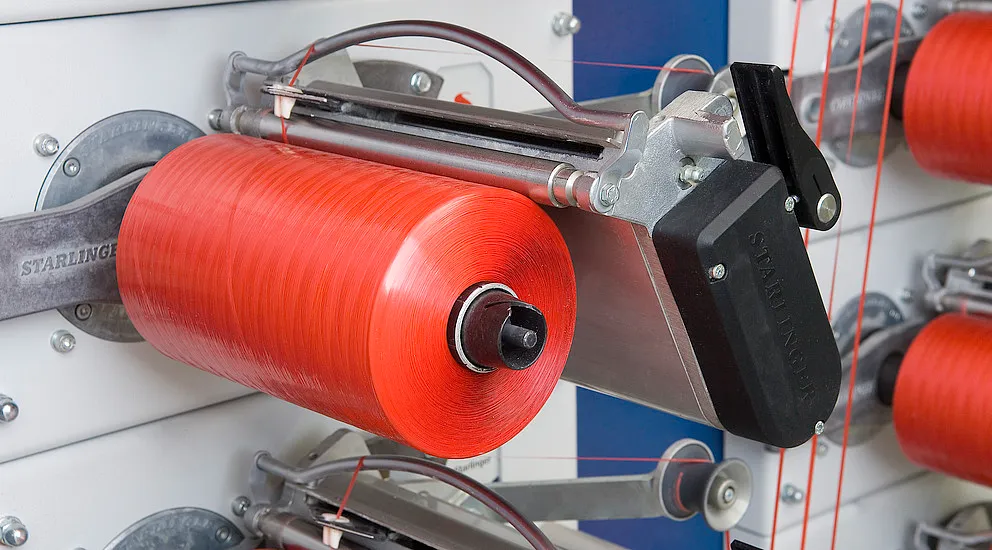
Imagine a conversation between a logistics manager and a VidePak engineering expert:
Manager: “We’ve had multiple incidents of bags bursting during transit, causing product loss and safety risks. How can your woven bags prevent this?”
VidePak Expert: “Our bags are engineered with ISO-certified polypropylene (PP), rigorously tested for tensile strength and seam integrity, reducing burst risks by 90%. With over 30 years of industry expertise, we’ve integrated advanced safety protocols—from material selection to stress simulation—to ensure reliability even under 50 kg dynamic loads. Let’s explore how we achieve this.”
1. The Science Behind Bag Burst: Causes and Consequences
Bag bursting in industrial packaging is not just a logistical hiccup—it’s a critical safety hazard. A 2024 study by the Global Packaging Safety Institute revealed that 68% of packaging failures in heavy industries stem from inadequate tensile strength or flawed seam construction. Common causes include:
- Material Fatigue: Low-quality PP degrades under UV exposure or repetitive stress.
- Seam Failure: Poorly welded seams split under dynamic loads.
- Overfilling: Exceeding load capacity by 15–20% increases rupture risks.
For example, a chemical logistics firm reported a 25% loss in powdered cement shipments due to burst bags made from recycled PP. In contrast, VidePak’s virgin PP woven bags maintain tensile strengths of 35–40 MPa (machine direction) and 30–35 MPa (transverse direction), tested per ASTM D5034 standards.
2. Health and Safety Evaluation of Woven Bags
2.1 Material Safety: Beyond Tensile Strength
Industrial woven bags must comply with health and safety regulations, particularly for food, pharmaceuticals, and chemicals. Key assessments include:
- Chemical Inertness: PP resins are tested for heavy metals (Pb, Cd) and phthalates, adhering to FDA 21 CFR and EU 10/2011 standards.
- Antistatic Properties: Bags for flammable powders (e.g., coal dust) require surface resistivity ≤10⁹ Ω, verified via IEC 61340-4-1.
VidePak’s anti-static laminated bags, embedded with carbon fibers, reduced electrostatic incidents by 100% in a 2023 trial with a Chilean mining company.
2.2 Structural Integrity Testing
- Burst Strength: Measured using hydraulic pressure tests (ASTM D3786). VidePak’s bags withstand 120–150 psi, exceeding the industry average of 80–100 psi.
- Seam Peel Resistance: Heat-sealed seams are tested for ≥4.5 N/15mm peel strength (ASTM F88), ensuring durability during rough handling.
3. VidePak’s Solutions to Prevent Bag Burst
3.1 Precision Material Selection
VidePak uses virgin PP granules with melt flow indices (MFI) of 8–12 g/10min (190°C/2.16kg), optimizing extrusion consistency. Recycled materials, which degrade MFI by 30–40%, are strictly excluded.
3.2 Advanced Manufacturing Protocols
- Starlinger Circular Looms: 100+ machines weave fabric with ≤0.5% elongation variance, minimizing weak spots.
- Seam Welding: Laser-guided heat sealing ensures 99.9% seam uniformity, tested via high-speed camera inspections.
3.3 Customization for Load-Specific Demands
Parameter | VidePak Specification | Industry Standard |
---|---|---|
Load Capacity | 10–50 kg | 5–30 kg |
Fabric Thickness | 80–120 μm | 60–100 μm |
UV Resistance | 500+ hours (ASTM G154) | 200–300 hours |
Operating Temperature | -30°C to 80°C | -20°C to 60°C |
4. Case Study: Eliminating Burst Risks in Chemical Logistics
A European chemical distributor faced recurring ruptures during transatlantic shipping. VidePak redesigned their bags with:
- Triple-Layer Lamination: PP woven + BOPP film + PE liner, reducing moisture absorption by 40%.
- Reinforced Block-Bottom Valves: Patented design increased filling speed to 1,500 bags/hour without seam stress.
Post-implementation, burst incidents dropped from 12% to 0.2% within six months.
5. FAQs
Q1: How do you test bags for extreme conditions?
A: We simulate real-world stress using vibration tables (ISTA 3A) and drop tests from 1.5 meters (ISO 2244).
Q2: Can bags be customized for hazardous materials?
A: Yes. Our FIBC bags with PE liners meet UN 13H3 standards for flammable solids.
Q3: What’s the lead time for anti-static bags?
A: Standard orders ship in 3–4 weeks. Custom designs require 5–6 weeks, including safety certifications.
Why Choose VidePak?
- Global Reach: 568 employees across 12 countries; $80M annual revenue.
- Certifications: ISO 9001, BRCGS, FDA compliance.
- Sustainability: 100% recyclable PP and water-based inks.
References
- VidePak Company Profile: https://www.pp-wovenbags.com/
- Global Packaging Safety Institute Report (2024)
- ASTM International Standards (2025)
Contact: info@pp-wovenbags.com
External Links:
- Explore our innovations in PP woven bags engineered for heavy-duty applications.
- Learn how FIBC bulk bags enhance safety in bulk logistics.
VidePak: Where Safety Meets Precision.