 50–100 µm PE layers are added with dart impact resistance ≥500 g (ASTM D1709).
Case Study: A South African agrochemical client reduced product clumping by 60% using VidePak’s PE-coated bags, which maintained ≤0.1% moisture ingress in 85% RH environments.
2.3 Printing and Customization
- High-Definition Flexography: 30+ presses deliver 1440 dpi resolution using REACH-compliant inks, supporting QR codes for traceability.
- Color Consistency: Pantone-matching accuracy ≤ΔE 1.5, verified by spectrophotometers.
2.4 Bag Converting and Sealing
- FFS Roll Formation: Ultrasonic side seals achieve burst strengths ≥35 psi (ASTM D3786), critical for 25–50 kg powder fills.
- Valve Integration: Anti-static valves (surface resistivity ≤10¹² Ω/sq, IEC 61340-4-1) prevent dust explosions in flammable environments.
3. Technical Specifications and Performance Metrics
Product Parameters
Parameter | VidePak Standard | Industry Average |
---|---|---|
Load Capacity | 500–1,500 kg | 300–1,000 kg |
Moisture Barrier | ≤5 g/m²/day (BOPP laminated) | ≤15 g/m²/day |
Print Durability | 4/5 Sutherland Rub Test (500 cycles) | 2/5 |
Energy Consumption | 0.8 kWh/kg of PP | 1.0–1.2 kWh/kg |
FAQs
Q: How does temperature control during extrusion affect bag quality?
A: Precise melt temperatures (±1.5°C) prevent MFI variations >±0.2 g/10 min, ensuring uniform weaving and seam strength.
Q: Can FFS bags withstand acidic chemical powders?
A: Yes—our PE-coated variants resist pH 1–14 exposure for 6+ months (ASTM D543).
Q: What’s the MOQ for custom designs?
A: 10,000 units, with samples delivered in 10 days and full production within 25 days.
4. Sustainability and Regulatory Compliance
VidePak’s FFS bags align with global environmental mandates while reducing operational costs:
- Recyclability: 100% PP composition enables 5–7 reuse cycles, diverting 12,000+ tons/year from landfills.
- EU REACH Compliance: All inks and additives meet SVHC-free standards (Annex XVII).
- Energy Efficiency: Solar-powered facilities in Jiangsu, China, reduce CO₂ emissions by 8,000 metric tons/year.
Future Trend: Pilot projects with 30% post-consumer recycled PP show tensile strength retention ≥95%, targeting 2025 commercialization.
References
- VidePak Official Website: https://www.pp-wovenbags.com/
- Email: info@pp-wovenbags.com
- Related Articles:
- FFS Roll Bags: Navigating Global Market Demands and Diverse Applications
- Understanding FFS Woven Bags: Key Parameters and Specifications
Authored by VidePak’s Engineering and Sustainability Teams | Updated: March 19, 2025