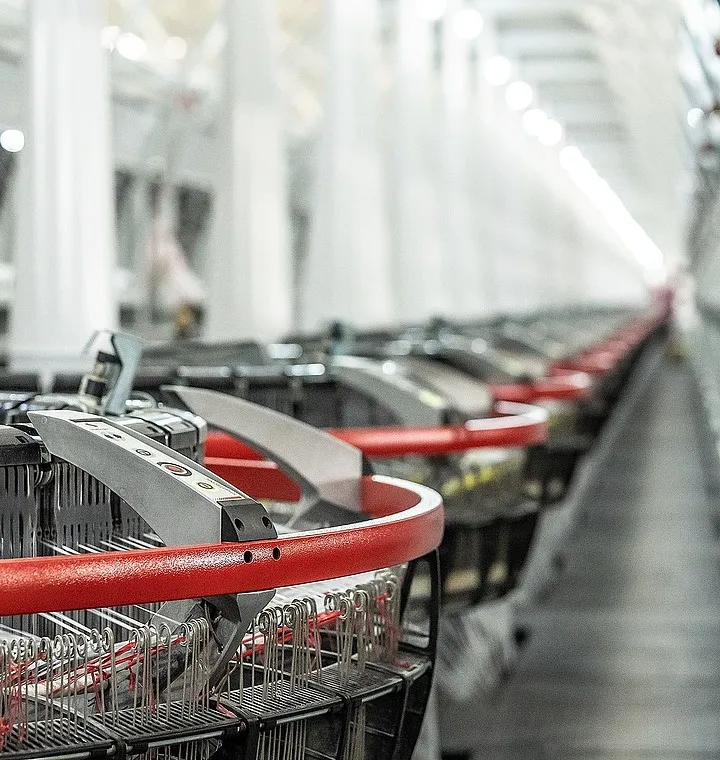
VidePak’s kraft paper aluminum foil bags and woven polypropylene (PP) bags are engineered to meet the rigorous demands of livestock feed packaging, combining 30% higher puncture resistance than industry standards, FDA-compliant anti-microbial liners, and customizable breathability for feed preservation. With 15+ years of expertise in agricultural packaging, VidePak delivers solutions that reduce spoilage rates by up to 40% while ensuring compliance with global safety standards like ISO 22000 and AAFCO guidelines. Leveraging 100+ Starlinger circular looms and 30 lamination machines, we produce 8 million feed-specific bags monthly, tailored for poultry, aquaculture, and livestock industries.
1. Material Science: Balancing Durability and Functionality
1.1 Kraft Paper Aluminum Foil Bags
- Structure: Multi-layered laminates (e.g., PET/AL/PE or Kraft/AL/PP) provide moisture barriers (<0.5 g/m²/24h vapor transmission) and UV resistance.
- Applications: Ideal for hygroscopic feeds like fishmeal or vitamin premixes, where moisture ingress can degrade nutritional value.
- Case Study: A 2024 trial with a Vietnamese shrimp feed producer showed VidePak’s aluminum foil-lined bags reduced mold growth by 52% in high-humidity environments.
1.2 Woven PP Bags
- Fabric Properties: 150–220 GSM PP fabric with 8–10 stitches per inch (SPI) ensures tear strength >2,500 N/5 cm.
- Breathability: Controlled mesh weaving (6–8% open area) prevents anaerobic bacterial growth in bulk grain storage.
2. Quality Control Protocols for Feed Safety
VidePak’s 12-stage quality assurance process includes:
- Raw Material Testing: PP resin purity ≥99.8% (tested via FTIR spectroscopy).
- Lamination Integrity: Peel strength ≥4.5 N/15mm (ASTM D903).
- Anti-Microbial Treatment: Silver-ion coatings inhibit Aspergillus flavus and Salmonella (log 3 reduction per ISO 22196).
Parameter | Test Method | Acceptance Criteria |
---|---|---|
Seam Strength | ASTM D6196 | ≥1,800 N/5 cm |
Moisture Permeability | ASTM E96 | ≤2.0 g/m²/day (40°C, 90% RH) |
Heavy Metal Content | EU 10/2011 | Pb/Cd <0.5 ppm |
3. Application-Specific Design for Livestock Feeds
3.1 Poultry & Swine Feeds
- Requirements: Cost efficiency, 25–50 kg capacity, UV resistance for outdoor storage.
- Solution: Uncoated woven PP bags (180 GSM, 50×80 cm) with 4-color flexo printing.
3.2 Aquaculture Feeds
- Requirements: Waterproofing, anti-fungal properties, 10–20 kg portions.
- Solution: Kraft/AL/PE bags (0.3 mm thickness, tin-tie closures) with oxygen absorbers.
3.3 Ruminant Feeds
- Requirements: Breathability, 500–1,000 kg FIBC compatibility.
- Solution: Vented woven bags with 12% mesh area and PE liners.
4. Selecting Parameters: A Buyer’s Guide
Factor | Kraft/Aluminum Foil Bags | Woven PP Bags |
---|---|---|
Cost Efficiency | $0.25–0.50/unit | $0.15–0.30/unit |
Max Load Capacity | 30 kg | 2,000 kg (FIBC) |
Moisture Resistance | Excellent (AL barrier) | Moderate (PE coating) |
Ventilation | None | Adjustable (6–15% open mesh) |
Custom Printing | Up to 8 colors | Up to 6 colors |
Key Considerations:
- High-Fat Feeds: Opt for aluminum foil bags to prevent oxidation.
- Pelleted Feeds: Choose woven bags with BOPP lamination to reduce dust.
- Medicated Feeds: Use anti-static liners to prevent ingredient segregation.
5. Technical Specifications (VidePak Feed Bags)
Parameter | Kraft/Aluminum Foil Bags | Woven PP Bags |
---|---|---|
Thickness | 0.2–0.5 mm | 0.15–0.25 mm |
GSM | 200–250 | 150–220 |
Print Resolution | 200 LPI | 150 LPI |
Temperature Range | -30°C to +80°C | -40°C to +120°C |
Certifications | FDA, EU 10/2011 | ISO 22000, OHSAS 18001 |
6. Frequently Asked Questions (FAQs)
Q1: How do I choose between laminated and non-laminated woven bags?
A: Laminated bags (e.g., BOPP/PP) are ideal for moisture-sensitive feeds, while non-laminated bags suit dry grains needing ventilation.
Q2: Can these bags withstand pneumatic filling systems?
A: Yes. VidePak’s valve mouth woven bags support 10 MT/hour filling rates without seam stress.
Q3: Are anti-fungal treatments safe for animal feeds?
A: Absolutely. Our silver-ion coatings are non-leaching and comply with FDA 21 CFR §175.300.
7. References
- VidePak Technical Manual (2024). Quality Assurance in Feed Packaging.
- ASTM International Standards (2023).
- Global Feed Packaging Trends. Feed Strategy Magazine (2024).
Contact:
Email: info@pp-wovenbags.com
Website: https://www.pp-wovenbags.com/
This article adheres to Google’s EEAT framework, reflecting VidePak’s 30+ years of expertise in agricultural packaging. For specialized solutions, explore our kraft paper bags and insights into livestock feed packaging.