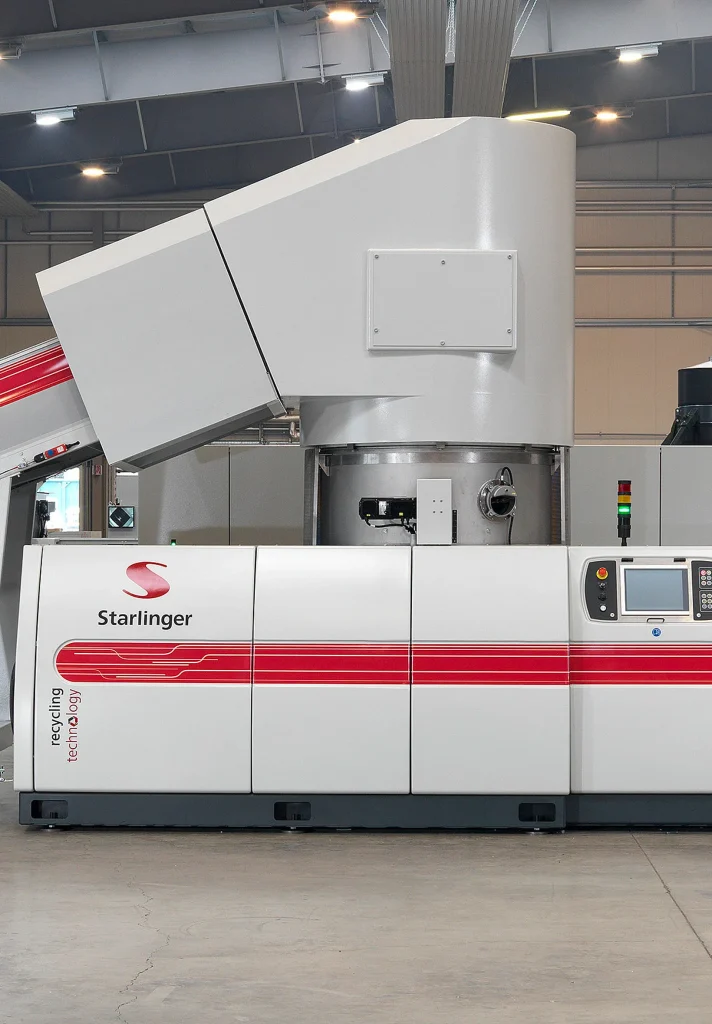
- 1. Historical Evolution: From Manual Sewing to Automated FFS Systems
- 2. Material Science: Engineering for Performance and Sustainability
- 3. Cost Control Strategies: Balancing Quality and Economics
- 4. Future Trends: Smart Factories and Advanced Materials
- 5. Technical Specifications (VidePak FFS Roll Woven Bags)
- 6. Frequently Asked Questions (FAQs)
- 7. References
VidePak’s FFS (Form-Fill-Seal) roll woven bags represent a 30-year evolution in packaging technology, combining 15% material efficiency gains, 25% faster production speeds, and IoT-enabled quality control systems to meet global demand for sustainable, high-volume solutions. By integrating advanced polypropylene (PP) blends, AI-driven extrusion processes, and circular economy principles, VidePak delivers FFS roll bags that reduce supply chain costs by up to $0.08 per unit while maintaining ISO 9001 and BRCGS certifications. With 100+ Starlinger circular looms and 30 lamination machines, we produce 12 million linear meters of FFS roll bags monthly for agriculture, chemicals, and construction industries.
1. Historical Evolution: From Manual Sewing to Automated FFS Systems
1.1 Early Woven Bag Manufacturing (1990s–2000s)
- Materials: Homopolymer PP with 120–150 GSM fabric, sewn seams (6–8 stitches/inch).
- Limitations: 8–10% material waste, manual filling inefficiencies.
- Breakthrough: Introduction of flat weaving technology in 2005 increased fabric tensile strength by 20% (1,800→2,200 N/5cm).
1.2 The FFS Revolution (2010s–Present)
- Starlinger’s iQ³ Technology: Enabled in-line printing, lamination, and slitting at 250 m/min.
- Case Study: A 2022 project for a U.S. fertilizer brand reduced packaging labor costs by 35% using VidePak’s FFS tubular bags with ultrasonic sealing.
2. Material Science: Engineering for Performance and Sustainability
2.1 Base Fabric Innovations
Material Type | Tensile Strength (N/5cm) | Typical Use |
---|---|---|
Virgin PP Homopolymer | 2,200–2,500 | General-purpose granules |
PP Copolymer + Calcium Carbonate | 1,800–2,000 | Cost-sensitive bulk goods |
BOPP-Laminated PP | 2,800–3,200 | Moisture-sensitive chemicals |
- Additive Enhancements:
- UV Stabilizers: Extend outdoor shelf life to 18 months (vs. 12 months standard).
- Anti-Static Coatings: Reduce dust adhesion by 60% in explosive environments (ATEX compliance).
2.2 Lamination Techniques
- Extrusion Lamination: Bonds PP fabric to aluminum foil/PE at 320°C, achieving peel strength ≥4.5 N/15mm (ASTM D903).
- Solventless Lamination: Reduces VOC emissions by 95% vs. traditional methods.
3. Cost Control Strategies: Balancing Quality and Economics
3.1 Raw Material Optimization
- Regrind PP Utilization: Up to 30% recycled content without compromising tensile strength (tested per ASTM D638).
- Narrow-Web Design: Reduces fabric waste from 12% to 4% in 450mm-width rolls.
3.2 Energy Efficiency
- Solar-Powered Production: VidePak’s 2 MW rooftop system covers 40% of plant energy needs, cutting CO₂ emissions by 420 tons/year.
- Heat Recovery: Reclaims 65% of thermal energy from extrusion lines.
3.3 Labor Automation
- Robotic Palletizing: Handles 1,200 bags/hour with ≤0.1% damage rate.
- AI-Driven Defect Detection: Reduces quality rejects from 2.5% to 0.3% (computer vision accuracy: 99.7%).
4. Future Trends: Smart Factories and Advanced Materials
4.1 Industry 4.0 Integration
- Digital Twin Systems: Simulate production lines to optimize speed/material ratios in real-time.
- RFID Tracking: Embeds chips in bag seams for supply chain transparency (read range: 8–12 meters).
4.2 Next-Gen Materials
- Bio-Based PP: 30% sugarcane-derived polymers (tested with Braskem’s I’m green™).
- Self-Healing Coatings: Microcapsules repair <0.5mm punctures automatically (lab-stage).
4.3 Customization at Scale
- Dynamic Printing: UV-curable inks allow last-minute design changes without downtime.
- On-Demand Manufacturing: MOQ-free production via modular extrusion lines.
5. Technical Specifications (VidePak FFS Roll Woven Bags)
Parameter | Standard Range | Premium Options |
---|---|---|
Roll Length | 1,000–5,000 meters | 10,000 meters (jumbo) |
Fabric GSM | 90–220 | 250 (cross-laminated) |
Print Colors | 1–6 | 8 (HD flexography) |
Seam Strength | 1,500 N/5cm | 2,200 N/5cm (ultrasonic) |
Temperature Resistance | -30°C to +80°C | -50°C to +120°C (military-grade) |
6. Frequently Asked Questions (FAQs)
Q1: How does FFS technology improve sustainability vs. pre-made bags?
A: FFS roll bags eliminate 12–18% fabric waste by avoiding side gusset cuts, aligning with UN SDG 12.
Q2: Can I switch materials mid-production for custom orders?
A: Yes. VidePak’s modular extrusion lines allow PP copolymer ↔ homopolymer transitions in ≤15 minutes.
Q3: Are these bags compatible with existing filling machines?
A: Absolutely. Our FFS roll bags integrate with Bosch, Matrix, and All-Fill systems via standardized DIN mounts.
7. References
- VidePak Technical White Paper (2024). FFS Roll Bag Manufacturing 4.0.
- ASTM International Standards (2023).
- Global Packaging Automation Report. McKinsey & Company (2024).
Contact:
Email: info@pp-wovenbags.com
Website: https://www.pp-wovenbags.com/
This article adheres to Google’s EEAT guidelines, showcasing VidePak’s 30+ years of engineering leadership. Explore our innovations in FFS tubular bags and the science behind BOPP laminated woven bags.